-
- News
- Books
Featured Books
- pcb007 Magazine
Latest Issues
Current IssueThe Hole Truth: Via Integrity in an HDI World
From the drilled hole to registration across multiple sequential lamination cycles, to the quality of your copper plating, via reliability in an HDI world is becoming an ever-greater challenge. This month we look at “The Hole Truth,” from creating the “perfect” via to how you can assure via quality and reliability, the first time, every time.
In Pursuit of Perfection: Defect Reduction
For bare PCB board fabrication, defect reduction is a critical aspect of a company's bottom line profitability. In this issue, we examine how imaging, etching, and plating processes can provide information and insight into reducing defects and increasing yields.
Voices of the Industry
We take the pulse of the PCB industry by sharing insights from leading fabricators and suppliers in this month's issue. We've gathered their thoughts on the new U.S. administration, spending, the war in Ukraine, and their most pressing needs. It’s an eye-opening and enlightening look behind the curtain.
- Articles
- Columns
- Links
- Media kit
||| MENU - pcb007 Magazine
Orbotech’s Gaby Waisman: 'The Future is Digital'
April 18, 2016 | Pete Starkey, I-Connect007Estimated reading time: 12 minutes
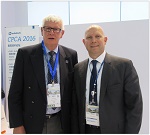
I sat down with Orbotech President Gaby Waisman at CPCA in Shanghai recently, and he offered a comprehensive explanation of why digitalization is truly the future, especially with regard to increasing throughputs. We also discussed Orbotech’s company vision and products, as well as its role in “helping to drive the industry into fully digitalized imaging technology.”
Starkey: Gaby, could you begin by giving me some idea of Orbotech’s company vision? How do you see the industry and its requirements for the future?
Waisman: Absolutely. So what we see today in the industry are several major trends that we need to address. One is obviously cost reduction or having better cost per print. The other one is yield enhancement, which is in a way is associated but has much more to it. The third is automation. The fourth is being greener, saving energy, catering for waste treatment and becoming greener in general, which is obviously not only one of the regulatory requirements, but in general this is what the industry is trying to strive for. What we're doing in addition is trying to add a layer of additional value and insight into the production floor team, giving them and management an ability to analyze the situation in each and every moment by aggregating information from the tools, as well as providing a business intelligence layer. We want to offer not only this kind of insight but also pre-emptive maintenance in order again to improve the uptime and overall yield of production efficiency.
Starkey: If we begin with your assessments of the market requirements, what information do you need to feed to your development people and your design people? What do you need to be producing to satisfy that market requirement?
Waisman: We need to offer digitalization. Digitalizing the production floor, we need to cater for thinner materials, tighter line-space. We need to do it faster and we need to do it more efficiently. We need to find ways to also increase the yield. And I will discuss it specifically with one of our machines. If we take a look at the booth over here, the first machine that is catering to such requirements is the Sprint, which is basically an inkjet. Its purpose is simply to digitalize the world of silk-screen, converting it from analog to digital.
Now this vision is not new. This is not the first time for us to present the inkjet machine. I believe we've been doing it for the last ten years, approximately. But we've moved gradually from offering solutions to quick turnaround, mid-production levels. For the first time now we can offer a solution for mass production. We are looking at the markets over here, Asia Pacific and definitely in China. The need is for mass production. We can offer a machine that offers similar, obviously better, cost performance, and cost per print, compared to the analog, silk screen solution. And in addition, it addresses the waste, saving steps along the process, saving on operators, saving on other factors related to the abilities of silk screen in general. And it offers better registration, alignment and so forth, and obviously automation. We can really offer, for the first time, a solution that can overhaul this industry, the mass-market, mass production industry, with this machine. This machine will be fully automated, offering up to 95 prints per hour. It offers superior quality, registration and all those aspects that not only can replace traditional silk screens but make it more efficient, save on the ink and material, make this a greener type of solution to something that is considered a base line production in the industry, and as I mentioned, in an automated way.
Starkey: I think you've made a very significant statement in saying that you now have developed inkjet printing to the level where you are confident to place it in a mass production environment. Always the association of inkjet is that it is a great technique for quick turn, small batch. In the past that's never really been suitable for the sort of volumes and the sort of throughputs you've been talking about.
Waisman: Very true. For the first time we've really managed this breakthrough from, as you mentioned, the small batch, quick turnaround, to mass production. It has been an evolutionary way, but it is a revolutionary step. This is the Sprint 200 that we're showcasing here, and I'm very confident that we are now seeing the beginning of the revolution, the era of turning analog into digital in this specific production phase.
Starkey: You have approached digital from two separate directions. You have for many years been identified as the leader in laser direct imaging for primary imaging. Now at the other end of PCB manufacturing sequence, you've brought a different digital imaging technology into play that can handle the sort of volumes and, as you say, you're helping to drive the industry into a fully digital, fully digitalized imaging technology.
Waisman: You're absolutely right, this is an additional step in the digital revolution that started about 10–15 years ago. It’s obviously apparent in each and every one of our tools. We haven't discussed the general advantages of digital versus analog—I think this is quite clear by now, with the flexibility and the other capabilities. But I think that specifically in silk screen this very important also because of the green trends and the need to have greener technologies that are digital, cost efficient, etc., and reduce the material waste. I think this is all very important in transforming this particular part of the industry.
Page 1 of 3
Suggested Items
SHENMAO Strengthens Semiconductor Capabilities with Acquisition of PMTC
07/10/2025 | SHENMAOSHENMAO America, Inc. has announced the acquisition of Profound Material Technology Co., Ltd. (PMTC), a premier Taiwan-based manufacturer of high-performance solder balls for semiconductor packaging.
KYZEN to Highlight Understencil and PCB Cleaners at SMTA Querétaro Expo and Tech Forum
07/09/2025 | KYZEN'KYZEN, the global leader in innovative environmentally responsible cleaning chemistries, will exhibit at the SMTA Querétaro Expo & Tech Forum, scheduled to take place Thursday, July 24, at Centro de Congresos y Teatro Metropolitano de Querétaro.
Driving Innovation: Direct Imaging vs. Conventional Exposure
07/01/2025 | Simon Khesin -- Column: Driving InnovationMy first camera used Kodak film. I even experimented with developing photos in the bathroom, though I usually dropped the film off at a Kodak center and received the prints two weeks later, only to discover that some images were out of focus or poorly framed. Today, every smartphone contains a high-quality camera capable of producing stunning images instantly.
Hands-On Demos Now Available for Apollo Seiko’s EF and AF Selective Soldering Lines
06/30/2025 | Apollo SeikoApollo Seiko, a leading innovator in soldering technology, is excited to spotlight its expanded lineup of EF and AF Series Selective Soldering Systems, now available for live demonstrations in its newly dedicated demo room.
Indium Corporation Expert to Present on Automotive and Industrial Solder Bonding Solutions at Global Electronics Association Workshop
06/26/2025 | IndiumIndium Corporation Principal Engineer, Advanced Materials, Andy Mackie, Ph.D., MSc, will deliver a technical presentation on innovative solder bonding solutions for automotive and industrial applications at the Global Electronics A