-
-
News
News Highlights
- Books
Featured Books
- smt007 Magazine
Latest Issues
Current IssueSupply Chain Strategies
A successful brand is built on strong customer relationships—anchored by a well-orchestrated supply chain at its core. This month, we look at how managing your supply chain directly influences customer perception.
What's Your Sweet Spot?
Are you in a niche that’s growing or shrinking? Is it time to reassess and refocus? We spotlight companies thriving by redefining or reinforcing their niche. What are their insights?
Moving Forward With Confidence
In this issue, we focus on sales and quoting, workforce training, new IPC leadership in the U.S. and Canada, the effects of tariffs, CFX standards, and much more—all designed to provide perspective as you move through the cloud bank of today's shifting economic market.
- Articles
- Columns
- Links
- Media kit
||| MENU - smt007 Magazine
Six Sigma: What is it and How is it Used in Electronics Manufacturing?
January 19, 2017 | Neil Sharp, JJS ManufacturingEstimated reading time: 4 minutes
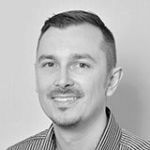
"Six Sigma is a quality program that, when all is said and done, improves your customer's experience, lowers your costs, and builds better leaders." – Jack Welch
Six Sigma: it sounds like something out of a Dan Brown novel. But it's not a mystery to be unraveled; rather, it is a defined, data-driven methodology aimed at process improvement and consistent output in manufacturing.
Although it was originally developed by Motorola in 1986, Six Sigma is more commonly associated with General Electric (GE). Jack Welch, the former chairman and CEO of GE, made Six Sigma a core component of his business strategy during his twenty-year tenure. It is now an entrenched business philosophy at the organization.
Today, Six Sigma is utilized across industries. So, what does it involve and what does it look like in practice?
What is Six Sigma?
"In contrast with other quality initiatives, Six Sigma recognises that there is a direct correlation between the number of product defects, wasted operating costs, and the level of customer satisfaction." – Process Quality Associates Inc (PQA)
Six Sigma revolves around reducing errors, to deliver better products and services – thereby improving the customer experience and increasing profit. It's essentially a quest for perfection – although, of course true perfection is impossible to achieve.
The term "sigma" derives from the eighteenth letter of the Greek alphabet (Σ, σ, ς). A Six Sigma process is one in which 99.99966 per cent of products created are free of defects; to put it another way, there should be no more than 3.4 defects per million opportunities (DPMO).
A defect is anything that falls outside of a standard process – that is, a variation. And, in electronics manufacturing, this measurement can be used in relation to anything from a component to a period of time. These calculations are rooted in mathematics and statistics and are further explained here [1] and here [2].
GE outlines the key concepts that inform Six Sigma as follows:
- Critical to quality – attributes most important to the customer.
- Defect – failing to deliver what the customer wants.
- Process capability – what your process can deliver.
- Variation – what the customer sees and feels.
- Stable operations – ensuring consistent, predictable processes to improve what the customer sees and feels.
- Design for Six Sigma – designing to meet customer needs and process capability.
Implementing Six Sigma
The successful deployment of Six Sigma is dependent on rolling it out across the entire organization.
The two main sub-methodologies for Six Sigma are: DMAIC and DMADV (also known as DFSS (Design for Six Sigma)). Both approaches are data-driven: the former is used to improve current business processes, while the latter focuses on creating new processes or products. Often, a business might implement DMAIC and then move on to DMADV.
iSixSigma defines each methodology as follows:
DMAIC
- Define – define the project goals and customer (internal and external) deliverables.
- Measure – measure the process to determine current performance.
- Analyze – analyze and determine the root cause(s) of the defects.
- Improve – improve the process by eliminating defects.
- Control – control future process performance.
DMADV
- Define – define the project goals and customer (internal and external) deliverables.
- Measure – measure and determine customer needs and specifications.
- Analyze – analyze the process options to meet the customer needs.
- Design – design (detailed) the process to meet the customer needs.
- Verify – verify the design performance and ability to meet customer needs.
Six Sigma is deployed by a number of key people across an organization, including:
- Champions - executive leaders, who oversee the Six Sigma vision and drive it forwards.
- Master Black Belts - experts in Six Sigma integration. These people are focused full-time on rolling out Six Sigma and act as in-house coaches.
- Black Belts - those directly responsible for the implementation of Six Sigma within an organization. They report to Master Black Belts and have advanced expertise.
- Green Belts - those who support the Black Belts and carry out many of the day-to-day tasks involved in each project.
This might all sound a bit complex and intimidating. However, it requires specialist training, in order to achieve success. There are a number of Six Sigma certification organizations, including professional associations, universities and for-profit training organizations.
Lean Six Sigma
More recently, Six Sigma has been combined with lean manufacturing to create a new methodology: Lean Six Sigma. Lean manufacturing is, of course, aimed at eliminating waste within manufacturing – and so the two complement one another well.
Lean is implemented to identify opportunities to decrease waste within the manufacturing process and then Six Sigma is used to decrease defects. Together, these two methodologies help to maximize customer satisfaction and profit.
Today, manufacturing firms exist in a challenging landscape. There is an increasing demand for customized products, which are expected to get to market faster than ever before – and, of course, the looming Fourth Industrial Revolution is disrupting the sector at its core.
Against this backdrop, it is more vital than ever to retain a competitive advantage. Implementing Six Sigma (and Lean Six Sigma) is an excellent way to ensure you remain on top.
References
2. www.pqa.net
This post originally appeared on the JJS Manufacturing blog, which can be found here.
Testimonial
"We’re proud to call I-Connect007 a trusted partner. Their innovative approach and industry insight made our podcast collaboration a success by connecting us with the right audience and delivering real results."
Julia McCaffrey - NCAB GroupSuggested Items
SEL: Revolutionizing PCB Production Through MES, Partnerships, and Vision
08/21/2025 | Barry Matties, I-Connect007Two years ago, we visited Schweitzer Engineering Laboratories (SEL) to better understand its new captive greenfield PCB facility. We recently returned, this time to discuss how this bold vision has transformed the industry. Barry Matties met with John Hendrickson, engineering director, and Jessi Hall, vice president of vertical integration, to discuss the transformative capabilities of Factory Core, SEL’s custom manufacturing execution system (MES), which allows for real-time monitoring of workflow and machine performance, and has led to impressive improvements in quality and cost efficiency.
Efficiency Unleashed: Breaking Down Lean and Six Sigma
06/02/2025 | Marcy LaRont, PCB007 MagazineAs a child in the late 1970s, I lived near Fremont, California, the home of the GM automotive manufacturing plant. At the time, GM had a terrible reputation for producing poor quality cars that were dwindling in popularity. I toured the GM plant while in elementary school. Each child received a pair of safety glasses before our group was escorted around the plant with our teacher. I remember seeing the car pieces on the line, and workers using blow torches to assemble the car together.
Marcy’s Musings: The Relentless Pursuit of Perfection
05/16/2025 | Marcy LaRont -- Column: Marcy's MusingsFew things in this world are or will ever be perfect. For me, perfection might look like the vivid colors that only Mother Nature can create, the birth of a child, and the inner workings of the human brain. But all else in this physical, tangible world is, in one way or another, inherently flawed. Even the “flawless” diamond is more about the sheer awe and beauty of beholding near-perfection than perfection itself. In many ways, this truth provides great texture and diversity to our world. Yet, we still strive for perfection, and it’s in this that we learn and achieve higher heights than we otherwise would have.
Uyemura Announces Six Sigma Graduates
04/02/2025 | UyemuraDr. Patrick Valentine, Technical & Lean Six Sigma Manager and Six Sigma Master Black Belt, announces the completion of Lean Six Sigma Black Belt training by 4 members of Uyemura’s professional staff.
IEC Collaborates with Supply Partners at IPC APEX EXPO 2025
01/29/2025 | IECIn keeping with its company's Supply Chain Motto of Collaboration – Innovation – Quality – Dedication, International Electronic Components, Inc. is excited to announce its collaboration with five other companies at the upcoming IPC Apex Expo 2025.