NASA Seeks 'FabLab' Concepts for In-Space Manufacturing
May 8, 2017 | NASAEstimated reading time: 2 minutes
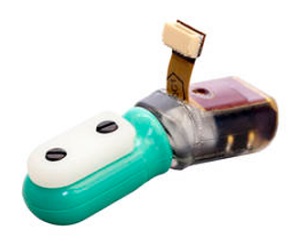
NASA is seeking proposals for development of a first-generation, in-space, multi-material fabrication laboratory, or FabLab, for space missions. The FabLab solicitation is issued as Appendix B of the Next Space Technologies for Exploration Partnerships (NextSTEP-2) Broad Agency Announcement.
Multi-material sensors like the one pictured above are vital to space ship operations, and need to be fabricated on demand during deep space missions.
The FabLab development path will be implemented in three phases with the objective of the final phase to demonstrate a commercially developed FabLab on the International Space Station. This solicitation seeks responses only to Phase A, in which private industry partners will produce ground-based prototypes with a measurable ability to mature into flight demonstrations on the space station within three years.
FabLab is part of a broad agency strategy and series of investments managed by NASA's Advanced Exploration Systems Division (AES) and Space Technology Mission Directorate (STMD) to advance key technology capability areas. According to Jason Crusan, director of AES, which also manages NextSTEP, FabLab is a logical extension of in-space manufacturing following the success of 3-D printing plastics on the space station.
International Space Station astronaut Barry “Butch” Wilmore holds a science sample container that took two hours to make in December 2014. The container was the first object to be printed with two parts: a lid and a container.
“We’ve already seen the benefits of on-demand manufacturing for tools and replacement parts on station,” said Crusan. “We want to increase the number of materials we can use to manufacture items on-demand in space and improve overall manufacturing efficiencies as well.” He added that in-space manufacturing ultimately should become an end-to-end process, capable of recycling feedstock as well as harvesting it from extraterrestrial sources.
For FabLab Phase A, NASA is requesting ground prototypes designed to be compatible with the space station’s EXPRESS Racks and capable of remote-controlled operations from Earth to manufacture multi-material components, including metals. Phase A selectees will have 18 months to deliver the prototype, after which NASA will determine which, if any, partners will continue to Phase B to further mature their technologies on the NextSTEP development path. Phase B details, including the maturation path to the final Phase C, will be released under a separate solicitation.
“Having an integrated capability for on-demand manufacturing and repair of components and systems during space missions will be integral for sustainable exploration missions,” said Jim Reuter, deputy associate administrator for STMD Programs. “This is a rapidly-evolving, disruptive area in which NASA wants to continue working with industry and academia to develop these technologies through collaborative mechanisms such as this one.” He adds, “This BAA solicitation has great potential for developing meaningful applications for space missions, as well as direct terrestrial commercial infusion.”
NextSTEP is a public-private partnership cost-sharing development model managed by AES that advances deep space exploration capabilities to support human missions in deep space. Small businesses, as defined by NASA’s Small Business Innovative Research Program, are eligible for pro-rated cost-sharing agreements when partnering to develop capabilities for this NextSTEP Appendix.
NASA will host an informational industry forum to address questions, tentatively scheduled for May 25, 2017 at 11 a.m. EDT. Final inquiries from prospective responders to the NextSTEP-2 Appendix B are due June 2, 2017, and notices of intent (NOIs) are encouraged to be provided by June 16. Proposals are due August 2, 2017.
Suggested Items
TTCI Joins Printed Circuit Engineering Association to Strengthen Design-to-Test Collaboration and Workforce Development
07/09/2025 | The Test Connection Inc.The Test Connection Inc. (TTCI), a leading provider of electronic test and manufacturing solutions, is proud to announce its membership in the Printed Circuit Engineering Association (PCEA), further expanding the company’s efforts to support cross-functional collaboration, industry standards, and technical education in the printed circuit design and manufacturing community.
GlobalFoundries to Acquire MIPS to Accelerate AI and Compute Capabilities
07/09/2025 | GlobalFoundriesGlobalFoundries announced a definitive agreement to acquire MIPS, a leading supplier of AI and processor IP. This strategic acquisition will expand GF’s portfolio of customizable IP offerings, allowing it to further differentiate its process technologies with IP and software capabilities.
LITEON Technology Reports Consolidated June Sales of NT$13.6 Billion, Up 16% Y-o-Y
07/08/2025 | LITEON TechnologyLITEON Technology reported its June consolidated revenue of NT$13.6 billion. Thanks to the growth from power management in cloud computing, advanced server, and networking, the revenue is up 2% M-o-M, 16% Y-o-Y. The cumulative sales for January to June totaled NT$76.8 billion, up 24%, Y-o-Y.
Inside Aimtron’s Cross-border EMS Strategy
07/08/2025 | Nolan Johnson, SMT007 MagazineMukesh Vasani immigrated from a very small farming village in India to the U.S. in 1995 as a civil engineer. After shifting into electronics, Mukesh built his Chicago-based company, Aimtron, into a successful enterprise by combining quality with competitive pricing. He leveraged his roots in India to expand manufacturing without compromising on quality.
Be the Partner Engineers Can Rely On
07/08/2025 | Nolan Johnson, SMT007 MagazineGreen Circuits’ unique niche in the electronics manufacturing industry comes partly from its location in Silicon Valley, but also from its specialty of serving up quick-turn prototypes and low-volume work with high-complexity production. In this conversation, CEO Michael Hinshaw emphasizes the value of end-to-end services, especially while the pace of R&D development is accelerating amidst a growing demand for complexity across industries.