3D-printed Rocket Engine Aims to Break World Record
June 16, 2015 | UC San DiegoEstimated reading time: 2 minutes
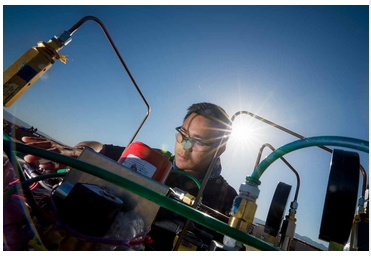
On a hot, dusty Friday evening in May, a caravan of five cars packed with UC San Diego students rolled onto FAR site in the Mojave Desert – a 10-acre property established by the Friends of Amateur Rocketry, Inc. to safely test and launch rockets. It took three tries, but the UC San Diego chapter of Students for the Exploration and Development of Space were able to successfully test the latest version of their 3D-printed rocket engine.
Shooting for the stars
Now that the engine is ready, the team will finish building the rocket it will power and take it to the Experimental Sounding Rocket Association's Intercollegiate Engineering Rocket Competition from June 25 to 27 in Green River, Utah.
“We’re going to break the world record for the longest flight of a 3D-printed rocket engine,” said Darren Charrier, SEDS business manager and first-year engineering student at UC San Diego. “We’re aiming for our rocket to fly 10,000 feet in the air. We all watched the first record being set a few weekends ago – the first 3D-printed rocket engine went 60 feet in the air.”
The first world record was established by Bagaveev Corporation, which subsequently donated $2,600 to the SEDS crowdfunding campaign.
The UC San Diego engine was sponsored by GPI Prototypes, a 3D printing company in Chicago, which subsequently printed the engine. SEDS is also sponsored by NASA’s Marshal Flight Space Center, which helped to finance the fabrication of the test stand. Behind NASA, SEDS UCSD has a whole host of sponsors such as Lockheed Martin, XCOR, The Gordon Center, Gantner Instruments, and many more.
The test
The students had been at FAR first in 2013 to test Tri-D, the team’s inaugural research project, and again a few months prior to test UC San Diego’s first 3D-printed rocket engine, Vulcan-I. The initial test of Vulcan-I (called a hotfire) lasted only 5 seconds.
Image
With the completion of the first test, UC San Diego became the first university to successfully design, print and test a 3D-printed rocket engine.
The students were present at FAR again in May to fire the engine for 15 seconds, which is the amount of time the engine will burn during the launch.
“The last stretch of the drive to FAR is the longest,” said Charrier. “The drive takes five hours, and even longer for those towing the test stand! The fact that so many students were willing to make the trip this close to finals week really shows how passionate they are.”
Image
The night they arrived, many of the students camped in tents while others slept under the stars. They were up at 6 a.m. Saturday morning to prepare the test stand and get ready for the hotfire.
“We weren’t ready to test the engine until 1 p.m. on Saturday,” said Charrier. “Once the engine was cleaned and calibrated, we needed an ignition source. The igniter itself is a small amount of solid rocket fuel at the end of a stick, and it catches fire when introduced to an electrical charge. Unfortunately, the first test failed because of operational errors.”
Refilling the tanks takes approximately 2.5 hours. The second time the team tried it, the igniter simply didn’t work. While searching for the problem, they discovered that the pressures in their test system were too high. The third time was the charm for Vulcan-I, and at 6 p.m. Saturday evening, the team successfully fired the engine.
The engine is about 10 inches long and weighs about 10 lbs. It is designed to generate 750 lbs of thrust and is made of a high-grade alloy.
Suggested Items
The Test Connection Inc. Appoints USM Reps as Exclusive Sales Representative in Mexico
05/13/2025 | The Test Connection Inc.The Test Connection Inc. (TTCI), a leading provider of electronic test and manufacturing solutions, is pleased to announce the appointment of USM Reps as its exclusive sales representative in Mexico.
Top 10 OSAT Companies of 2024 Revealed—China Players See Double-Digit Growth, Reshaping the Global Market Landscape
05/13/2025 | TrendForceTrendForce’s latest report on the semiconductor packaging and testing (OSAT) sector reveals that the global OSAT industry in 2024 faced dual challenges from accelerating technological advancements and ongoing industry consolidation.
Innovative Technology Advancements in Test: HATS² Technology and Its Impact on Reliability Testing
05/13/2025 | Barry Matties, I-Connect007Ensuring the reliability of printed circuit boards (PCBs) has become increasingly difficult and critical, yet the development of advanced testing methodologies is essential to meeting industry demands and addressing persistent challenges. One significant innovation is the High Acceleration Thermal Shock (HATS²) test system, which transforms how reliability testing is conducted. After 40 years in the testing business at Microtek, Bob Neves is beginning a new journey with his company, Reliability Assessment Solutions Inc. (RAS).
Discover TRI Test Solutions at New-Tech 2025
05/08/2025 | TRIBynet Testing Systems, TRI's industry partner, will join New-Tech 2025 at EXPO Tel-Aviv, Pavilion 1 from May 20 – 21, 2025.
Datest Expands Presence in the Upper Midwest with Omni-Tec Partnership
05/05/2025 | DatestDatest, a trusted leader in advanced testing, engineering, inspection, and failure analysis services, is proud to announce its partnership with Gary Krieg of Omni-Tec, Inc. as its official sales representative in the Upper Midwest.