-
-
News
News Highlights
- Books
Featured Books
- smt007 Magazine
Latest Issues
Current IssueWhat's Your Sweet Spot?
Are you in a niche that’s growing or shrinking? Is it time to reassess and refocus? We spotlight companies thriving by redefining or reinforcing their niche. What are their insights?
Moving Forward With Confidence
In this issue, we focus on sales and quoting, workforce training, new IPC leadership in the U.S. and Canada, the effects of tariffs, CFX standards, and much more—all designed to provide perspective as you move through the cloud bank of today's shifting economic market.
Intelligent Test and Inspection
Are you ready to explore the cutting-edge advancements shaping the electronics manufacturing industry? The May 2025 issue of SMT007 Magazine is packed with insights, innovations, and expert perspectives that you won’t want to miss.
- Articles
- Columns
- Links
- Media kit
||| MENU - smt007 Magazine
Dymax SpeedMask: Process Automation Shortens Throughput Times and Reduces Costs
July 25, 2022 | DymaxEstimated reading time: 2 minutes
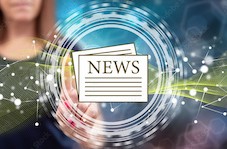
Dymax has helped MTU Aero Engines, Germany’s leading engine manufacturer in Munich, to successfully use Dymax SpeedMask® temporary maskants for its engine components. While in the past special areas of the components still had to be masked off manually to partially prepare them for e.g., thermal or abrasive surface treatments, now fully automatic dispensers apply the light-curing material to the component in the shortest possible time with high precision.
Surface treatment, for example thermal spraying, is a key manufacturing process used on aero engine parts. In this process, certain surfaces must be temporarily masked with millimeter precision to protect them from inadvertent treatment during the process. For a long time, maskants were manually applied by affixing adhesive tapes, silicone rings, masks, or metal covers, all of which required a great deal of time and care. Growing product demand and increasingly complex shapes made it challenging for MTU to provide a precise and cost-effective temporary protection for sensitive component surfaces. When Thomas Kaltenecker, production planner at MTU Aero Engines, became acquainted with Dymax's light-curable maskants, he was certain the material would reduce challenges and improve the overall process. Dymax SpeedMask® maskants are easy to apply even to the most complex shapes and geometries and offer excellent properties to withstand high temperatures during finishing processes. Moreover, Dymax maskants can be seamlessly integrated into automated dispense and curing systems – in other words, exactly what MTU was looking for.
Programmable robotic arms, together with the Dymax SpeedMask®, perform this difficult task with ease. With various dispensers, the gel-like material is applied fully automatic with high precision to the surface or even sprayed to cover a larger area of the component. A brief exposure to UV light at the proper intensity and wavelength ensures that the material cures within seconds. The masking can be removed just as quickly after going through the various surface treatments without leaving any residue. This not only saves manufacturing time and production costs, but also has a positive effect on the sustainability of the process, as the error rate is reduced to nearly zero tolerance levels.
Thomas Kaltenecker enthusiastically stated, "Several hundred components in our portfolio undergo various surface treatment processes during their production, such as thermal coating, shot peening, electroplating, etc. The respective Dymax SpeedMask® masking processes can be adapted quickly and easily for this, resulting in significant time savings in our production process."
Virginia Hogan, Senior Global Business Development Manager at Dymax, added, "We are delighted that Dymax was able to support a total solution for MTU Aero Engines. Our application engineers, system integration, and internal sales teams worked together to not only provide a great maskant but deliver a fully automated dispense and curing machine. We are happy to continue to support MTU in making them more capable and their process more efficient."
Suggested Items
SMT007 Magazine July—What’s Your Competitive Sweet Spot?
07/01/2025 | I-Connect007 Editorial TeamAre you in a niche that’s growing or shrinking? Is it time to reassess and refocus? We spotlight companies thriving by redefining or reinforcing their niche—what are their insights? In the July 2025 issue of SMT007 Magazine, we spotlight companies thriving by redefining or reinforcing their niche and offer insights to help you evaluate your own.
Smarter Machines Use AOI to Transform PCB Inspections
06/30/2025 | Marcy LaRont, PCB007 MagazineAs automated optical inspection (AOI) evolves from traditional end-of-process inspections to proactive, in-line solutions, the integration of AI and machine learning is revolutionizing defect reduction and enhancing yields, marking a pivotal shift in how quality is managed in manufacturing.
Magnalytix and Foresite to Host Technical Webinar on SIR Testing and Functional Reliability
06/26/2025 | MAGNALYTIXMagnalytix, in collaboration with Foresite Inc., is pleased to announce an upcoming one-hour Webinar Workshop titled “Comparing SIR IPC B-52 to Umpire 41 Functional & SIR Test Method.” This session will be held on July 24, 2025, and is open to professionals in electronics manufacturing, reliability engineering, and process development seeking insights into new testing standards for climatic reliability.
The Death of the Microsection
06/26/2025 | Bob Neves, Reliability Assessment Solutions, Inc.I got my start out of college grinding and polishing PCB microsections. My thumbs are a bit arthritic today because of the experience (microsection grinders know what I mean). Back then, via structures were rather large, and getting to the center in six steps of grinding and polishing was easy compared to what my team has been doing recently at the lab.
Specially Developed for Laser Plastic Welding from LPKF
06/25/2025 | LPKFLPKF introduces TherMoPro, a thermographic analysis system specifically developed for laser plastic welding that transforms thermal data into concrete actionable insights. Through automated capture, evaluation, and interpretation of surface temperature patterns immediately after welding, the system provides unprecedented process transparency that correlates with product joining quality and long-term product stability.