-
- News
- Books
Featured Books
- pcb007 Magazine
Latest Issues
Current IssueThe Hole Truth: Via Integrity in an HDI World
From the drilled hole to registration across multiple sequential lamination cycles, to the quality of your copper plating, via reliability in an HDI world is becoming an ever-greater challenge. This month we look at “The Hole Truth,” from creating the “perfect” via to how you can assure via quality and reliability, the first time, every time.
In Pursuit of Perfection: Defect Reduction
For bare PCB board fabrication, defect reduction is a critical aspect of a company's bottom line profitability. In this issue, we examine how imaging, etching, and plating processes can provide information and insight into reducing defects and increasing yields.
Voices of the Industry
We take the pulse of the PCB industry by sharing insights from leading fabricators and suppliers in this month's issue. We've gathered their thoughts on the new U.S. administration, spending, the war in Ukraine, and their most pressing needs. It’s an eye-opening and enlightening look behind the curtain.
- Articles
- Columns
- Links
- Media kit
||| MENU - pcb007 Magazine
The Newest Flex Shop in the U.S.
July 7, 2016 | Barry Matties and Angela Alexander, I-Connect007Estimated reading time: 27 minutes
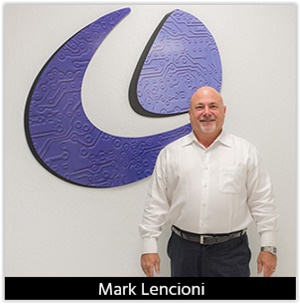
I-Connect007 sales team member Angela Alexander and I recently got a tour of Lenthor’s new Silicon Valley flex board shop and then sat down with President and CEO Mark Lencioni to discuss the new flex facility, the markets, management, and the future.
Barry Matties: Mark, give our readers a little background on Lenthor Engineering and what you do.
Mark Lencioni: We are entering our 31st year of business; having been founded in 1985. We are now located in our brand new, 55,000 sq. ft. state-of-the-art facility dedicated specifically to the fabrication and assembly of flex and rigid-flex products. We made it as “Lean” as possible for all our manufacturing systems to be very close to each other, in order to get the most efficiencies with our employees and product movement. It came out just like we planned.
Matties: So is Lenthor a flex shop primarily?
Lencioni: Yes, we specialize in flex circuit fabrication and assembly. We specialize in multilayer and rigid-flex technology, very high aspect ratios, high layer counts, and the technology to allow packaging to get into the size and shape it needs to be. We have succeeded by satisfying the toughest demands from the most demanding customers in the world.
Matties: Flex is still one of the fastest growing areas in the marketplace.
Lencioni: Yes, our customers’ products are the largest they will ever be and flex circuits are a natural solution to help people package things in the size and shape they need to be. They're getting smaller and smaller. From wearable devices, to cellphones, to any kind of mechanical device, automotive, military equipment, and some semiconductor equipment processing.
Matties: In your 30+ years, what's the most surprising thing you have seen in the flex market?
Lencioni: I would say the growth in both medical and military. We didn't really appreciate the opportunity these markets held for us until we did some specific market research after 9/11. The results of that research are what led us to move more heavily into these markets. If you look at the world and the environment we are in, these marketplaces are poised to be well-established for many, many years to come.
Matties: Your facility is an ITAR facility; what's the percentage of work that you bring through here?
Lencioni: We are about 55% military, 25% medical, and the rest balances across industrial and telecom.
Matties: Where do you see the largest growth coming from right now?
Lencioni: Military and Medical. Military obviously is in a very stable environment because it doesn't go offshore. We are finding growth from within a market that we are already well positioned to support. The medical market is also very favorable for us. We have developed the kind of process validation and control that market insists on.
Matties: Going back to your new facility, who laid out the facility?
Lencioni: It was a combination of Rich Clemente and myself. We took the processes, and with help from engineers regarding where they needed to be, we just started to lay it out. We did that with an architect, and so whatever building we decided to go into we just took that footprint and laid it right in.
Matties: When you are laying out a facility like this, what's the goal?
Lencioni: The goals were product efficiency and people movement. To really make sure that the product started finished within the most efficient process path, minimizing as best we could the movement and handling of materials.
Matties: When we first started the tour we talked about your old facility and the length of that process.
Lencioni: Yes, we had a campus environment previous to this which included three separate buildings. Although they were across the parking lot from each other, the movement of materials from beginning to end was about 2.2 miles. We re-validated what it is in our new factory and depending on product type the movement is down to about one eighth of a mile. The product moves with more efficiency, it doesn't get mishandled, and the employees are able to stay focused on their job of producing boards instead of moving materials.
Page 1 of 5
Suggested Items
Copper Price Surge Raises Alarms for Electronics
07/15/2025 | Global Electronics Association Advocacy and Government Relations TeamThe copper market is experiencing major turbulence in the wake of U.S. President Donald Trump’s announcement of a 50% tariff on imported copper effective Aug. 1. Recent news reports, including from the New York Times, sent U.S. copper futures soaring to record highs, climbing nearly 13% in a single day as manufacturers braced for supply shocks and surging costs.
I-Connect007 Editor’s Choice: Five Must-Reads for the Week
07/11/2025 | Andy Shaughnessy, Design007 MagazineThis week, we have quite a variety of news items and articles for you. News continues to stream out of Washington, D.C., with tariffs rearing their controversial head again. Because these tariffs are targeted at overseas copper manufacturers, this news has a direct effect on our industry.I-Connect007 Editor’s Choice: Five Must-Reads for the Week
Digital Twin Concept in Copper Electroplating Process Performance
07/11/2025 | Aga Franczak, Robrecht Belis, Elsyca N.V.PCB manufacturing involves transforming a design into a physical board while meeting specific requirements. Understanding these design specifications is crucial, as they directly impact the PCB's fabrication process, performance, and yield rate. One key design specification is copper thieving—the addition of “dummy” pads across the surface that are plated along with the features designed on the outer layers. The purpose of the process is to provide a uniform distribution of copper across the outer layers to make the plating current density and plating in the holes more uniform.
Trump Copper Tariffs Spark Concern
07/10/2025 | I-Connect007 Editorial TeamPresident Donald Trump stated on July 8 that he plans to impose a 50% tariff on copper imports, sparking concern in a global industry whose output is critical to electric vehicles, military hardware, semiconductors, and a wide range of consumer goods. According to Yahoo Finance, copper futures climbed over 2% following tariff confirmation.
Happy’s Tech Talk #40: Factors in PTH Reliability—Hole Voids
07/09/2025 | Happy Holden -- Column: Happy’s Tech TalkWhen we consider via reliability, the major contributing factors are typically processing deviations. These can be subtle and not always visible. One particularly insightful column was by Mike Carano, “Causes of Plating Voids, Pre-electroless Copper,” where he outlined some of the possible causes of hole defects for both plated through-hole (PTH) and blind vias.