-
- News
- Books
Featured Books
- smt007 Magazine
Latest Issues
Current IssueWhat's Your Sweet Spot?
Are you in a niche that’s growing or shrinking? Is it time to reassess and refocus? We spotlight companies thriving by redefining or reinforcing their niche. What are their insights?
Moving Forward With Confidence
In this issue, we focus on sales and quoting, workforce training, new IPC leadership in the U.S. and Canada, the effects of tariffs, CFX standards, and much more—all designed to provide perspective as you move through the cloud bank of today's shifting economic market.
Intelligent Test and Inspection
Are you ready to explore the cutting-edge advancements shaping the electronics manufacturing industry? The May 2025 issue of SMT007 Magazine is packed with insights, innovations, and expert perspectives that you won’t want to miss.
- Articles
- Columns
- Links
- Media kit
||| MENU - smt007 Magazine
Book Excerpt: 'The Electronics Industry’s Guide to… The Evolving PCB NPI', Chapter 3
January 4, 2023 | I-Connect007 Editorial TeamEstimated reading time: 2 minutes
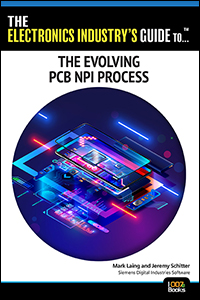
Chapter 3: Streamlining Data Preparation
With the need to move design data efficiently into manufacturing for assembly and test purposes, starting from a single source of intelligent data seems to be obvious. However, with different applications with different capabilities this can be difficult to achieve. Real-world support for any format can vary between machine and software vendors. The optimal goal should be to create a single digital twin of the product upfront regardless of the downstream applications that need that data.
If we consider the PCB and the parts being placed on it, their data should have significant commonality across the many steps in PCB assembly and test. Typically, we find that process and test engineers think there is much more machine-specific data across their lines than there really is in practice.
Solutions exist in the market that can manage this common data and then deliver machine-specific information to the machine software as needed, on demand. In this way, the factory can maintain the common data, but, more importantly, they have a common part library data that is independent of the line. Remember when we talked about the move from mixed vendor lines to single vendor lines and mixed-line factories? The ability to manage part data in this context is key to efficiently streamlining the NPI phase.
First, let’s start with the typical data preparation tasks that form the base for a typical NPI flow. Being able to accurately import the source layout CAD data is an important first step. As we discussed in chapter one, ODB++ and IPC 2581 provide a common, standardized data format for layout information. However, not all CAD data is the same, even in the context of one format such as ODB++. This is because different designers use unique conventions in their source libraries. The position and rotation of each component placement can be inconsistent for any single format because each component location is based on the definition of the library cell that it references. Why does this decrease efficiency?
Consider that, during the SMT process, the machine picks a component up from a feeder and positions that component, rotating it before releasing it on the board. What the machine considers for the rotation is based on its perspective and the orientation of the part in the feeder. However, what the design software considers for position and orientation is based on an arbitrarily defined cell library. The variations in that cell library are a result of the environment that the designer works in. What is the origin of the cell? Is it pin 1? Is it the middle of the part? Is it a corner on the cell? What is the rotation of the part at 0 degrees? Is it pin 1 to the left or to the right? What about IC components with many pins? Is pin 1 in the lower right corner, or maybe the lower left?
See Figure 3.1 for how a designer may have defined their source footprint, which is what is used for placement position and angle. We have a polarized part here but pin 2 is associated with the silkscreen indicator.
To continue reading this chapter of The Electronics Industry's Guide to... The Evolving PCB NPI Process, download your free book today!
Suggested Items
The Global Electronics Association Releases IPC-8911: First-Ever Conductive Yarn Standard for E-Textile Application
07/02/2025 | Global Electronics AssociationThe Global Electronics Association announces the release of IPC-8911, Requirements for Conductive Yarns for E-Textiles Applications. This first-of-its-kind global standard establishes a clear framework for classifying, designating, and qualifying conductive yarns—helping to address longstanding challenges in supply chain communication, product testing, and material selection within the growing e-textiles industry.
IPC-CFX, 2.0: How to Use the QPL Effectively
07/02/2025 | Chris Jorgensen, Global Electronics AssociationIn part one of this series, we discussed the new features in CFX Version 2.0 and their implications for improved inter-machine communication. But what about bringing this new functionality to the shop floor? The IPC-CFX-2591 QPL is a powerful technical resource for manufacturers seeking CFX-enabled equipment. The Qualified Product List (QPL) helps streamline equipment selection by listing models verified for CFX compliance through a robust third-party virtual qualification process.
Advancing Aerospace Excellence: Emerald’s Medford Team Earns Space Addendum Certification
06/30/2025 | Emerald TechnologiesWe’re thrilled to announce a major achievement from our Medford, Oregon facility. Andy Abrigo has officially earned her credentials as a Certified IPC Trainer (CIT) under the IPC J-STD-001 Space Addendum, the leading industry standard for space and military-grade electronics manufacturing.
Magnalytix and Foresite to Host Technical Webinar on SIR Testing and Functional Reliability
06/26/2025 | MAGNALYTIXMagnalytix, in collaboration with Foresite Inc., is pleased to announce an upcoming one-hour Webinar Workshop titled “Comparing SIR IPC B-52 to Umpire 41 Functional & SIR Test Method.” This session will be held on July 24, 2025, and is open to professionals in electronics manufacturing, reliability engineering, and process development seeking insights into new testing standards for climatic reliability.
IPC Rebrands as Global Electronics Association: Interview With Dr. John W. Mitchell
06/22/2025 | Marcy LaRont, I-Connect007Today, following a major announcement, IPC is embracing the rapid advancement of technology with a bold decision to change its name to the Global Electronics Association. This name more accurately reflects the full breadth of its work and the modern realities of electronics manufacturing. In this exclusive interview, Global Electronics Association President and CEO Dr. John W. Mitchell shares the story behind the rebrand: Why now, what it means for the industry, and how it aligns with the organization’s mission.