-
-
News
News Highlights
- Books
Featured Books
- smt007 Magazine
Latest Issues
Current IssueWhat's Your Sweet Spot?
Are you in a niche that’s growing or shrinking? Is it time to reassess and refocus? We spotlight companies thriving by redefining or reinforcing their niche. What are their insights?
Moving Forward With Confidence
In this issue, we focus on sales and quoting, workforce training, new IPC leadership in the U.S. and Canada, the effects of tariffs, CFX standards, and much more—all designed to provide perspective as you move through the cloud bank of today's shifting economic market.
Intelligent Test and Inspection
Are you ready to explore the cutting-edge advancements shaping the electronics manufacturing industry? The May 2025 issue of SMT007 Magazine is packed with insights, innovations, and expert perspectives that you won’t want to miss.
- Articles
- Columns
- Links
- Media kit
||| MENU - smt007 Magazine
Thermal Indicator Technology for Aerospace Wire Harness Assemblies
July 19, 2017 | Jerry Sidone, Alpha Assembly SolutionsEstimated reading time: 5 minutes
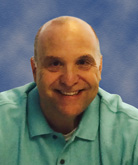
Solder preform sleeves are designed to fit any wire termination. They are used in aerospace wire harness assemblies for wire splicing, RF cable assembly and pin and connector terminations. Most often you will see them integrated with heat shrink tubing. The heat shrink tubing provides an environmental barrier for the solder connection.
Solder sleeves of different alloys are used because of many factors. These can include location in the aircraft and the operational temperature for the connection. For example, an operating temperature rating of 125–150°C (deploys SnBi, SnPbCd, and SnPb) are for aircraft wings and body and 175°C ratings (deploying SnAg4) are used near the engines. Solder alloys are classified as low and high temperature alloys. It is extremely important for the solder operation to be done correctly and be verifiable. Reliability of the solder joint is directly related to safety. Whenever possible, eutectic alloys are used because their liquidous and solidus temperatures are the same, leaving little doubt to the operator when the solder is molten. This is the first indication to the operator that they are reaching proper melting temperatures. However, to form a reliable solder joint, temperatures should reach 20–30°C above the melt temperature range of the solder alloy.
Determining if a solder joint was formed correctly can be very subjective and difficult to regulate, especially in a mass production environment with multiple operators involved. Various industry specifications describe methods to test for a good interconnection both electrically and mechanically, but these methods (especially mechanical tests) are not conducive to a production environment.
For example, mechanical pull tests are conducted during the development phase of the cable assembly to determine the strength of the solder joint. However, they are not intended to be used at assembly since most of the testing is destructive. Most often, visual aids such as sketches or photos depicting good and bad solder joints are used as visual go/no-go gauges. In many cases, OEMs require that preform solder sleeves be integrated with crimp connectors to provide a redundant fail-safe solution due to the catastrophic failure that can occur.
The necessity of having a reliable solder joint in a cable or wire harness cannot be understated in aerospace applications. In addition to selecting the right alloy, you must take into account what makes a good solder joint: (1) the right type and amount of flux; (2) an adequate amount of heat; (3) correct amount of time; and (4) correct volume of solder. All are required to form a good intermetallic solder joint. Too much heat or applying the heat too long allows the solder to wick up the wire and under the insulation, reducing the amount of solder and weakening the joint. Too little heat will cause a cold solder joint where an intermetallic between the solder and the conductor is not completely formed and produces a solder joint susceptible to cracking or failure. Either of these can be disastrous at 40,000 feet.
Thermal indicator technology was developed into solder sleeves many years ago and has proven to be an effective means of providing visual indication of a reliable solder joint. There are two types of thermal indicators used in aerospace applications today: thermochromic dyes and solder fuse rings. Both the thermochromic dyes and fuse rings activate at a specified temperature above the base solder’s melting temperature range indicating sufficient heat and time have been applied to generate a good solder joint. The benefit of this type of technology is that it is an obvious signal to the operator during the soldering process that the solder joint is complete and the heat can be removed. An added benefit of thermal indicator technology allows quality control to perform spot inspections at any time.
Thermochromic dyes are designed to change color at specified temperature range. Thermochromic dyes are integrated into the external flux coating of the sleeve and forms the base color of the sleeve. When the solder sleeve reaches its melting temperature range, the dye begins to transition to a different color known as the activation color. When the dye on the solder sleeve finishes its color transition to the activation color, the solder joint is complete. The most popular thermal indicator dye used in aerospace today transitions from red to clear.
Figure 1: The thermal indicator technology in solder sleeves is an effective means of providing visual indication of a reliable solder joint.
Most recent advances in thermochromic dye technology are providing a more durable finish, more brilliant and contrasting base and activation colors which are giving users many more color options. The color options are a function of the dyes’ temperature activation ranges and therefore cannot be randomly selected to fit a user’s desired color change pallet. The user should contact the solder preform provider to determine the available color options for their solder melting range. In some instances, multiple color activation ranges are available at the same transition range providing a wider selection of color options.
Fuse alloy rings integrated into the solder sleeve are another type of thermal indicator used in the aerospace industry. The fuse alloy ring is integrated with the solder sleeve and used as the visual indicator to the operator or quality inspector. The solder sleeve and fuse alloy rings are made from different alloys. A solder ring of a higher melt point alloy is fitted over the outside circumference of the base alloy sleeve. The solder ring’s melt temperature range is a specified set temperature above the base solder sleeve alloy. When the solder ring melts, the base sleeve alloy has melted properly and the solder joint forms. The fuse alloy ring can be dialed into any temperature range but are most commonly used with SnAg and SnPb alloys.
Thermal indicator technologies used with solder preforms are an effective means for determining a cable interconnection has been soldered correctly. They provide a visual indication to the operator and quality control inspector that adequate soldering temperatures have been reached. Thermal indicators provide a more accurate and visual verification of the solder joint than using a photo or sketch as a gauge for inspection. Recent advancements in thermal dye indicator technology are providing a more durable coating and brilliant color selections.
Suggested Items
Knocking Down the Bone Pile: Addressing End-of-life Component Solderability Issues, Part 4
07/15/2025 | Nash Bell -- Column: Knocking Down the Bone PileIn 1983, the Department of Defense identified that over 40% of military electronic system failures in the field were electrical, with approximately 50% attributed to poor solder connections. Investigations revealed that plated finishes, typically nickel or tin, were porous and non-intermetallic.
SHENMAO Strengthens Semiconductor Capabilities with Acquisition of PMTC
07/10/2025 | SHENMAOSHENMAO America, Inc. has announced the acquisition of Profound Material Technology Co., Ltd. (PMTC), a premier Taiwan-based manufacturer of high-performance solder balls for semiconductor packaging.
KYZEN to Highlight Understencil and PCB Cleaners at SMTA Querétaro Expo and Tech Forum
07/09/2025 | KYZEN'KYZEN, the global leader in innovative environmentally responsible cleaning chemistries, will exhibit at the SMTA Querétaro Expo & Tech Forum, scheduled to take place Thursday, July 24, at Centro de Congresos y Teatro Metropolitano de Querétaro.
Driving Innovation: Direct Imaging vs. Conventional Exposure
07/01/2025 | Simon Khesin -- Column: Driving InnovationMy first camera used Kodak film. I even experimented with developing photos in the bathroom, though I usually dropped the film off at a Kodak center and received the prints two weeks later, only to discover that some images were out of focus or poorly framed. Today, every smartphone contains a high-quality camera capable of producing stunning images instantly.
Hands-On Demos Now Available for Apollo Seiko’s EF and AF Selective Soldering Lines
06/30/2025 | Apollo SeikoApollo Seiko, a leading innovator in soldering technology, is excited to spotlight its expanded lineup of EF and AF Series Selective Soldering Systems, now available for live demonstrations in its newly dedicated demo room.