-
- News
- Books
Featured Books
- pcb007 Magazine
Latest Issues
Current IssueVoices of the Industry
We take the pulse of the PCB industry by sharing insights from leading fabricators and suppliers in this month's issue. We've gathered their thoughts on the new U.S. administration, spending, the war in Ukraine, and their most pressing needs. It’s an eye-opening and enlightening look behind the curtain.
The Essential Guide to Surface Finishes
We go back to basics this month with a recount of a little history, and look forward to addressing the many challenges that high density, high frequency, adhesion, SI, and corrosion concerns for harsh environments bring to the fore. We compare and contrast surface finishes by type and application, take a hard look at the many iterations of gold plating, and address palladium as a surface finish.
It's Show Time!
In this month’s issue of PCB007 Magazine we reimagine the possibilities featuring stories all about IPC APEX EXPO 2025—covering what to look forward to, and what you don’t want to miss.
- Articles
- Columns
Search Console
- Links
- Media kit
||| MENU - pcb007 Magazine
An Interview with Gene Weiner at HKPCA
January 19, 2016 | Barry Matties and Stephen Las Marias, I-Connect007Estimated reading time: 17 minutes
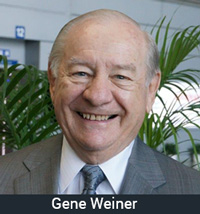
Barry Matties and Stephen Las Marias recently met with industry veteran Gene Weiner, president of Weiner International Associates to get his take on the HKPCA show, industry trends and his outlook for 2016.
Barry Matties: Gene, when did you get started in this industry?
Gene Weiner: I started in 1956 as a student technician at MIT’s Lincoln Laboratory, and that's where I had my first publication at age 20, co-authored with E.A. Guditz, “Plated Electrical Connections.” We made cordwood packages with electroplated connections. No solder was used. The concept was like that which Joe Fjelstad envisions—a package without solder joints. First, we encapsulated all the components of the package in parallel with silicone then epoxy, bringing all leads to either the “top” or “bottom” surface, and then milled out the circuit patterns exposing the tips of the component leads. We then electroplated the top and bottom sides of the “box”, and sanded it flat, exposing a flat plastic (insulating) surface with embedded copper circuitry. We successfully cycled and tested the package, and it was a really a great innovation. But before that got off the ground along came the semiconductor, multilayer printed circuits, advanced packaging, and plated through-holes. Everything changed overnight and the cordwood package with plated electrical connections was shelved.
Matties: But the concept is still valid.
Weiner: It is. When Joe Fjelstad brought up the solderless connection packaging and we all played with it a few years ago, I found a copy of my original paper. I sent a copy to him, and we enjoyed reviewing it. Joe’s concept was something we couldn't do back then because suitable components and materials weren't available, so his was a more advanced version.
Matties: So you’ve been in the industry for how many years now?
Weiner: Almost 60 years.
Matties: What's the greatest surprise you've seen in the 60 years?
Weiner: The greatest surprise, and it really wasn't a surprise, was the rise and fall of the printed circuit industry as we knew it in the United States, from virtually the beginning to the end.
Matties: Are you referring to the late ‘90s, when we saw the steep fall?
Weiner: The late ‘90s and then again in 2009, which really just about finished it off. It was driven by the big OEMs, like Motorola, Burroughs, and companies like that. They kept squeezing and squeezing the price and put a number of companies in the Midwest and Northeast out of business. Some of them failed themselves while others shifted their sourcing to Asia. The trend continued as EMS companies arose and squeezed prices further, treating boards as just a component or commodity as they, too, began to source in Asia. Japan first, then Taiwan put a major emphasis on quality and volume production. This trend continued to China where labor was, at that time, much lower than the more “industrialized” countries.
Matties: So now we're here at the HKPCA show, which is the largest PCB trade show in the world, I think.
Weiner: That's their claim to fame and from the looks of it I’d say it is. When I go to the CPCA in March we’ll find out, but I think it is because it's more focused on printed circuits and everything related to it—they’re not limiting it to just the PCB, which is a very smart move, and it’s working very well.
Matties: What's so impressive about this show is the total pieces of equipment that you see on the floor. If you want to come kick the tires, this is a place to do it.
Weiner: Pieces of equipment are being introduced here that will not be introduced or even shown at the IPC APEX event in Las Vegas in March.
Matties: And there’s no need, right? This equipment is really geared for mass production, and IPC isn’t really servicing that sort of market at the shows in the U.S.
Weiner: I fault a lot of the U.S.’s fall on the drive by the major OEMs to cut costs. I fault our government for some of this, for driving up the cost of doing business in the United States and driving companies to manufacture offshore. I fault some of this on perhaps too much of an individual approach from the entrepreneurs, the smaller operations in the U.S., who back then could not afford to keep up, as you needed higher and higher volume to justify cost and newer facilities and equipment to produce finer feature sizes. It's a very complicated situation. Even now, people talk about reshoring and new activities or whatever, but I've just got a letter from a colleague on the West Coast who's been in this industry as long as I have, and he's a bit older than I am...
Matties: Really? Is that possible? [laughing]
Weiner: It is! I'm not going to be 80 for another nine months or so, and he's got a decade plus on me. But I asked him what he’s been doing and he said he’s busy destroying his records on soldering and bare boards because it is a thing of the past. He has moved on to packaging and ICs and he believes anyone still in the U.S. that hasn't done that had better do so soon because they won't be here at all in the near future.
We also had a visitor here at the show this week from Massachusetts because he has to upgrade and go to digital in imaging, add laser drills, and a change and expand a number of other operations. He told me that the equipment he has to see at the prices he wants just won't be shown in the United States in March. He’s a former director of IPC, so we showed him some new things including one piece of equipment that was being introduced here at the show. It was developed in North America, but it’s being introduced in China. At first I asked myself why that was, but when you look at reality and leave out the talk about the Feds, the government, or reshoring, it becomes obvious—the United States produces about 5% of the world’s bare boards while Greater China manufactures more than 70%. If you are an equipment company and it costs money to build the equipment, ship it, get it through customs, set it up, test it and show it, and the dates of two major shows were identical would you put it in the 5% show or the show in the 70+% market? It’s just common business sense.
Page 1 of 3
Suggested Items
Indium’s Karthik Vijay to Present on Dual Alloy Solder Paste Systems at SMTA’s Electronics in Harsh Environments Conference
05/06/2025 | Indium CorporationIndium Corporation Technical Manager, Europe, Africa, and the Middle East Karthik Vijay will deliver a technical presentation on dual alloy solder paste systems at SMTA’s Electronics in Harsh Environments Conference, May 20-22 in Amsterdam, Netherlands.
SolderKing Achieves the Prestigious King’s Award for Enterprise in International Trade
05/06/2025 | SolderKingSolderKing Assembly Materials Ltd, a leading British manufacturer of high-performance soldering materials and consumables, has been honoured with a King’s Award for Enterprise, one of the UK’s most respected business honours.
Knocking Down the Bone Pile: Gold Mitigation for Class 2 Electronics
05/07/2025 | Nash Bell -- Column: Knocking Down the Bone PileIn electronic assemblies, the integrity of connections between components is paramount for ensuring reliability and performance. Gold embrittlement and dissolution are two critical phenomena that can compromise this integrity. Gold embrittlement occurs when gold diffuses into solder joints or alloys, resulting in mechanical brittleness and an increased susceptibility to cracking. Conversely, gold dissolution involves the melting away of gold into solder or metal matrices, potentially altering the electrical and mechanical properties of the joint.
'Chill Out' with TopLine’s President Martin Hart to Discuss Cold Electronics at SPWG 2025
05/02/2025 | TopLineBraided Solder Columns can withstand the rigors of deep space cold and cryogenic environments, and represent a robust new solution to challenges facing next generation large packages in electronics assembly.
BEST Inc. Reports Record Demand for EZReball BGA Reballing Process
05/01/2025 | BEST Inc.BEST Inc., a leader in electronic component services, is pleased to announce they are experiencing record demand for their EZReball™ BGA reballing process which greatly simplifies the reballing of ball grid array (BGA) and chip scale package (CSP) devices.