-
- News
- Books
Featured Books
- pcb007 Magazine
Latest Issues
Current IssueThe Hole Truth: Via Integrity in an HDI World
From the drilled hole to registration across multiple sequential lamination cycles, to the quality of your copper plating, via reliability in an HDI world is becoming an ever-greater challenge. This month we look at “The Hole Truth,” from creating the “perfect” via to how you can assure via quality and reliability, the first time, every time.
In Pursuit of Perfection: Defect Reduction
For bare PCB board fabrication, defect reduction is a critical aspect of a company's bottom line profitability. In this issue, we examine how imaging, etching, and plating processes can provide information and insight into reducing defects and increasing yields.
Voices of the Industry
We take the pulse of the PCB industry by sharing insights from leading fabricators and suppliers in this month's issue. We've gathered their thoughts on the new U.S. administration, spending, the war in Ukraine, and their most pressing needs. It’s an eye-opening and enlightening look behind the curtain.
- Articles
- Columns
- Links
- Media kit
||| MENU - pcb007 Magazine
Estimated reading time: 3 minutes
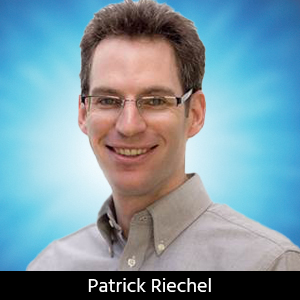
Stepping Up To Laser Processing for Flex, Part 1: Opportunities and Implications
This six-part series will examine how to effectively supplement your flex production capabilities with laser processing.
Market demand for smaller, faster, wearable, lighter and more powerful devices continues to keep PCB manufacturers scrambling to keep up as they evolve and adapt their manufacturing capabilities to meet changing customer needs. But keeping up with the dizzying pace of change in the world of PCB manufacturing need not be a daunting task. Employing laser technology is one of the best ways to stay current, as it enables printed circuit manufacturers to achieve manufacturing flexibility and agility, with more accurate and/or smaller features than is possible with traditional processes.
As highlighted in Figure 1, there are several steps in the flexible circuit manufacturing process where laser processing can play a significant role. In this series, we will focus on the laser micromachining processes related to drilling, coverlay cutting and circuit singulation using general laser micromachining systems. Keep in mind that, although this series deals primarily with flex, many of same laser processing principles discussed also apply to rigid boards—and even to LDI.
Figure 1: The role of laser technology in the flex processing manufacturing flow.
When is the Right Time to Adopt Laser Micromachining?
Printed circuit manufacturers typically invest in laser micromachining systems when current mechanical processing capabilities can no longer address the processing accuracy and quality dictated by size constraints and newer materials. Mechanical punching, routing, and drilling are either no longer feasible or simply not a cost-effective solution due to many of the following issues:
- Features become too small or too complex for drill/routing bit diameters and/or die punch manufacturing capabilities
- Trace width/spacing requirements require via pads to shrink beyond mechanical drilling registration capabilities
- Part tolerances require machining accuracies beyond mechanical processing capabilities
- The number of vias per panel increases sufficiently to make mechanical drilling less cost effective than laser drilling.
- Customer demand includes blind via processing in thin flex material beyond the depth control capabilities of mechanical drills.
- High product mix and/or fast turnaround time requirements become incompatible with the long lead times and expense associated with fabricating dies for coverlay cutting and circuit singulation
If some of these issues sound familiar, it’s probably time to consider laser processing. But before launching into that endeavor, take the time to learn about the opportunities and implications associated with laser processing. It can pay big dividends, but to get optimal results there are some approaches and best practices that you should be aware of.
About This Series
In each future installment of the Stepping up to Laser Processing for Flex series, we will arm you with information you need to investigate the advantages of FPC laser processing and the role it can play in optimizing your processing capabilities. Upcoming installments will cover the following:
- Calculating and Optimizing Production
How do you calculate and optimize total system cost of ownership and cost per panel? We will provide an overview of the high-impact profitability factors in choosing and running your system.
- Readiness and Site Preparation
How do you ensure that your facilities are ready for the introduction of laser processing? Find strategies for addressing shop floor concerns such as HVAC, temperature control, debris removal capabilities, power requirements and more.
- Installation, Training, and Initial Operation
How do you get your new system installed and processing those first runs? We will cover installation best practices, system verification testing, training and safety.
- Process Development
How do you develop your process library? Learn several best practices, tips and tricks for typical flexible circuit laser processes.
- Maintenance and Servicing
How do you minimize system maintenance and repair costs while prolonging its useful life? We’ll examine best practices and considerations related to the “care and feeding” of your laser processing machine.
Mike Jennings is director of product marketing with ESI’s Industrial Products Division.
Patrick Riechel is product manager for ESI’s flexible circuit micromachining tools.
More Columns from Laser Pointers
Laser Pointers: Stepping Up to Laser Processing for Flex, Part 6 — Proper Care and Feeding of Your EquipmentLaser Pointers: Stepping Up to Laser Processing for Flex, Part 5—Process Development
Laser Pointers: Stepping Up to Laser Processing for Flex, Part 4—Installation, Training and Initial Operation
Laser Processing and Telecentricity
Stepping up to Laser Processing for Flex, Part 3: Readiness and Site Preparation
Automate to Innovate in Flex Processing
Stepping Up to Laser Processing for Flex, Part 2: Calculating and Optimizing Production
Keeping on Top of Laser Safety