-
- News
- Books
Featured Books
- smt007 Magazine
Latest Issues
Current IssueSpotlight on India
We invite you on a virtual tour of India’s thriving ecosystem, guided by the Global Electronics Association’s India office staff, who share their insights into the region’s growth and opportunities.
Supply Chain Strategies
A successful brand is built on strong customer relationships—anchored by a well-orchestrated supply chain at its core. This month, we look at how managing your supply chain directly influences customer perception.
What's Your Sweet Spot?
Are you in a niche that’s growing or shrinking? Is it time to reassess and refocus? We spotlight companies thriving by redefining or reinforcing their niche. What are their insights?
- Articles
- Columns
- Links
- Media kit
||| MENU - smt007 Magazine
Estimated reading time: 3 minutes
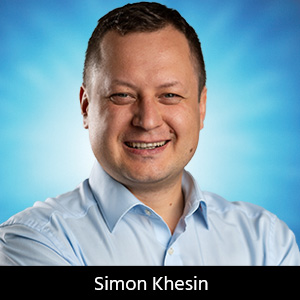
Driving Innovation: Direct Imaging vs. Conventional Exposure
My first camera used Kodak film. I even experimented with developing photos in the bathroom, though I usually dropped the film off at a Kodak center and received the prints two weeks later, only to discover that some images were out of focus or poorly framed. Today, every smartphone contains a high-quality camera capable of producing stunning images instantly. Since the early 2000s, a similar transformation has been unfolding in the PCB industry: the advancement of direct imaging (DI) technology. In this article, I’ll examine this ongoing shift by comparing direct imaging with conventional exposure across several key criteria.
Accuracy and Quality
Which technology offers higher accuracy and better results? Direct imaging (DI)clearly outperforms conventional exposure. The latter depends heavily on the condition of phototools, which are sensitive to storage conditions and wear, making consistent, high-quality output difficult to maintain.
However, DI eliminates these variables. It also simplifies top-to-bottom alignment, providing much better precision. Considering that current DI systems can achieve line/space resolutions as fine as 4/4 microns—or even 2/2 microns in some cases—the choice in terms of accuracy and quality becomes obvious.
Technical Possibilities
The elimination of phototools opens up strong digital advantages. Since the DI system receives the pattern digitally, it can easily scale, rotate, or shift the image during or just before the exposure—without the need for new tooling. For inner layers, updated scaling coefficients can be applied directly from the CAM department. For outer layers and solder mask, the system can automatically align to drilled fiducials or contact pads under the solder mask, eliminating time-consuming phototool updates. Such possibilities are a must for current high-end board production.
Another major advantage is the DI machine’s integration with MES systems and traceability. It can read data-matrix codes, load the corresponding part program from a server or from MES, or generate and expose a unique code for each individual PCB. This improves traceability and process control.
DI enables high levels of automation, allowing seamless integration into fully automated production lines. For inner layers, these lines could include everything from dry film pre-treatment to resist stripping. For outer layers, the lines could run from dry film pre-treatment to development (depending on whether it’s pattern or panel plating).
Additionally, a DI system’s autofocus feature helps compensate for variations in panel thickness online during the exposure process, ensuring consistent imaging results across varying board conditions.
Costs
One might argue, “But conventional exposure is cheaper.” Is it really? When you consider not only the exposure unit but also the plotter, film developer, film storage, dedicated space for phototool production, more cleanrooms, and the increased need for quality control, the total investment may not be as different as it seems at first glance. DI systems also come in various configurations with different headcounts to suit different production, capacity, and investment needs.
Moreover, capital investment is only one side of the equation for high-end PCBs. The real question is what the machine can help you earn. DI technology enables the production of more advanced PCBs, resulting in the potential for higher revenue. Additionally, improved yield and reduced defect rates mean less material loss, fewer reworks, and stronger customer satisfaction.
Nevertheless, I would admit that, for simple patterns with low resolution, conventional exposure might be justified.
Productivity
For dry film exposure, DI systems have reached speeds comparable to conventional exposure or even faster, especially with modern resists optimized for DI.
Due to higher energy requirements (and consequently lower productivity), many manufacturers continued using traditional methods for the solder mask exposure.
That is now changing as well. DI machines specifically optimized for solder mask are becoming the new standard. Schmoll introduced a model several years ago designed especially for solder mask applications. While the standard model can perform solder mask exposure, the new configuration can deliver up to 50% higher productivity than the five-head in certain scenarios (depending on energy requirements, panel size, and solder mask type).
Summary
Just as digital photography has replaced film, direct imaging is well on its way to replacing traditional exposure in PCB manufacturing. Key drivers of this transition include:
- Superior accuracy and quality
- Advanced capabilities such as real-time scaling and traceability
- Fewer process steps due to the elimination of phototools
- Higher yields and lower defect rates
- Automation possibilities
The last barrier to complete adoption was solder mask exposure. However, with new machine configurations, this transition is now clearly underway.
This column originally appeared in the June 2025 issue of PCB007 Magazine.
More Columns from Driving Innovation
Driving Innovation: Inner Layer Alignment Methods in PCB ProductionDriving Innovation: Direct Imaging vs. Conventional Exposure
Driving Innovation: Traceability in PCB Production
Driving Innovation: Registration in PCB Production Throughout the Process
Driving Innovation: Schmoll—Decades of Technology Evolution