-
-
News
News Highlights
- Books
Featured Books
- pcb007 Magazine
Latest Issues
Current IssueThe Hole Truth: Via Integrity in an HDI World
From the drilled hole to registration across multiple sequential lamination cycles, to the quality of your copper plating, via reliability in an HDI world is becoming an ever-greater challenge. This month we look at “The Hole Truth,” from creating the “perfect” via to how you can assure via quality and reliability, the first time, every time.
In Pursuit of Perfection: Defect Reduction
For bare PCB board fabrication, defect reduction is a critical aspect of a company's bottom line profitability. In this issue, we examine how imaging, etching, and plating processes can provide information and insight into reducing defects and increasing yields.
Voices of the Industry
We take the pulse of the PCB industry by sharing insights from leading fabricators and suppliers in this month's issue. We've gathered their thoughts on the new U.S. administration, spending, the war in Ukraine, and their most pressing needs. It’s an eye-opening and enlightening look behind the curtain.
- Articles
- Columns
- Links
- Media kit
||| MENU - pcb007 Magazine
Estimated reading time: 1 minute
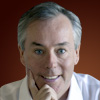
Why Removing Your Bottleneck is a Bad Idea
I received a number of comments about my column, Are Boringly Predictable Operations Possible? (February 2014). An argument repeated to me again and again was, “We don’t have a capacity problem! We have a sales problem! I have plenty of capacity!” To which I think, but do not say, “No you don’t, otherwise you wouldn’t have a sales problem.”
Let me give you an example. Let’s say you have one LDI machine for building your HDI product. This machine is only utilized 40% of the time. The orders coming off this machine generate 80% of your profits. You would tell me, “Gray, we do not have a capacity problem at LDI.” And I would likely be unable to convince you otherwise. Let’s say you have a number of orders going through your shop that are not only HDI, but HDI quick-turn premium orders. If you complete these orders on time you will have revenue and profitability numbers for the month that will be record breakers. Then the LDI machine suddenly goes down. You have zero throughput for a week as the machine is repaired. This lack of a second machine, this extra capacity, is going to have a negative impact on your current and future sales.
You could say that isn’t what you meant about not having a capacity problem--of course having only one machine for doing critical work is risky. Then why did you let the Lean expert strip you of all excess capacity to level load and balance the production line if you knew intuitively this would increase your risk? On a recent internet search, I found this: “Line balancing is leveling the workload across all processes in a cell or value stream to remove bottlenecks and excess capacity.” The article stated, “Match the production rate after all wastes have been removed to the takt time at each process of the value stream.”
This is a very popular, yet insane thing to do.
Read the full column here.
Editor's Note: This column originally appeared in the July 2014 issue of The PCB Magazine.
More Columns from Solving DAM Problems
Solving DAM Problems: Solving a True DAM ProblemSolving Dam Problems: Why Removing Your Bottleneck is a Bad Idea
Change Your DAM Thinking: Do We Need to be More Innovative?
Solving DAM Problems: Can Scrap be Beaten? A Strategy for 2014 and Beyond
Solving Dam Problems: How to Compute Your Plant's DAM Capacity
Solving DAM Problems: Standards are DAM Important!
Solving DAM Problems: What's the DAM Problem with Scheduling?
Solving Your DAM Problems: Examine Your DAM WIP