-
- News
- Books
Featured Books
- smt007 Magazine
Latest Issues
Current IssueWhat's Your Sweet Spot?
Are you in a niche that’s growing or shrinking? Is it time to reassess and refocus? We spotlight companies thriving by redefining or reinforcing their niche. What are their insights?
Moving Forward With Confidence
In this issue, we focus on sales and quoting, workforce training, new IPC leadership in the U.S. and Canada, the effects of tariffs, CFX standards, and much more—all designed to provide perspective as you move through the cloud bank of today's shifting economic market.
Intelligent Test and Inspection
Are you ready to explore the cutting-edge advancements shaping the electronics manufacturing industry? The May 2025 issue of SMT007 Magazine is packed with insights, innovations, and expert perspectives that you won’t want to miss.
- Articles
- Columns
- Links
- Media kit
||| MENU - smt007 Magazine
Reducing Risks to Employees’ Health with Extraction and Filtration Technology
August 18, 2015 | Stefan Meissner, ULT AGEstimated reading time: 1 minute
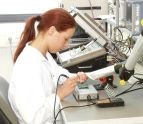
Occupational health and safety in manufacturing companies have become increasingly important in recent years. Today it should be seen as a part of the job rather than an annoyance. Manufacturing processes have gained in complexity, and resulting pollutants have become smaller and particularly more exotic.
"From chipping come chips" is a popular saying. Today, the chips cannot be seen with the naked eye any longer since particle size of resulting dust and smoke has arrived in the nano range.
Pollutants of any size always affect humans, machines and the environment. In addition to social and human aspects, a high sickness absence rate of employees has adverse economic effects on a company just like malfunctioning machines due to pollutions. Maintenance expenses, rework and finally loss of reputation and falling demand are the predominant adverse effects.
These factors lead to a rising demand for extraction and filtration technology, which reliably protects equipment and employee health, and furthermore, takes account of changing process parameters.
By now, extraction and filtration technology covers a wide range of airborne substances. Nearly all processes to be found in the manufacturing industry are supported. From interconnection and separation technologies, surface processing such as drilling, sintering and milling, the utilisation of fluxes or production processes such as 3D printing or rapid prototyping by means of laser, soldering and gluing — all these processes generate harmful substances that might show extreme impact on health.
Lasers are increasingly utilised in metal and plastics processing (e.g., drilling, welding, cutting, engraving, sintering, etc.). For example, in metal processing dusts containing heavy metals are released that may accumulate in the human body. During processing of alloyed metals, contained substances such as nickel, cobalt and chromium are released. The pyrolysis of organic substances may generate dioxins or hydrogen chloride. Moreover, laser smoke contains fine dust that may, at worst, lead to respiratory diseases, cardiovascular problems and an increased cancer risk.
Apart from bad quality of work due to permanent smoke and odour emissions, machines may be affected or damaged due to pollution and chemical reactions of their products. In particular, in the case of finest precision mechanical works, each kind of impact by particles must be avoided.
Editor's Note: This article originally appeared in the August 2015 issue of SMT Magazine.
Suggested Items
SHENMAO Strengthens Semiconductor Capabilities with Acquisition of PMTC
07/10/2025 | SHENMAOSHENMAO America, Inc. has announced the acquisition of Profound Material Technology Co., Ltd. (PMTC), a premier Taiwan-based manufacturer of high-performance solder balls for semiconductor packaging.
Hands-On Demos Now Available for Apollo Seiko’s EF and AF Selective Soldering Lines
06/30/2025 | Apollo SeikoApollo Seiko, a leading innovator in soldering technology, is excited to spotlight its expanded lineup of EF and AF Series Selective Soldering Systems, now available for live demonstrations in its newly dedicated demo room.
SolderKing’s Successful Approach to Modern Soldering Needs
06/18/2025 | Nolan Johnson, I-Connect007Chris Ward, co-founder of the family-owned SolderKing, discusses his company's rapid growth and recent recognition with the King’s Award for Enterprise. Chris shares how SolderKing has achieved these award-winning levels of service in such a short timeframe. Their secret? Being flexible in a changing market, technical prowess, and strong customer support.
E-tronix Announces Upcoming Webinar with ELMOTEC: Optimizing Soldering Quality and Efficiency with Robotic Automation
05/30/2025 | E-tronixE-tronix, a Stromberg Company, is excited to host an informative webinar presented by Raphael Luchs, CEO of ELMOTEC, titled "Optimize Soldering Quality and Efficiency with Robotic Automation," taking place on Wednesday, June 4, 2025 at 12:00 PM CDT.
SMTA Releases Final Batch of Training Resources Donated by Bob Willis
05/29/2025 | SMTAThe Surface Mount Technology Association (SMTA) announces the release of several more webinars, poster sets, and photo libraries to conclude a generous donation from renowned industry expert Bob Willis.