-
-
News
News Highlights
- Books
Featured Books
- pcb007 Magazine
Latest Issues
Current IssueThe Hole Truth: Via Integrity in an HDI World
From the drilled hole to registration across multiple sequential lamination cycles, to the quality of your copper plating, via reliability in an HDI world is becoming an ever-greater challenge. This month we look at “The Hole Truth,” from creating the “perfect” via to how you can assure via quality and reliability, the first time, every time.
In Pursuit of Perfection: Defect Reduction
For bare PCB board fabrication, defect reduction is a critical aspect of a company's bottom line profitability. In this issue, we examine how imaging, etching, and plating processes can provide information and insight into reducing defects and increasing yields.
Voices of the Industry
We take the pulse of the PCB industry by sharing insights from leading fabricators and suppliers in this month's issue. We've gathered their thoughts on the new U.S. administration, spending, the war in Ukraine, and their most pressing needs. It’s an eye-opening and enlightening look behind the curtain.
- Articles
- Columns
- Links
- Media kit
||| MENU - pcb007 Magazine
Koen Hollevoet Explains Rogers' New PEEK-based Material for Extreme Temps
April 28, 2016 | Barry Matties, I-Connect007Estimated reading time: 9 minutes
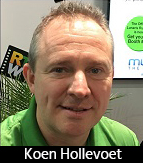
Rogers has been developing a new material called XT/duroid laminate, which is based on polyether ether ketone (PEEK) material and can withstand some of the harshest temperatures and environments. I met with Koen Hollevoet, Business Development Manager at Rogers Corporation, at IPC APEX EXPO 2016 to further discuss this material and learn how it might benefit the PCB market.
Barry Matties: Koen, let’s talk first about what you're introducing and what you've been presenting here at IPC APEX EXPO.
Koen Hollevoet: At Rogers, we're introducing XT/duroid laminates which are based on PEEK material. PEEK is a high temperature thermoplastic material that’s already well-known in the avionics industry and in oil and gas, because it's a material that is very chemical resistant and is also resistant to extremely hot temperatures or cold temperatures.
Rogers is using this PEEK-based material for PCBs. It works as an insulator with very interesting characteristics from a circuit perspective in terms of dielectric breakdown, thermal behavior, and things like that. As it is already known in the avionics industry and oil and gas, we think there's a very interesting market out there where we can introduce this as a circuit or maybe as a shielding material if it is covered not with copper but with aluminum or nickel, which we can do.
It really is multipurpose, and it takes us really out of our wheelhouse and into a new area that we have to learn about.
Matties: Why did you go into this area with this composite? Is this something that you just said, “Boy, this is an explosive market,” or what was the impetus behind it?
Hollevoet: Actually, what drove us into this was working in high-frequency and seeing materials getting thinner and thinner. With the PEEK material we were working very closely with a supplier that was making films and we said, “Wait a minute, if they can make films that are 1 mil or 2 mil thick, we can make thin RF circuits out of it.” In the beginning it didn't really fit high frequency applications, but today we've learned more about the impact of the copper, the impact of delamination and now we can make it into a high frequency laminate that is very stable over temperature. It has the lowest TCDk of Rogers’ product range.
By the time we went through this, we had many other people asking, “Can you stick nickel to it? Can you stick aluminum to it?” We tried more and more things and then we realized that there's a far bigger market beyond the high-frequency applications because people are hitting the limits with their current PTFE and polyimide materials and want to use PEEK because of the chemical resistance, low moisture absorption and thermal conductivity. We know this works for mechanical parts so let’s use it in circuits for avionics or automotive and some of these things.
So we discovered that there are whole new markets out there, which was not our original intention.
Matties: Sometimes that's how the best things happen, right?
Hollevoet: It’s interesting also because my background within Rogers for the first five years was originally in the power electronics market, and there temperature is much more of an issue with getting more power in smaller things like in electrical cars. So I have a background which is quite different from most of my high frequency colleagues in PCB laminates. That allows me today to combine different product technology knowledge and different market knowledge within the company.
Matties: So how fast do you think this technology will be embraced and creating great revenue streams for you? That's the million, or multi-million dollar question.
Hollevoet: My bosses always say, “Where's the money? Show me the money.” This is quite a new material, especially in the circuits world, so it takes time for people to do qualifications before adopting. That takes some time to do, especially in this market. It's all about reliability, and reliability is not something you do with overnight testing—you need 1,000 hours here, you need 500 hours there, etc. The next step is to design it in and to qualify the application. We expect it might take a few years from now until it turns into really big volume.
In the meantime, there are a lot of interesting opportunities we're working on, most of which are on the avionics side at this stage. We got involved with the Clean Sky Project, a research program funded by the European Community where they were asking for an alternative, new system, to replace the PTFE cable harnesses in the engines of airplanes. These cables are expensive and they are heavy because everything has to be shielded in there. So there's a lot of weight to save, especially in the future when the newer engines will have more sensors which means more wiring and more electronics in the engine. The new fuels will also push the temperatures up.
We teamed up with Trackwise and SEA (Systems Engineering and Assessment Ltd) from the UK and developed a multi-layer large flexible printed circuit to replace the PTFE wire harness. That really pushed the limits because up until then we said, “Oh yeah, we can do 200°C,” but actually the engineers from Rolls Royce that were behind this project wanted to push it to the max. We passed more than 3600 hours at 260°C without any failure, including 16 hours vibrations in 2 axis. We succeeded also more than 1500 hours at 330°C, but that was only after we introduced an additional oxidation barrier layer. The constructions stayed very stable with no delamination. That gave us enough confidence to proceed with people like Rolls Royce to pursue more commercial applications. We are pushing the boundaries thanks to these calls for development and R&D.
Matties: Are there standards around this yet?
Hollevoet: We consider that these materials on one hand are being used as a flexible material, so we should get into the flexible side. On the other hand, we can use it as a rigid material when it's thicker and contains more layers of glass reinforcement. It is a material with dual use in terms of flex or rigid or a combination.
Today the IPC and other regulators have their standards based on today's electronics, and we are pushing those limits so we can't fit everything into the standards that exist today. Today there is nothing foreseen for PEEK-based materials, so we have to create and set some new standards. Luckily, often innovators are less reluctant to depend only on the standard specifications.
Matties: Is there any special manufacturing from the manufacturer’s point of view when they're using it that they have to be aware of or invest into?
Hollevoet: Basically people that are already using materials in high-end circuit boards, such as processing PTFE multilayer boards should be able to handle this XT/duroid circuit laminate. Of course, it's chemical resistant so it will not react to many of the chemicals and you'll need plasma treatment or laser drilling and things like that because that's going to be more effective than any of the chemical processes.
Matties: So there are no barriers to entry for adopting this technology?
Hollevoet: No, I don't think so. It can be done, and it is being done in a number of shops we are working with today.
Matties: How long have you been working with it in shops?
Hollevoet: We started in 2010.
Matties: So you have some history with it.
Hollevoet: We have indeed some history with it. Now we have to develop it further and support the adoption in the market. We are also discovering new markets that have been developing only recently. One example is the oil and gas market—before oil and gas was drilled down to 1,000 to 2,000 meters but now they go much deeper. So now suddenly they find out that the traditional materials they use today go out of their capability range and start to delaminate, dissolve or don't resist the more hostile environment. I think that's where today the market is opening up more than it was in 2010 or before.
Matties: If a fabricator adopts this, does this open up new market potential for them to increase their revenue?
Hollevoet: I think it's in the high-end markets where we're looking at this material to be used where performance and reliability prevail and where the current materials no longer meet the requirements of the OEMs. These markets are definitely on the rise.
Matties: So they can come in with a new solution and perhaps keep a customer, or gain a customer?
Hollevoet: Yeah, the fabricator can create more value now because they can offer material that is extending the customer’s current capabilities, and like I said, some major markets are pushing the boundaries to extreme temperatures. The second market opportunity for XT/duroid material is where the circuits have to be very chemical resistant, like in anything related to fumes, fuels etc.
PEEK is also a material that is radiation resistant. So any application dealing with X-rays or gamma rays, because that's where materials tend to oxidize extremely rapidly, is a potential fit for XT/duroid material. As you notice, there are all kinds of new markets that have needs that can't be met with current materials.
Matties: It sounds like a product like this could also help somebody enter into a new market.
Hollevoet: It definitely helps because it enables new technologies in more extreme environments beyond the limits of today.
Matties: Is there anything that we haven't talked about that we should cover around this?
Hollevoet: Another interesting aspect of the material is that it can go very thin. We start at 2 mil (50µm), with or without woven glass, and it can go much thicker from there. It's flexible at first and as it gets thicker with more glass we can make it stiffer. It is halogen-free but it's inherently flame retardant and there are no toxic fumes, which is an environmental concern that's alive today.
This material is laminated without any adhesive. That enables us to reduce the thickness. The adhesive is also most often the weakest spot in the laminate. It's the first that's going to dissolve. It's the first that's going to oxidize or pick up moisture, so if you can avoid this by eliminating the adhesive you have made a big step forward.
Matties: In the space that you're describing, the extreme high-end, is this the total replacement product for everything that's now being used? Is that what you guys see when you're blue skying this?
Hollevoet: I don't think it is just a drop-in replacement. It can overlap with a lot of things today but I think the real use will be mainly at the edge and beyond the capabilities of the current materials. Some of the materials today, like polyimide, have been so commoditized nowadays that there's definitely a price difference with this material. When you're at the edge of the current technology and current materials, that's where we can step in and make a difference.
Matties: Sounds great, thanks for sharing all this with us today. It's really interesting and we wish you the best of success.
Hollevoet: Thank you very much.
Suggested Items
The Evolution of Picosecond Laser Drilling
06/19/2025 | Marcy LaRont, PCB007 MagazineIs it hard to imagine a single laser pulse reduced not only from nanoseconds to picoseconds in its pulse duration, but even to femtoseconds? Well, buckle up because it seems we are there. In this interview, Dr. Stefan Rung, technical director of laser machines at Schmoll Maschinen GmbH, traces the technology trajectory of the laser drill from the CO2 laser to cutting-edge picosecond and hybrid laser drilling systems, highlighting the benefits and limitations of each method, and demonstrating how laser innovations are shaping the future of PCB fabrication.
Day 2: More Cutting-edge Insights at the EIPC Summer Conference
06/18/2025 | Pete Starkey, I-Connect007The European Institute for the PCB Community (EIPC) summer conference took place this year in Edinburgh, Scotland, June 3-4. This is the third of three articles on the conference. The other two cover Day 1’s sessions and the opening keynote speech. Below is a recap of the second day’s sessions.
Day 1: Cutting Edge Insights at the EIPC Summer Conference
06/17/2025 | Pete Starkey, I-Connect007The European Institute for the PCB Community (EIPC) Summer Conference took place this year in Edinburgh, Scotland, June 3-4. This is the second of three articles on the conference. The other two cover the keynote speeches and Day 2 of the technical conference. Below is a recap of the first day’s sessions.
Preventing Surface Prep Defects and Ensuring Reliability
06/10/2025 | Marcy LaRont, PCB007 MagazineIn printed circuit board (PCB) fabrication, surface preparation is a critical process that ensures strong adhesion, reliable plating, and long-term product performance. Without proper surface treatment, manufacturers may encounter defects such as delamination, poor solder mask adhesion, and plating failures. This article examines key surface preparation techniques, common defects resulting from improper processes, and real-world case studies that illustrate best practices.
RF PCB Design Tips and Tricks
05/08/2025 | Cherie Litson, EPTAC MIT CID/CID+There are many great books, videos, and information online about designing PCBs for RF circuits. A few of my favorite RF sources are Hans Rosenberg, Stephen Chavez, and Rick Hartley, but there are many more. These PCB design engineers have a very good perspective on what it takes to take an RF design from schematic concept to PCB layout.