DARPA Kicks Off Program to Explore Space-Based Manufacturing
March 28, 2022 | DARPAEstimated reading time: 2 minutes
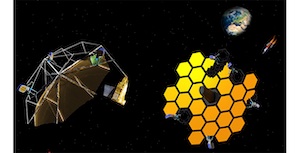
DARPA’s Novel Orbital Moon Manufacturing, Materials, and Mass Efficient Design (NOM4D) program is underway with eight industry and university research teams on contract. The selected teams are tasked to provide foundational proofs of concept in materials science, manufacturing, and design technologies to enable production of future space structures on orbit without the volume constraints imposed by launch. The vision is to ferry raw materials from Earth and collect lunar materials for on-orbit manufacturing. The NOM4D program does not involve building any structures on the surface of the moon. All manufacturing would be done in orbital construction facilities and the results utilized in orbital applications.
“Current space systems are all designed, built, and tested on Earth before being launched into a stable orbit and deployed to their final operational configuration,” said Bill Carter NOM4D program manager in DARPA’s Defense Sciences Office. “These constraints are particularly acute for large structures such as solar arrays, antennas and optical systems, where size is critical to performance. NOM4D aims to enable a new paradigm where future structures that support DoD space systems are built off-Earth using designs optimized for the space environment, shedding launch constraints. This would enable enhanced capability, improved robustness, operation in higher orbits, and future cislunar applications.”
For NOM4D, performers won’t be launching raw materials into space, collecting lunar samples or building structures on orbit. Any orbital experimentation would happen in potential follow-on efforts.
The following research teams are on contract to pursue a variety of challenges focused on two areas listed below:
1. In-space materials and manufacturing
- HRL Laboratories, LLC, Malibu, California, will be developing new die-less fabrication processes to make orbital mechanical elements and bonded structures on-orbit.
- University of Florida, Gainesville, Florida, will develop predictive material and correlative process models to enable on-orbit use of laser forming.
- University of Illinois Urbana-Champaign, Champaign, Illinois, is working to develop a high precision in-space composite forming process utilizing self-energized frontal polymerization.
- Physical Sciences, Inc., Andover, Massachusetts, will develop continuous fabrication of regolith-derived, glass-ceramic mechanical structures for use in large-scale orbital applications.
- Teledyne Scientific Company, LLC, Thousand Oaks, California, will build a comprehensive materials properties database of additive-modified regolith for use in controlled thermal expansion precision orbital structures.
2. Mass-efficient designs for in-space manufacturing
- University of Michigan, Ann Arbor, Michigan, will explore new design approaches to mass-efficient, high- precision, stable and resilient space structures based on metamaterial and metadamping concepts.
- Opterus Research and Development, Inc., Loveland, Colorado, will develop designs for extreme mass efficient large-scale structures optimized for resiliency and mobility.
- California Institute of Technology, Pasadena, California, will design novel tension and bending hybrid architectures and structural components with highly anisotropic mechanical response.
During Phase 1, program performers are tasked to meet stringent structural efficiency targets supporting a megawatt-class solar array. In Phase 2, teams are tasked to increase mass efficiency and demonstrate precision manufacturing for radio frequency (RF) reflectors. In the final phase, performers are tasked to demonstrate precision for infrared (IR) reflectors.
“Assuming current space technology trends continue, in 10-20 years we expect to see advances that will enable DoD to take full advantage of the NOM4D-developed technologies and capabilities,” Carter said. “This includes robotic manipulation sufficient to enable assembly of large structures from NOM4D-manufactured components, enhanced on-orbit mobility, and routine re-fueling of on-orbit assets. We also anticipate several other advantages, including more affordable space access and launch costs in LEO [low-earth orbit], GEO [geosynchronous orbit], cislunar space, and beyond.”
Testimonial
"We’re proud to call I-Connect007 a trusted partner. Their innovative approach and industry insight made our podcast collaboration a success by connecting us with the right audience and delivering real results."
Julia McCaffrey - NCAB GroupSuggested Items
Hungarian EMS Provider VIDEOTON Group Acquires Stake in Limtronik
07/23/2025 | VideotonVIDEOTON is a privately owned, family-run Hungarian contract manufacturer. As one of the top EU-based companies in this sector, VIDEOTON offers comprehensive electronic manufacturing services (EMS).
Cicor Grows Double-Digit Again and Creates Strong Foundation for Further Expansion
07/23/2025 | Cicor Technologies Ltd.In the first half of 2025, Cicor Group took a significant step towards its ambition of becoming the pan-European leader in its chosen markets as announced in the strategy 2028, expanding market presence into France and Spain.
Hon Hai Earns ISO 37301 Compliance Management System Certification
07/23/2025 | Hon Hai Precision Industry Co., Ltd.Hon Hai Technology Group, the world’s largest technology manufacturing platform service provider, announced that Hon Hai Precision Industry Co., Ltd. and Hon Hai Semiconductor Manufacturing Co., Ltd. have officially passed the ISO 37301 compliance management system international certification issued by the British Standards Institution (BSI ).
AI-driven MES Rewriting the Rules of Manufacturing Transformation
07/23/2025 | Francisco Almada Lobo, Critical ManufacturingThe Critical Manufacturing MES & Industry 4.0 International Summit, June 12–13, revealed a profound shift in how manufacturers approach digital transformation. AI-enabled execution systems are no longer a future ambition but are essential for navigating complexity and driving change.
SisTech Manufacturing Leads the Charge Against Electronic Component Obsolescence with Innovative Solutions
07/22/2025 | Globe NewswireSisTech Manufacturing recently rolled out advancements to its Electronic Manufacturing Services. These updates underscore the company's dedication to streamlining production processes while maintaining high quality and precision for their diverse clients.