-
-
News
News Highlights
- Books
Featured Books
- pcb007 Magazine
Latest Issues
Current IssueThe Hole Truth: Via Integrity in an HDI World
From the drilled hole to registration across multiple sequential lamination cycles, to the quality of your copper plating, via reliability in an HDI world is becoming an ever-greater challenge. This month we look at “The Hole Truth,” from creating the “perfect” via to how you can assure via quality and reliability, the first time, every time.
In Pursuit of Perfection: Defect Reduction
For bare PCB board fabrication, defect reduction is a critical aspect of a company's bottom line profitability. In this issue, we examine how imaging, etching, and plating processes can provide information and insight into reducing defects and increasing yields.
Voices of the Industry
We take the pulse of the PCB industry by sharing insights from leading fabricators and suppliers in this month's issue. We've gathered their thoughts on the new U.S. administration, spending, the war in Ukraine, and their most pressing needs. It’s an eye-opening and enlightening look behind the curtain.
- Articles
- Columns
- Links
- Media kit
||| MENU - pcb007 Magazine
Estimated reading time: 9 minutes
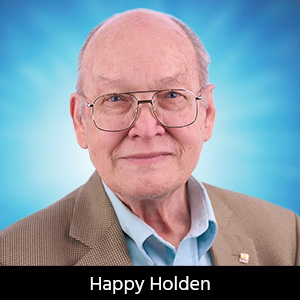
Contact Columnist Form
Producibility and Other Figures of Merit
Metrics are data and statistically backed measures. It is always expedient to base decisions on data and metrics, for example, in PCB design[1]. These measures can be density, first-pass yield[2] connectivity or in this context, producibility[3]. These measures are the basis for predicting and planning a printed circuit design. But what if a metric doesn’t exist? Then you can create the next best measure, the Figure of Merit.
The Figure of Merit
When used in the design, or any process, there are four categories of measures applied to a product:
- Metrics: Both the product and the process are measured by physical data using SPC and TQM techniques. (The Predictive Engineering Process)
- Figure of Merit (FOM): Both the product and the process are scored by linear equations developed by consensus expert opinion. (The Expert Opinion Process)
- Opinion: Opinion, albeit from an expert, is applied after or concurrent with design. (The Manufacturing Engineering Inspection Process)
- No Opinions: No attempt to inspect or improve the design/process is done during the specification, partitioning, or design stage. (The Over The Wall Process)
The critical parameter in the calculation of first pass yield (FPY) is the Figure of Merit—the Complexity Index. This is a dimensionless parameter that is what I call a pseudo-independent variable—it replaces a number of important independent variables that would be complicated if taken individually. This variable is invented, but it follows after a number of pseudo-independent variables that are essential for modern engineering, such as the dimensionless numbers (to be discussed in a future column near the end of the year). An example that you might remember is the Reynolds number (a measure of inertia force divided by viscous force) used in fluid flow calculations. The Reynolds number was first described quantitatively by Reynolds in 1883. Reynolds found that fluid velocity (l/t), fluid density (m/l), fluid viscosity (ml/t) and pipe diameter (l) determined the nature of pipe flow. The four variables, combined into a single dimensionless parameter. In fact, there are 154 dimensionless parameters used in engineering and nearly 304 variables whose ratios form non-dimensional numbers. Many of you might remember or work with some of these: Mach number, Stanton, Grashof, Euler, Prandtl or Knudsen. With this large body of work, there was no reason why I could not create the Complexity Index to represent all the critical variables in PCB fabrication.
It is always preferred to have metrics when discussing producibility. But if metrics are not available, then opinions are better than nothing. The problem with opinions is that they are difficult to defend and explain and when used in conjunction with producibility and many times they vary with each person. Attempts to remedy this problem by placing experienced manufacturing engineers in the design team have somewhat useful effects but there lies the problem that experienced manufacturing engineers take many years to educate and are needed on the factory floor. Design teams can be populated with college graduates! There just aren’t enough experienced manufacturing engineers to go around. That is why the Figure of Merit (FOM) process is so popular. For a small amount of work by experts it produces a scoring procedure that can be used and understood by all. With a FoM, a new college graduate in manufacturing engineering can assume the role of a much more experienced manufacturing engineer.
Metrics also establish a common language that links manufacturing to design. The "producibility scores" form a non-opinionated basis that allows a team approach that results in a quality, cost competitive product. This approach will be used to establish the design for manufacturing & assembly (DFM/A) in my next column.
The strategy in applying these measures is shown in Figure 1. The analysis process is unique to every individual and company, but certain conditions have to be met and considered if the product is going to be successful. If the score meets producibility requirements then select this approach, if not, then evaluate other opportunities and repeat the process.
Figure 1: The Figure of Merit creation process.
Creating a Figure Of Merit
Metrics are the preferred measures for design planning, but their availability for predicting producibility are limited today. Metrics also can take many months to develop and the amount of experimentation may make them costly. The measure that is much more cost effective and quicker to develop is the Figure of Merit. The Figure of Merit is the result of one or two days’ work by a group of design and manufacturing experts. The process is a nine-step procedure as follows:
- Define new measure (FOM)
- Determine why selected
- Survey customers for needs and expectations
- Brainstorm factors
- Sort ideas into groups
- Create group header definitions
- Prioritize groups
- Construct factor weighting value tables
- Create linear model for FOM
This procedure uses classical TQM techniques to brainstorm, rank and formulate an equation that will score producibility, assembly-ability or any other measure that can be used to do design planning. The two factors used in the producibility score are made up of 1) coefficient (CN) and 2) factor weighting (FWN).
1. Define the new measure
Define or identify the new measure to be developed. What property of a product would gain you the most competitive advantage? Manufacturability, DfM, Reparability, Serviceability, Testability, Reliability, Low Cost or Rapid Time-to-Market.
2. Determine why selected
Ensure that there is relevance to improved performance and communication if this FOM is developed. Are they part of this team? How does the new FOM improve the product?
3. Survey customers for needs and expectations
Who are the intended users of this FOM? Identify their needs and expectations. Collect data by surveys, interviews, or brainstorming of contributing characteristics or variables.
4. Brainstorm factors
Collect a team of experts that have a vested ownership of this new FOM. Invest in a facilitator to keep the activities rolling and on schedule. Giving everyone plenty of cards or Post-its, go around the team and collect ideas of what is important for this new Measure of FOM. Allow plenty of time. If the ideas stop coming, take a break and resume. Have the facilitator push for one more idea. There are no discussions or arguments during brainstorming—just ideas. Randomly lay out the cards so that all the team members can see them. Take as much room as it needs.
Figure 2: Arrange all the ideas so everyone can see them.
5. Sort ideas into groups
The purpose of this step is to collect those that go with each other. In silence, all team members should simultaneously begin moving the idea cards, collecting and arranging in columns the cards that each person believes belong together. All the cards should remain visible during this process so that everyone can consider the arrangement as it emerges. If cards are redundant, overlap them but in such a way that both can be read. Team members should freely change cards between groupings or create new groupings as they feel appropriate. Team members are allowed to disagree with a placement by making a new placement or returning to a previous one. Back and forth moves may occur for some time until the team settles on an arrangement that is acceptable to everyone. Some cards (ideas) may be loners that do not seem to fit in any grouping. They should be left that way rather than try to force-fit in any grouping. The facilitator helps resolve conflicts about ideas by changing their definition or creating a new Group.
6. Create header card for each group
The facilitator helps create with the team a header or definition of each group that captures the essential link among all of the ideas in that group and consists of enough words to clearly convey the meaning. Look for one idea that ties the whole group together. In many cases that central idea will not exist yet on a card. If it does not, the team should decide on a central idea and create a concise definition, usually three to five words. Figure 3 shows a photo of the idea grouping and the group headers.
Figure 3: The finished ideas groupings with headers.
7. Prioritize and rate each group
The Team needs to prioritize and rank each of the groups created by the last two steps (5 & 6). Three methods can be use:
Mulitvote: Each member of the team is given a fixed number of votes (usually the number of groups divided by three) to cast to the groups he/she thinks is the most important.
Ranking Vectors: Arrange each group in circular layout and connect by arrows as to which affects the other. Count the arrow-starts to give scores (Figure 4).
Figure 4: The Ranking Vectors method of determining prioritization.
Paired Ranking: This is the method I prefer. It simplifies the choices for voting and is the easiest to interpret. This is seen in Figure 5. Each Group is listed in the horizontal and vertical axis. A diagonal line is drawn. Discussion and voting is performed on each pair; 1-2, 1-3, 1-4, 1-5, then 2-3 (already did 2-1), 2-4, 2-5, then 3-4, 3-5 and finally 4-5. Which group wins get a “PLUS +”, ties get 0 and losers get “negative –“. The +, 0 and – are placed in opposite on the other side of the diagonal.
Figure 5: The Paired Ranking voting table and results (wins).
Coefficient-CN: The coefficients in the producibility score are the result of the prioritization process (Step 7). The actual voting scores of ‘wins+’ form the coefficients, Cn. In Figure 5, that is; 1 has 2 wins, 2 has 3 wins, 4 has none and is dropped (coefficient of 0) and 5 has 2 wins.
8. Construct factor weighting (FW) table
Each factor that emerges from the ranking process is calibrated by assigning values from one to 100 as seen in Figure 6. The "1" factor are easy to manufacture and the "100" factor are impossible today but merely very difficult in a few years. In my example, the measure is “minimum drill diameter size” and values are assigned for 1-25-50-75 and 100.
Figure 6: The Factor Weighting Table is used to calibrate the ‘measured’ group from one to 100.
9. Create lLinear model for FOM
The resulting scoring equation will look like the linear equation below (sum of CnFWn) and would be used like this:
SCORE = (C1) (FW1) + (C2) (FW2) + (C3) (FW3) + (Cn) (FWn) + ....
For example, if we assume the producibility of a bare PWB may be scored with the above equation if the following factors were established by the F.O.M. Process:
1. Size of the substrate C1 = 1.5
2. Number of drilled holes C2 = 3.0
3. Minimum trace width C3 = 4.0
Where the proposed PWB design has:
1. Size of the substrate FW1 = 36
2. Number of drilled holes FW2 = 18
3. Minimum trace width FW3 = 31
The producibility score would equal: (1.5 x 36) + (3.0 x 18) + (4.0 x 31) = 54 + 54 + 124 = 232
As I sometimes tell people about the process, “It’s based on expert opinions, used over and over, but it is surprisingly accurate!”
References
- Holden, H., “Wiring Demand,” CircuiTree, June 1998.
- Holden, H., “First Pass Yield,” CircuiTree, Sept. 1998.
- Holden, H., “Producibility,” CircuiTree, Aug. 1998.
Happy Holden has worked in printed circuit technology since 1970 with Hewlett-Packard, NanYa/Westwood, Merix, Foxconn and Gentex. Currently, he is the co-editor, with Clyde Coombs, of the Printed Circuit Handbook, 7th Ed.
More Columns from Happy’s Tech Talk
Happy’s Tech Talk #39: PCBs Replace Motor WindingsHappy’s Tech Talk #38: Novel Metallization for UHDI
Happy’s Tech Talk #37: New Ultra HDI Materials
Happy’s Tech Talk #36: The LEGO Principle of Optical Assembly
Happy’s Tech Talk #35: Yields March to Design Rules
Happy’s Tech Talk #34: Producibility and Other Pseudo-metrics
Happy’s Tech Talk #33: Wet Process Management and Control
Happy’s Tech Talk #32: Three Simple Ways to Manage and Control Wet Processes