-
-
News
News Highlights
- Books
Featured Books
- pcb007 Magazine
Latest Issues
Current IssueThe Hole Truth: Via Integrity in an HDI World
From the drilled hole to registration across multiple sequential lamination cycles, to the quality of your copper plating, via reliability in an HDI world is becoming an ever-greater challenge. This month we look at “The Hole Truth,” from creating the “perfect” via to how you can assure via quality and reliability, the first time, every time.
In Pursuit of Perfection: Defect Reduction
For bare PCB board fabrication, defect reduction is a critical aspect of a company's bottom line profitability. In this issue, we examine how imaging, etching, and plating processes can provide information and insight into reducing defects and increasing yields.
Voices of the Industry
We take the pulse of the PCB industry by sharing insights from leading fabricators and suppliers in this month's issue. We've gathered their thoughts on the new U.S. administration, spending, the war in Ukraine, and their most pressing needs. It’s an eye-opening and enlightening look behind the curtain.
- Articles
- Columns
- Links
- Media kit
||| MENU - pcb007 Magazine
Thin PCBs for Smart Phones: Technology and Reliability Considerations
November 19, 2014 |Estimated reading time: 1 minute
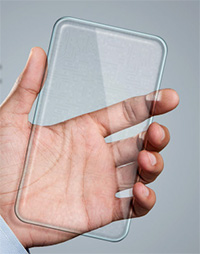
Abstract
The next generation of smartphones will demand very thin multilayer boards to reduce product thickness again. This paper shows three different manufacturing approaches which can be used for very thin, any-layer build-ups. The technological approaches are compared on reliability level—the any-layer copper filled microvia technology which is to be considered as state-of-the-art technology for high-end phones and the ALIVH-C/G technology that is well established in Japan.
A test vehicle design featuring test coupons for comprehensive reliability test series has been defined as target application for investigation. The applied test vehicle build-ups comprise an eight-layer build-up with total board thickness below 500 µm. The first test vehicle is based on an any-layer HDI build-up including copper filled stacked microvia structures, the second test vehicle features a 1+6+1 ALIVH-C build-up comprising an outer HDI prepreg layer, while the third test vehicle is built in ALIVH-G technology featuring a full ALIVH build-up.
The influence of the applied manufacturing technology on the reliability performance of thin PCBs is evaluated based on these three test vehicle build-ups.
To cover the behavior during SMD component assembly the produced samples are subjected to reflow sensitivity testing applying a lead-free reflow profile with a peak temperature of +260ºC. Failure occurrence and the observed failure modes are evaluated and compared.
In parallel, a temperature cycling test is conducted on the test vehicles in a temperature range between -40ºC and +125ºC to evaluate the thermo mechanical reliability of the test vehicles with regard to the manufacturing technology.
To characterize the reliability aspects influenced by electrochemical migration phenomenon the different samples are subjected to a HAST test at +130ºC with 85% humidity level.
The results obtained from reliability testing are summarized and compared within this paper. The identified relations between manufacturing technology and the reliability performance of the test vehicles are shown; strengths as well as weaknesses of the applied any-layer technologies are identified and summarized.
Read the full article here.
Editor's Note: This article originally appeared in the October issue of The PCB Magazine.
Suggested Items
Target Condition: Are Autorouters Friend or Foe?
07/01/2025 | Kelly Dack -- Column: Target ConditionFor PCB designers, just hearing the word “autorouters” can trigger everything from eye rolls to heated debate. We all have stories—some painful, some comical—of boards gone sideways at the hands of an overzealous routing algorithm. But these tools aren’t going away, and frankly, they shouldn’t. Used wisely, they can save some project teams hours or even days. Used blindly, they can cost weeks. So, where do autorouting tools stand today, and is interactive routing the smarter path forward?
High Density Packaging User Group (HDP) Welcomes Lincstech as New Member
07/01/2025 | High Density Packaging User GroupHigh Density Packaging User Group (HDP) is pleased to announce that Lincstech Co., Ltd. (Lincstech) has become a member.
Zhen Ding's 2025 Lean & Digital Initiative Presentation Conference Concludes Successfully, Driving Group Transformation
07/01/2025 | Zhen DingTo advance its digital transformation strategy and embody the CA- PDCA continuous improvement philosophy, Zhen Ding Technology Group (Zhen Ding) successfully hosted the 2025 H1 Lean & Digital Initiative Presentation Conference.
EU Defence Electronics Ecosystem Highlighted in Brussels
07/01/2025 | I-Connect007 Editorial TeamIn this interview, Alison James, senior director of Global Electronics Association—Europe (formerly IPC), discusses the European Defence & Security Summit in Brussels, June 9–13, as well as the first IPC–ASD Europe Defense Electronics Summit, June 10th, which brought together 70 leaders from across the electronics manufacturing supply chain. ASD is the Aerospace, Security and Defence Industries Association of Europe, and co-hosted both the larger and smaller events.
Smarter Machines Use AOI to Transform PCB Inspections
06/30/2025 | Marcy LaRont, PCB007 MagazineAs automated optical inspection (AOI) evolves from traditional end-of-process inspections to proactive, in-line solutions, the integration of AI and machine learning is revolutionizing defect reduction and enhancing yields, marking a pivotal shift in how quality is managed in manufacturing.