-
-
News
News Highlights
- Books
Featured Books
- pcb007 Magazine
Latest Issues
Current IssueThe Hole Truth: Via Integrity in an HDI World
From the drilled hole to registration across multiple sequential lamination cycles, to the quality of your copper plating, via reliability in an HDI world is becoming an ever-greater challenge. This month we look at “The Hole Truth,” from creating the “perfect” via to how you can assure via quality and reliability, the first time, every time.
In Pursuit of Perfection: Defect Reduction
For bare PCB board fabrication, defect reduction is a critical aspect of a company's bottom line profitability. In this issue, we examine how imaging, etching, and plating processes can provide information and insight into reducing defects and increasing yields.
Voices of the Industry
We take the pulse of the PCB industry by sharing insights from leading fabricators and suppliers in this month's issue. We've gathered their thoughts on the new U.S. administration, spending, the war in Ukraine, and their most pressing needs. It’s an eye-opening and enlightening look behind the curtain.
- Articles
- Columns
- Links
- Media kit
||| MENU - pcb007 Magazine
Rogers: Bringing New Materials to Light
December 12, 2022 | Pete Starkey, I-Connect007Estimated reading time: 7 minutes
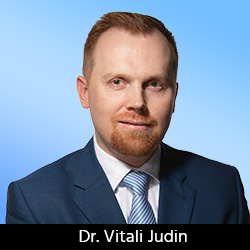
I stopped by the Rogers booth at electronica to hear from Dr. Vitali Judin, the new business development manager at Rogers, on how the well-respected company is making a splash with new high frequency materials meant to address the rapidly evolving needs of the additive manufacturing sector. Rogers determined that digital light processing (DLP) 3D printing technique brought the combination of speed and resolution necessary to make additive manufacturing reasonably scalable, then partnered with Fortify to bring the processing consistency needed for the RF industry. With so many potential applications for this newly adapted technology, Rogers hopes to create a full slate of additive manufacturing materials for use in this sector and beyond.
Pete Starkey: I’m delighted to talk about some of Rogers’s new products with Dr. Vitali Judin here at electronica. Vitali, it’s lovely to meet you and thank you for making me feel so welcome.
Dr. Vitali Judin: Good morning, Pete. Thank you very much for this introduction. I’m happy to chat with you about our new products and developments.
Starkey: Why don’t you walk us through what’s “new” with these new products?
Judin: First, let me tell you a little about our background. Rogers is a well-established high frequency laminate and prepreg manufacturer. This time we literally went out of plane.
Starkey: Rogers has a well-established identity in the industry.
Judin: Exactly, especially in the high frequency world. At the end of last year, we started to dip into the additive manufacturing sector. We saw a gap in 3D printing processes with high potential for semi-mass production compatibility, and we wanted to address that need by creating dedicated materials for high frequency applications. What do I mean by that? There are multiple 3D printing techniques to realize 3D parts; one of the most well-known is fused deposition modeling (FDM), where you create your part pixel by pixel by melting individual filaments of thermoplastic. That process takes time, of course, and that’s why we wanted to use specific technology to allow those processes to run in parallel, thereby creating your parts much faster—that’s DLP.
DLP, or “digital light processing,” is where you use a fluid polymer instead of fiber to build your whole plane simultaneously in one single shot. To break it down, you make a shot with a specific UV light and polymerize the structure. Then you move your building plate in the Z direction and do the next shot and next shot so that the whole building plane, which might contain 20, 100, or 1,000 parts at the same time, is built up very quickly. In the time it would take you to build one part with FDM using filament, you can build—depending on the size of your lenses—100 or even 1,000 parts in a single production run.
Starkey: Although this technology has existed for many years, you’ve adapted it using new chemistries to meet the need you identified in this sector.
Judin: That’s correct. While the technology is not new, we are stepping into a new material domain. In the filament world, we had plenty of options for high frequency capable materials, but they are not mass production compatible. In the DLP world, there was a gap of the right set of materials with RF properties. Rogers is well known for consistently stable and reliable high frequency materials, so we created a resin called Radix™ printable dielectric, which has a dielectric constant of 2.8 and a very low dissipation factor, to specifically meet the needs of this technology.
Starkey: Yes, I understand your specialist capabilities in choosing the right materials for application. What are typical applications for these structures?
Judin: If you pair a great low loss material with DLP technology, you get to use some very specific manufacturing techniques. By partnering with Fortify, a company that handles high viscosity and highly filled ceramic components, as well as highly filled microparticle polymers and resins, we’ve figured out that we can create specific meshed structures—lattices. To do this, we allow some air inside of the meshed structure by very precisely controlling the fraction of air we introduce into the material.
This allows you to create a kind of low dielectric constant spacer by replicating unit cells with some fraction of air. These small unit cells can have some well-known topologies. For example, there’s the simple cubic unit cell. Then there’s also a gyroid cell, which you can replicate; if you change the thickness of the wall inside a gyroid cell, you can create nice gradients of your dielectric constant inside your three-dimensional part. A well-known example is a Luneburg lens. The Luneburg lens is a spherical object that has a gradient from inside to outside in a specific dielectric constant range. This form allows you to create a high frequency lens very easily, and through this technology, the manufacturing process is easy too. If you tried to create these structures using conventional techniques, it would be extremely difficult.
Starkey: I imagine it would be. These samples that we have in front of us appear to be very precisely engineered using honeycomb structures that demonstrate a great deal of control over the structure’s geometry.
Judin: Absolutely. These parts we have here on the table are examples of these low dielectric constant spacers and other kinds of spacers. You can create mechanical structures that can carry some mechanical parts, like antenna patches, and have a dielectric constant of 1.15–1.2. That is created by this structure—what we are seeing here is a gyroid structure.
Starkey: We understand the nature of the material, and the technology used to create these structures. What is the next stage? After you’ve made this, how do you process it?
Judin: In the high frequency world, the reliability and the constancy of the parameters and electric values is extremely important. We can create these gyroid structures by controlling the porosity and air fraction inside of the material, which plays an important role in the generation of the final effective dielectric value of your part. So that’s why we’ve partnered with Fortify; they have an extremely reliable 3D printer with a proprietary material mixing system and great software that allows us to convert and control the dielectric constant values, thereby converting the simulated dielectric constant directly to the structure as both a fraction of air and a fraction of the material.
Starkey: Yeah, and the material itself is not just a straightforward polymer, it’s a filled material.
Judin: That’s right.
Starkey: Part of the skill, then, is to maintain the uniformity of the dispersion of the filler.
Judin: Absolutely right. You need to control multiple parameters when printing your part, because if you are not mixing this composite polymer material, you can create adverse effects like sedimentation, where your part will have a different content of particles in the beginning of the print and a much lower content of the particles at the end of the print. That’s why you need to have your printing process well under control, and here we rely on Fortify’s technology, along with our years of experience in different domains and application fields. But beyond these meshed structures and low Dk structures, you also create full resin parts like conical cylinders; you can even find a way to put metalized structures on the surface of this objects to create planar antennas, conformal antennas, or other conformal structures, so there are plenty of different application fields for this technology.
Starkey: Is this concept now on the open market, or is it still in development?
Judin: This material that we have here, Radix 2.8 Dk printable dielectric, is already released, and we’ve already seen a scale up in certain applications, especially in the aerospace and defense domains. We’ve seen a lot of movement, but we need to educate our customer and the customer needs to educate us. We’re providing a new tool for the high frequency engineer’s toolbox. We explain the initial steps and then they immediately run a couple of simulations.
Starkey: Yeah. That’s a good two-way application engineering challenge.
Judin: Exactly. We get a couple of questions back and then we need to run some additional tests. We are currently in the late phase of this learning curve. We did a lot of interesting evaluations and now understand our material much better. Our aim at Rogers is to create a full portfolio of additive manufacturing materials with different dielectric constants, and we’re well on our way to achieving that goal.
Starkey: Well, Vitali, I’ve found these past few minutes extremely fascinating, and I thank you for such a thorough explanation of these exciting new products and the techniques you’ve used to create them.
Judin: I appreciate it, Pete. Thank you very much, and have a good day.
Starkey: It’s been a great pleasure to meet you. Thank you.
Suggested Items
S&K Aerospace Awarded Major Contract Under DLA Maritime Acquisition Advancement Program
07/02/2025 | BUSINESS WIRES&K Aerospace, LLC has been awarded a significant contract under the Defense Logistics Agency’s (DLA) Maritime Acquisition Advancement Program, managed by the U.S. Naval Supply Command - Weapon Systems Support (NAVSUP WSS) in Mechanicsburg, PA.
Green Circuits to Exhibit Full-Service Electronics Manufacturing Solutions at 2025 SMD Symposium
07/02/2025 | Green CircuitsGreen Circuits, a full-service Electronics Manufacturing Services (EMS) partner to leading OEMs, is pleased to announce its participation in the 2025 SMD Symposium, taking place August 5-7 at the Von Braun Center in Huntsville, Alabama.
I-Connect007 Editor’s Choice: Five Must-Reads for the Week
06/27/2025 | Nolan Johnson, I-Connect007While news outside our industry keeps our attention occupied, the big news inside the industry is the rechristening of IPC as the Global Electronics Association. My must-reads begins with Marcy LaRont’s exclusive and informative interview with Dr. John Mitchell, president and CEO of the Global Electronics Association. For designers, have we finally reached the point in time where autorouters will fulfill their potential?
Knocking Down the Bone Pile: Tin Whisker Mitigation in Aerospace Applications, Part 3
06/25/2025 | Nash Bell -- Column: Knocking Down the Bone PileTin whiskers are slender, hair-like metallic growths that can develop on the surface of tin-plated electronic components. Typically measuring a few micrometers in diameter and growing several millimeters in length, they form through an electrochemical process influenced by environmental factors such as temperature variations, mechanical or compressive stress, and the aging of solder alloys.
RTX, the Singapore Economic Development Board Sign MOU Outlining 10-year Growth Roadmap
06/20/2025 | RTXRTX and the Singapore Economic Development Board (EDB) have signed a Memorandum of Understanding (MoU) which outlines a 10-year roadmap to further long-term strategic collaboration in Singapore.