-
- News
- Books
Featured Books
- smt007 Magazine
Latest Issues
Current IssueWhat's Your Sweet Spot?
Are you in a niche that’s growing or shrinking? Is it time to reassess and refocus? We spotlight companies thriving by redefining or reinforcing their niche. What are their insights?
Moving Forward With Confidence
In this issue, we focus on sales and quoting, workforce training, new IPC leadership in the U.S. and Canada, the effects of tariffs, CFX standards, and much more—all designed to provide perspective as you move through the cloud bank of today's shifting economic market.
Intelligent Test and Inspection
Are you ready to explore the cutting-edge advancements shaping the electronics manufacturing industry? The May 2025 issue of SMT007 Magazine is packed with insights, innovations, and expert perspectives that you won’t want to miss.
- Articles
- Columns
- Links
- Media kit
||| MENU - smt007 Magazine
Stop Over-specifying Your Materials
May 25, 2023 | I-Connect007 Editorial TeamEstimated reading time: 3 minutes
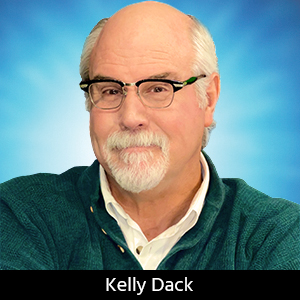
Columnist Kelly Dack has had a pretty wide range of experiences. As a PCB designer, he has sat behind the desk at an NPI company, an OEM, a fabricator, and now an EMS provider. We asked him to share a few thoughts on the materials selection process and how it could be improved.
Kelly also explains how overly zealous PCB designers make things too complicated by over-specifying their materials, which leads to confusion once the board goes to volume production overseas. Are you over-constraining your material choices?
Andy Shaughnessy: Kelly, what is your process for material selection? Walk us through it.
Kelly Dack: Sure. I actually wrote a guideline for our customers that explains the material selection process. As mentioned, over-specification in the EMS realm is rampant and problematic from the standpoint of scaling products to volume overseas. This guide has a section on laminated materials that includes a simple, tried-and-true material specification. It says, “Materials: laminated glass epoxy resin type FR-4 series or equivalent per IPC-4101 with a Tg of greater than or equal to xxx.” This is a number that we can modify. We say, for instance, 170°C, and a Td (time to delamination) temperature of greater than 3XX°C. Those are all movable numbers that designers can edit.
That’s how we specify our laminate materials for printed circuit boards, unless the performance criteria dictates that it needs to go further and get more specific—for example, high-performance signal integrity constraints, impedance control, or exotic materials. But otherwise, FR-4 laminates cover 85–95% of our customers’ design requirements.
Shaughnessy: Where do designers typically go to find this information? What documents or guidelines should they use?
Dack: Many designers use their company’s documentation template or go to their elders and learn through knowledge that has been passed down. I just went through a bunch of our customers’ designs and fabrication drawings, and I found plenty of examples of customer material specification. Many of them call out a specific IPC-4101 slash number, and it’s usually the same slash number each time. It’s either 4101/26 or /21.
Shaughnessy: IPC has said that slash sheets were not ever meant for designers to use; they’re mainly a way for PCB supplier purchasing and marketing departments to communicate with buyers.
Dack: I’m glad to hear that confirmation as it was my understanding as well. This all came from the MIL-S-13949 spec back in the mil-spec days, most of which has been replaced by IPC standards. But we are seeing some of our customers’ designs specifying laminates by using slash numbers and I get the feeling it’s just because of tribal knowledge. If you look at most of the designs, they appear to be basic, not really requiring a specific material. The board would work fine with a generic glass-epoxy laminate because it has no impedance control or performance criteria. We just print and etch some copper onto it, create a circuit, and it moves electrons.
It’s usually only when we get into the super high-speed design in the gigahertz range where we have to start thinking about loss tangents and permittivities. Here’s the challenge: How much do you constrain? If you’re building your PCB design down at the local prototype shop, which will build a board any way you want, everybody seems fat and happy. But when you want to build 1 million boards, you must introduce a low-cost constraint because you can’t pay $1,000 a board and make a profit. You scale to volume to get cost savings. To realize maximum cost savings, this has always been done offshore. But designers must realize that offshore suppliers don’t have access to all the materials and capabilities that U.S. prototype companies have. Over-specification of laminate materials by composition, performance characteristics, or a trademarked source creates a terrible, but avoidable ordering situation, putting quotes on hold every single day. The simple fact is that it causes our offshore PCB suppliers to request and obtain approval for material substitutions before they can proceed.
To read this entire conversation, which appeared in the May 2023 issue of Design007 Magazine, click here.
Suggested Items
The Evolution of Picosecond Laser Drilling
06/19/2025 | Marcy LaRont, PCB007 MagazineIs it hard to imagine a single laser pulse reduced not only from nanoseconds to picoseconds in its pulse duration, but even to femtoseconds? Well, buckle up because it seems we are there. In this interview, Dr. Stefan Rung, technical director of laser machines at Schmoll Maschinen GmbH, traces the technology trajectory of the laser drill from the CO2 laser to cutting-edge picosecond and hybrid laser drilling systems, highlighting the benefits and limitations of each method, and demonstrating how laser innovations are shaping the future of PCB fabrication.
Day 2: More Cutting-edge Insights at the EIPC Summer Conference
06/18/2025 | Pete Starkey, I-Connect007The European Institute for the PCB Community (EIPC) summer conference took place this year in Edinburgh, Scotland, June 3-4. This is the third of three articles on the conference. The other two cover Day 1’s sessions and the opening keynote speech. Below is a recap of the second day’s sessions.
Day 1: Cutting Edge Insights at the EIPC Summer Conference
06/17/2025 | Pete Starkey, I-Connect007The European Institute for the PCB Community (EIPC) Summer Conference took place this year in Edinburgh, Scotland, June 3-4. This is the second of three articles on the conference. The other two cover the keynote speeches and Day 2 of the technical conference. Below is a recap of the first day’s sessions.
Preventing Surface Prep Defects and Ensuring Reliability
06/10/2025 | Marcy LaRont, PCB007 MagazineIn printed circuit board (PCB) fabrication, surface preparation is a critical process that ensures strong adhesion, reliable plating, and long-term product performance. Without proper surface treatment, manufacturers may encounter defects such as delamination, poor solder mask adhesion, and plating failures. This article examines key surface preparation techniques, common defects resulting from improper processes, and real-world case studies that illustrate best practices.
RF PCB Design Tips and Tricks
05/08/2025 | Cherie Litson, EPTAC MIT CID/CID+There are many great books, videos, and information online about designing PCBs for RF circuits. A few of my favorite RF sources are Hans Rosenberg, Stephen Chavez, and Rick Hartley, but there are many more. These PCB design engineers have a very good perspective on what it takes to take an RF design from schematic concept to PCB layout.