-
- News
- Books
Featured Books
- pcb007 Magazine
Latest Issues
Current IssueSales: From Pitch to PO
From the first cold call to finally receiving that first purchase order, the July PCB007 Magazine breaks down some critical parts of the sales stack. To up your sales game, read on!
The Hole Truth: Via Integrity in an HDI World
From the drilled hole to registration across multiple sequential lamination cycles, to the quality of your copper plating, via reliability in an HDI world is becoming an ever-greater challenge. This month we look at “The Hole Truth,” from creating the “perfect” via to how you can assure via quality and reliability, the first time, every time.
In Pursuit of Perfection: Defect Reduction
For bare PCB board fabrication, defect reduction is a critical aspect of a company's bottom line profitability. In this issue, we examine how imaging, etching, and plating processes can provide information and insight into reducing defects and increasing yields.
- Articles
- Columns
- Links
- Media kit
||| MENU - pcb007 Magazine
Nano System, Two Years On
April 22, 2016 | Stephen Las Marias, I-Connect007Estimated reading time: 10 minutes
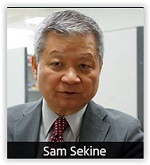
Established in July 2014, Nano System Inc. focuses on the design and manufacture of laser drill systems for the PCB industry. The company is also the exclusive distributor for Tongtai Machine and Tool Co. for PCB systems in the United States and Canada.
I caught up with Nano System President Sam Sekine last month at IPC APEX EXPO to discuss the latest product and business developments at his company.
Stephen Las Marias: Sam, thank you very much for this interview opportunity. Please talk about Nano System, and how the first two years have been.
Sam Sekine: The last time I had an interview with I-Connect007 was when we first received the order from Nova Drilling, but we couldn't make the machine just yet. We delivered the machine in December of last year. After we started our company, it took almost a year and a half for the first machine delivery. We designed it, we did our design manufacturing and then assembly, before shipping the machine. Everything is done back in New Hampshire.
That was the first machine. From that time on, Nova has been utilizing the machine very well. They recently showed the machine to a potential customer for us. I cannot tell you the name of the company, but that customer already placed an order for our second machine, and we are shipping the machine directly to them.
If we were doing just the distribution of the Tongtai machines, then I wouldn’t necessarily need much funding available. For our machines, we have to purchase the parts, assemble it, and all those costs are up to us. When we make one machine, it’s sales price is $600,000; the two machines are about $1.2 million. We need to have certain funding available for production of our systems for quick delivery. Luckily, we have good support from our investor, so we are making it. That's one way we are doing business, through R&D, design, and manufacturing the laser machine.
The other way is with the Tongtai machine sales. This has been working very well. Last year, we sold many machines to a company in Cupertino, which used to be a Hitachi customer. Companies check the capability of the Tongtai machine and the depth control is very accurate, so they want to utilize the Tongtai machine instead of continuing to buy the Hitachi machines. The price is slightly lower, but the most important thing is the overall quality, which is really good. That was one of the big sources of income for our company as a startup. We’re not quite even yet in the two years—we are on track with our goals for FY2016.
That's our good news. We’ve grown from that and now we're planning to focus more on the UV/CO2 laser machines. A lot of people are interested and are asking if we can make it at a smaller size and not for $600,000, but instead in the $200,000 range. The customers have been working together with us on this, and we have been working together with Tongtai. Our company is putting everything together, but we can purchase portions from Tongtai. They make about 100 of those machines every month, so we can purchase those parts and it will be less expensive. Then we can just mount the laser and do the optics by ourselves, and make a whole set of machines for lesser cost. Instead of us making everything in the U.S., we purchase that and 80% is already made, and then we can just add the 20% and make whole machines. That's the idea and it's working very well.
A lot of people are willing to work with us, and Tongtai is very happy with the way we work along with them. They asked us if we were interested in taking care of the Japanese market. I’ve been away from Japan since 1979, so after 35 years, I don't know much about it. But they asked if I could check into it. I’ve been talking to people I know, and they are willing to work together—so we may start selling Tongtai in Japan, too.
That's what we have been doing on the other side; but the main thing is making those UV/CO2 machines that we have right now and improving them. The next step is introducing a machine at a much lower cost, in the $200,000 range, for the people who really want it.
Las Marias: When you first envisioned setting up Nano System, what made you choose laser as the primary component in your drilling system?
Sekine: If our department, which used to be Hitachi Via, had not been purchased by another company, I would have stayed with Hitachi because I like the way they did business. But the new owner, kind of an investment company, had the idea that they needed to sell the company within two or three years.
For them, seeing me is crazy. I was looking at five to ten years from then at how to make the company stronger. That's a major reason I could not work with them anymore. It’s no longer Hitachi. Fortunately, at that time, the funding was available from our investor to make this machine. It's not a small amount, but they are happy to just support us, so we established the company. At the same time, we got a lot of requests from those Hitachi customers to make the UV/CO2 laser combo. There was a lot of demand because there was a very limited number of companies that could supply those machines in the United States, and they felt uncomfortable with the support of Hitachi under the new ownership. They don't have the same service as before. They asked me, ‘Sam, can you just take over that and make the UV/CO2 for us?’ That's how we started up.
We didn't think it was necessary to get into mechanical drills because there were already a lot of nice drilling machines available in the market. But they were short of a good UV/CO2 combo. I knew it was not going to be 200–300 machines, but there were definitely people in need of that technology. I said, ‘Okay. Let's work on that.’ Then our investor also agreed with our plan to make those machines. It costs a lot of money and takes a lot of time.
Luckily, we had great support from our first customer, Nova Drilling, who said, ‘Hey Sam. I know you’ve never sold any machines. I'll buy the first machine. I'll pay you a down payment. Let's work together.’ I was very lucky. We made the first machine for Nova, and since then we have been improving it.
Page 1 of 2
Suggested Items
TRI to Exhibit at SMTA Queretaro Expo 2025
07/16/2025 | TRITest Research, Inc. (TRI), the leading provider of test and inspection systems for the electronics manufacturing industry, is pleased to announce plans to exhibit at the SMTA Querétaro Expo 2025, scheduled to take place on July 24, 2025, at the Querétaro Centro de Congresos y Teatro Metropolitano.
Global PCB Connections: Let the Spec Fit the Board, Not Just the Brand
07/17/2025 | Jerome Larez -- Column: Global PCB ConnectionsIf you’ve ever seen an excellent PCB quote delayed, or worse, go cold because of a single line on the fab print, you’re not alone. Often, that line reads something like, “Use 370HR only,” or “IT-180A required.” These and other brand-name materials are proven performers, but unless your design needs that specific resin system (say, for RF performance, thermal reliability, or stringent CAF resistance), you may inadvertently be holding your job hostage.
IPC Hall of Fame Spotlight Series: Highlighting Lionel Fullwood
07/15/2025 | Dan Feinberg, I-Connect007Many IPC members who have contributed significantly to IPC and our industry have been awarded the IPC Raymond E. Pritchard Hall of Fame (HOF) Award. Though many early HOF members have passed away and are unknown to today’s IPC membership, their contributions still resonate. This special series on IPC Hall of Fame members provides a reminder of who was honored and why. As a bonus, for those who are still around, we get to find out what these talented individuals are up to today.
TRI Unveils New Platform for Diverse Board Sizes
07/14/2025 | TRITest Research, Inc. (TRI), the leading test and inspection systems provider for the electronics manufacturing industry, proudly introduces a new size configuration for SPI and AOI Models.
Seeing a Future in Mexico
07/09/2025 | Michelle Te, I-Connect007The Global Electronics Association (formerly known as IPC) has been instrumental in fostering a partnership with Guanajuato, a state north of Mexico City with 12 industrial clusters and close to 150 companies involved in electronics. This past spring, Alejandro Hernández, the undersecretary for investment promotion in Guanajuato, attended IPC APEX EXPO 2025 at the invitation of IPC Mexico Director Lorena Villanueva, where he met with several companies to discuss the opportunities available in Mexico. He is inviting electronics-related companies seeking long-term investment in a centrally located area with access to highways, railways, and ports.