-
- News
- Books
Featured Books
- smt007 Magazine
Latest Issues
Current IssueWhat's Your Sweet Spot?
Are you in a niche that’s growing or shrinking? Is it time to reassess and refocus? We spotlight companies thriving by redefining or reinforcing their niche. What are their insights?
Moving Forward With Confidence
In this issue, we focus on sales and quoting, workforce training, new IPC leadership in the U.S. and Canada, the effects of tariffs, CFX standards, and much more—all designed to provide perspective as you move through the cloud bank of today's shifting economic market.
Intelligent Test and Inspection
Are you ready to explore the cutting-edge advancements shaping the electronics manufacturing industry? The May 2025 issue of SMT007 Magazine is packed with insights, innovations, and expert perspectives that you won’t want to miss.
- Articles
- Columns
- Links
- Media kit
||| MENU - smt007 Magazine
A Review of the Opportunities and Processes for Printed Electronics (Part 3): Materials, Process Developments
June 24, 2015 | Happy Holden, PCB Technologist-RetiredEstimated reading time: 10 minutes
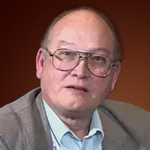
Most of the attention given to materials has appropriately centered on conductive inks, especially silver. Silver is the most conductive commonly used metal for making circuit conductors. Membrane switch circuits, which operate at relatively high voltages and low currents, have been printed onto polyester base materials using silver inks for more than a few decades. The challenge has been getting these circuits to have the bulk conductivity associated with copper. Common inks have conductivities that hover around 10% of copper and are not generally suitable for higher performance applications that operate at lower voltages or may require more power.
A number of suppliers have attacked the problem using a combination of new formulations of binders in the ink and nanoparticle silver are showing good improvements. One company, NovaCentrix, is addressing the challenge of making printable circuits by developing a tool and technology that sinters metal and semiconductor inks in a matter of milliseconds using light energy. The process reportedly can be carried out on a range of materials, including low-temperature, flexible substrates such as polyethylene terephthalate (PET) and paper. It is a promising technology for making low-cost products.
Ink technology
Organic and inorganic materials are both used for printed electronics. Ink materials must be available in liquid form for solution, dispersion or suspension. They must function as conductors, semiconductors, dielectrics or insulators. Material costs must be appropriate for the application.
For printing, viscosity, surface tension and solid content must be tightly controlled. Cross-layer interactions, such as wetting, adhesion, solubility and post-deposition drying procedures, affect the outcome. Additives often used in conventional printing inks are unavailable because they often defeat the purpose of electronic functionality.
Material properties largely determine the differences between printed and conventional electronics. Printable materials provide decisive advantages beside printability, such as mechanical flexibility and functional adjustment by chemical modification (e.g., light color in OLEDs).
Printed conductors offer lower conductivity and charge carrier mobility. With a few exceptions, inorganic ink materials are dispersions of metallic microparticles and nanoparticles. P-type metal-oxide-semiconductor (PMOS) technology may be used in printed electronics, but not complementary metal–oxide–semiconductor (CMOS) technology.
Conductive inks have been available for at least 40 years. The new conductive inks are designed specifically for use with low-temperature substrates including paper, (PET), polyether ether ketone (PEEK) and other plastics (including polyethylene film) and cure in an air environment.
Table 1: Ink Technologies
Copper, tin and silver nanoparticles are used with screen, flexo, offset and inkjet printing. Gold, silver and copper particles are used with inkjet. Sheet resistance is as low as ten milliohms per square. Resistivity’s as low as four times bulk have been attained with silver, but are higher for copper inks.
AC electroluminescent (EL) multicolor displays can cover many tens of square meters, or be incorporated into small watch faces and instrument displays. They involve six to eight printed inorganic layers, including a copper-doped phosphor, on a plastic film substrate.
Nanotechnology is the greatest boon to PE inks. There are proprietary material comprised of silicon nanoparticles dispersed in an environmentally-friendly blend of chemicals. These have optimized silicon particle size and dopant concentration to maximize the conversion efficiency of photovoltaic (PV) cells. The ink is screen-printed and a lower viscosity is available for inkjet printing.
Carbon nanotube (CNT) is another nanotechnology. CNT inks are available from many suppliers and known as V2V Ink Technology. C3Nano has transparent conductive CNT ink for touch panels and solar cells.
Table 2: Nanoparticle Conductive Metal Inks (from Novacentrix)
Substrates
Printed electronics uses flexible substrates, which lowers production cost and allows fabrication of mechanically flexible circuits. While inkjet and screen printing typically imprint rigid substrates like glass and silicon, mass printing methods nearly exclusively use flexible foil and paper. PET is a common choice due to its low cost and higher temperature stability. Polyethylene naphthalate (PEN) is another.
PEEK is a colorless organic polymer thermoplastic used in engineering applications. Polyimide (PI) foil is another alternative. Paper's low cost and manifold applications make it an attractive substrate, but its roughness and absorbency make it problematic for electronics. Low roughness and suitable wettability, which can be tuned pre-treatment (coating, corona) are important criteria for substrates. In contrast to conventional printing, high absorbency is usually disadvantageous.
Page 1 of 3
Suggested Items
Seeing a Future in Mexico
07/09/2025 | Michelle Te, I-Connect007The Global Electronics Association (formerly known as IPC) has been instrumental in fostering a partnership with Guanajuato, a state north of Mexico City with 12 industrial clusters and close to 150 companies involved in electronics. This past spring, Alejandro Hernández, the undersecretary for investment promotion in Guanajuato, attended IPC APEX EXPO 2025 at the invitation of IPC Mexico Director Lorena Villanueva, where he met with several companies to discuss the opportunities available in Mexico. He is inviting electronics-related companies seeking long-term investment in a centrally located area with access to highways, railways, and ports.
Webinar Review: A Global Trade and Economy in Flux
07/09/2025 | I-Connect007 Editorial TeamIn a July 8 webinar, Global Electronics Association Chief Economist Shawn DuBravac provided a comprehensive analysis of the evolving international trade environment, its implications for inflation, monetary policy, and labor dynamics, and a sober assessment of market valuations. In “Navigating a Shifting Landscape” DuBravac painted a picture of a global economy in flux, where shifting trade alliances and tariff structures are redrawing the supply chain map and influencing the broader economic landscape, while also conveying an overall bullish market outlook.
Arrow Electronics Launches Engineering Solutions Center to Support Tech Innovation Across India and Southeast Asia
07/09/2025 | Arrow ElectronicsArrow Electronics, a global provider of technology solutions, announced the launch of its new Engineering Solutions Center(ESC) in Bangalore, India.
LITEON Technology Reports Consolidated June Sales of NT$13.6 Billion, Up 16% Y-o-Y
07/08/2025 | LITEON TechnologyLITEON Technology reported its June consolidated revenue of NT$13.6 billion. Thanks to the growth from power management in cloud computing, advanced server, and networking, the revenue is up 2% M-o-M, 16% Y-o-Y. The cumulative sales for January to June totaled NT$76.8 billion, up 24%, Y-o-Y.
Niche Electronics Announces Major Manufacturing Upgrade
07/08/2025 | Niche ElectronicsNiche Electronics, a leading electronics manufacturing services company, announced today that it has completed installation of Yamaha’s newest SMT lineup at its Pennsylvania production facility.