-
-
News
News Highlights
- Books
Featured Books
- pcb007 Magazine
Latest Issues
Current IssueThe Hole Truth: Via Integrity in an HDI World
From the drilled hole to registration across multiple sequential lamination cycles, to the quality of your copper plating, via reliability in an HDI world is becoming an ever-greater challenge. This month we look at “The Hole Truth,” from creating the “perfect” via to how you can assure via quality and reliability, the first time, every time.
In Pursuit of Perfection: Defect Reduction
For bare PCB board fabrication, defect reduction is a critical aspect of a company's bottom line profitability. In this issue, we examine how imaging, etching, and plating processes can provide information and insight into reducing defects and increasing yields.
Voices of the Industry
We take the pulse of the PCB industry by sharing insights from leading fabricators and suppliers in this month's issue. We've gathered their thoughts on the new U.S. administration, spending, the war in Ukraine, and their most pressing needs. It’s an eye-opening and enlightening look behind the curtain.
- Articles
- Columns
- Links
- Media kit
||| MENU - pcb007 Magazine
Optimize Your Etcher for Best Image Quality
November 3, 2022 | Christopher Bonsell, ChemcutEstimated reading time: 1 minute
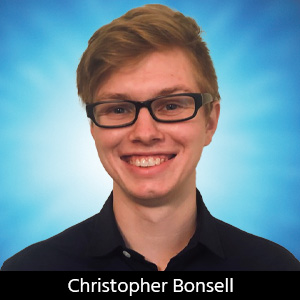
When it comes to obtaining high-quality images, many different factors come into play. Typically, most of these factors come down to your imaging equipment and cleanroom; however, there are factors involved in the etching process that can affect the quality of your image. Here are five steps to ensure your etching process is optimized for the best image quality.
1. Be wary of undercut.
When you are etching to obtain your circuitry patterns on a PCB, beware of undercut. Due to your solution’s etch factor—the ratio of sideways etch to downward etch—your image will need to compensate any change and variation that can arise. Naturally, when you create a line with a photoresist to make a feature, the outcome of that feature will be smaller because of the sideways etching. PCB designs typically account for this, but if you are working with thicker copper layers for your PCBs, you will have to be cautious and ensure that the sideways etch does not impact the features you desire.
2. Monitor your etchant quality.
Maintaining consistency of your etch chemistry is the key to ensuring your etcher gives a quality image. As you etch panels, your etchant will decline in quality because it loses reaction potential (from the depletion of reactants), and with that, you will pick up contaminants. To prevent this from affecting your etching process, you will need to implement process controls to maintain the properties of your etchant. Depending on the etching solution you utilize, the factors you need to control will vary. If you are unsure how to monitor or maintain your etch process, it is best to seek experienced help and consult your etch equipment manufacturer.
3. Clean your nozzles regularly.
As I mentioned, etching panels will introduce contaminants into your etching bath. With this, your nozzles can become clogged with debris. Frequently cleaning your nozzles is an easy measure you can take to prevent debris from affecting etch quality. Doing this will ensure that your panels receive a consistent spray pattern throughout the etch chamber.
To read this entire article, which appeared in the October 2022 issue of PCB007 Magazine, click here.
Suggested Items
The Evolution of Picosecond Laser Drilling
06/19/2025 | Marcy LaRont, PCB007 MagazineIs it hard to imagine a single laser pulse reduced not only from nanoseconds to picoseconds in its pulse duration, but even to femtoseconds? Well, buckle up because it seems we are there. In this interview, Dr. Stefan Rung, technical director of laser machines at Schmoll Maschinen GmbH, traces the technology trajectory of the laser drill from the CO2 laser to cutting-edge picosecond and hybrid laser drilling systems, highlighting the benefits and limitations of each method, and demonstrating how laser innovations are shaping the future of PCB fabrication.
Day 2: More Cutting-edge Insights at the EIPC Summer Conference
06/18/2025 | Pete Starkey, I-Connect007The European Institute for the PCB Community (EIPC) summer conference took place this year in Edinburgh, Scotland, June 3-4. This is the third of three articles on the conference. The other two cover Day 1’s sessions and the opening keynote speech. Below is a recap of the second day’s sessions.
Day 1: Cutting Edge Insights at the EIPC Summer Conference
06/17/2025 | Pete Starkey, I-Connect007The European Institute for the PCB Community (EIPC) Summer Conference took place this year in Edinburgh, Scotland, June 3-4. This is the second of three articles on the conference. The other two cover the keynote speeches and Day 2 of the technical conference. Below is a recap of the first day’s sessions.
Preventing Surface Prep Defects and Ensuring Reliability
06/10/2025 | Marcy LaRont, PCB007 MagazineIn printed circuit board (PCB) fabrication, surface preparation is a critical process that ensures strong adhesion, reliable plating, and long-term product performance. Without proper surface treatment, manufacturers may encounter defects such as delamination, poor solder mask adhesion, and plating failures. This article examines key surface preparation techniques, common defects resulting from improper processes, and real-world case studies that illustrate best practices.
RF PCB Design Tips and Tricks
05/08/2025 | Cherie Litson, EPTAC MIT CID/CID+There are many great books, videos, and information online about designing PCBs for RF circuits. A few of my favorite RF sources are Hans Rosenberg, Stephen Chavez, and Rick Hartley, but there are many more. These PCB design engineers have a very good perspective on what it takes to take an RF design from schematic concept to PCB layout.