Altair Presents Open, Flexible, and Scalable Total Digital Twin Solution
October 7, 2022 | AltairEstimated reading time: 2 minutes
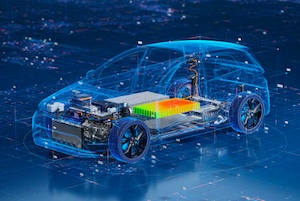
Altair, a global leader in computational science and artificial intelligence (AI), announced the launch of its broad digital twin solution that features the market’s most connected, cross-functional capabilities that can be deployed through any and every stage of a product lifecycle.
"Altair offers the market’s premier digital twin solution that can transform the way people and organizations design, develop, implement, and improve products and processes,” said Sam Mahalingam, chief technology officer, Altair. “Moving forward, we will continue establishing our digital twin leadership to provide further democratized, more accessible digital twin solutions.”
Fostering Evolution at Any Stage of a Product Lifecycle
Combining Altair’s leading simulation, high-performance computing (HPC), AI, data analytics, and Internet of Things (IoT) capabilities, companies can apply digital twin technology at any stage of the product lifecycle — from concept through in-service — as part of a cross-functional, enterprise-wide effort that advances collaboration and eliminates departmental silos. Additionally, Altair’s open, vendor-agnostic digital twin solution is the premier offering that gives customers the flexibility to run Altair software anywhere – whether on-site, in the cloud, hybrid, or via plug-and-play appliances – and the freedom to choose from a comprehensive toolset through a cost-effective, units-based licensing model called Altair Units.
Pre-Production
In the pre-production stage, Altair offers toolsets for “as-specified” twins, which cover system requirements, development, validation, real-world performance prediction, streamlined mechatronic product development, and more. This allows teams to design, analyze, and optimize systems and performance without expensive physical prototypes. It also enables teams to converge multiphysics simulation with advanced HPC, AI, and data analytics capabilities in a unified environment.
Featured as-specified twin tools include Altair Activate, Inspire, Drive, HyperWorks, PollEx, Flux, Compose, Feko, PSIM, and XLDyn (via the Altair Partner Alliance).
Post-Production
In the post-production stage, Altair has toolsets for “as-built” and “as-manufactured” twins. As-built twins allow teams to evaluate advanced virtual system dynamics under what-if scenarios, deploy reduced order modeling (ROM), detect design sensitivities, and resolve test failures. As-manufactured twins allow teams to evaluate integrated software, processors and hardware involved with systems such as human driver controls, ergonomics, immersion, virtual reality, and more. These twins help teams simulate realistic and unexpected events, improve workability and operation windows, and produce high-fidelity displays of innovations in interactive and realistic environments.
Featured as-built and as-manufactured twin tools include Altair Embed, MotionSolve, HyperStudy, Panopticon, Design Explorer, and Vortex Studio (via the Altair Partner Alliance).
In-Service Systems
Lastly, Altair’s digital twin tools for “as-sustained” twins cover predictive analytics and predictive maintenance of manufactured products that are in service. Teams can leverage real-time data stream analytics and machine learning to determine a system’s remaining useful life (RUL), trigger insights based on anomaly detection, refine system performance, deliver optimized maintenance routines, and much more.
Featured tools for as-sustained twins include Altair RapidMiner, SmartWorks, SLC, Monarch, and Knowledge Studio.
Users can take advantage of Altair’s end-to-end, holistic solutions and digital twin consulting team to help accelerate digital twin adoption in industries as diverse as aerospace, telecommunications, banking, financial services, manufacturing, energy, and electronics. Altair solutions allow organizations to do things like predict and optimize electric battery performance in buses, improve wind turbine efficiency, analyze and optimize the performance of an airborne radar system, analyze credit risk, monitor and detect financial fraud, design the ideal coffee machine, conduct prescriptive performance optimization and predictive maintenance of consumer products, and more.
Suggested Items
Meet the Author Podcast: Martyn Gaudion Unpacks the Secrets of High-Speed PCB Design
07/10/2025 | I-Connect007In this special Meet the Author episode of the On the Line with… podcast, Nolan Johnson sits down with Martyn Gaudion, signal integrity expert, managing director of Polar Instruments, and three-time author in I-Connect007’s popular The Printed Circuit Designer’s Guide to... series.
Intervala Hosts Employee Car and Motorcycle Show, Benefit Nonprofits
08/27/2024 | IntervalaIntervala hosted an employee car and motorcycle show, aptly named the Vala-Cruise and it was a roaring success! Employees had the chance to show off their prized wheels, and it was incredible to see the variety and passion on display.
KIC Honored with IPC Recognition for 25 Years of Membership and Contributions to Electronics Manufacturing Industry
06/24/2024 | KICKIC, a renowned pioneer in thermal process and temperature measurement solutions for electronics manufacturing, is proud to announce that it has been recognized by IPC for 25 years of membership and significant contributions to electronics manufacturing.
Boeing Starliner Spacecraft Completes Successful Crewed Docking with International Space Station
06/07/2024 | BoeingNASA astronauts Barry "Butch" Wilmore and Sunita "Suni" Williams successfully docked Boeing's Starliner spacecraft to the International Space Station (ISS), about 26 hours after launching from Cape Canaveral Space Force Station.
KIC’s Miles Moreau to Present Profiling Basics and Best Practices at SMTA Wisconsin Chapter PCBA Profile Workshop
01/25/2024 | KICKIC, a renowned pioneer in thermal process and temperature measurement solutions for electronics manufacturing, announces that Miles Moreau, General Manager, will be a featured speaker at the SMTA Wisconsin Chapter In-Person PCBA Profile Workshop.