-
-
News
News Highlights
- Books
Featured Books
- design007 Magazine
Latest Issues
Current IssueLearning to Speak ‘Fab’
Our expert contributors clear up many of the miscommunication problems between PCB designers and their fab and assembly stakeholders. As you will see, a little extra planning early in the design cycle can go a long way toward maintaining open lines of communication with the fab and assembly folks.
Training New Designers
Where will we find the next generation of PCB designers and design engineers? Once we locate them, how will we train and educate them? What will PCB designers of the future need to master to deal with tomorrow’s technology?
The Designer of the Future
Our expert contributors peer into their crystal balls and offer their thoughts on the designers and design engineers of tomorrow, and what their jobs will look like.
- Articles
- Columns
Search Console
- Links
- Media kit
||| MENU - design007 Magazine
Predictive Engineering: Happy Holden Discusses True DFM
October 4, 2017 | Andy Shaughnessy, PCBDesign007Estimated reading time: 2 minutes
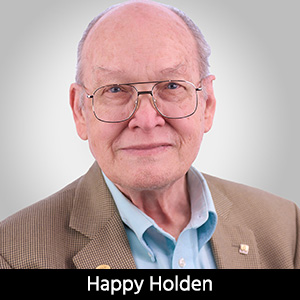
Happy Holden has been involved in DFM for over 45 years, since he first started working at HP and optimized their PCB design and manufacturing processes. Naturally, for this issue, Barry Matties and Andy Shaughnessy made it a priority to get Happy’s thoughts on DFM, and what true DFM entails.
Andy Shaughnessy: Happy, why don’t you start by telling us about your position on DFM, and why true DFM, to you, means that PCB designers and engineers should utilize predictive engineering.
Happy Holden: If you use the term “predictive engineering,” you're not going to get much recognition, because that's a term I use. What most people consider design for manufacturing, or DFX, is software that finds errors in design. Especially in CAM tooling put out by Valor, if a manufacturer puts in his design builds in a minimum, then the DFX software scans through that and finds what’s cautionary and that all requirements are met. That's all done after the fact.
For me, DFM was introduced when HP took up DFM. It was kind of invented by Professors Peter Dewhurst and Geoffrey Boothroyd. Anyway, DFM and DFMA (design for manufacturing and assembly) were really invented by these two American professors in New England. They wrote a book about it, Product Design for Manufacture & Assembly. It later became software.
Their whole philosophy centered on ways to figure out how to do it right the first time. Their book is about the nature of performance during design that allow you to decide if this is going to be easy to assemble. I think the more important component, that Hitachi and the Japanese took it up, was whether the product could be built by automation? That's really significant what Hitachi did with the philosophy. They not only took the ‘do it right the first time’ approach but then asked how they could do it simple enough that robots and automation can build it? The Japanese did this because they wanted to build all these first-generation products in a building next door in Japan and not ship it offshore like Americans were doing.
Contrast that with Apple Inc. Apple designs products that are impossible to automate. They're so complex. They're really fanciful, but they have to be built by human hands. You've got 86,000 17-year-old teenage girls in Shenzhen building these Apple products. Foxconn put up money to install 1 million robots to replace these girls. Today only about 400 robots have been installed out of that 1 million, because they found out the products they're building for the Americans can’t be automated.
I refer to DFM as being designed for manufacturing the first time. We're not just designing it, running software, finding the errors, going back, redesigning it, checking again, going back and re-spinning it, until it works. I'm alone in this definition unless you happen to be knowledgeable about Dewhurst and Boothroyd, which most people in printed circuits aren't.
To read this entire article, which appeared in the September 2017 issue of The PCB Design Magazine, click here.
Suggested Items
Technica USA Celebrates 40 Years of Excellence in Electronics Manufacturing
03/13/2025 | Technica USATechnica USA, a leading provider of materials, equipment, installation, and services for the printed circuit board (PCB) fabrication, PCB Assembly, substrates, MEMS, and semiconductor industries, proudly announces its 40th anniversary in 2025.
TCT Circuit Supply and Electra Polymers Announce New Strategic Partnership
03/12/2025 | Electra Polymers LtdTCT Circuit Supply (TCS) is excited to announce a new strategic partnership with Electra Polymers, a global leader in advanced specialty polymer products
Scanfil Signs Agreement with Leardal Medical for Malaysian Factory
03/12/2025 | ScanfilLaerdal Medical and Scanfil have signed a framework agreement for manufacturing at Scanfil’s newly acquired Malaysian factory in Johor Bahru. Scanfil announced an investment of EUR 4.3 million in the factory in January to meet its high customer demand.
The Test Connection Inc. Promotes Melanie Rutkauskas to Director of Operations for The Training Connection, LLC
03/11/2025 | The Test Connection Inc.The Test Connection Inc. (TTCI), a leading provider of electronic test and manufacturing solutions, is pleased to announce the promotion of Melanie Rutkauskas to Director of Operations for The Training Connection, LLC (TTC-LLC). With her extensive background in operations management, accounting, and customer relations, Melanie brings a wealth of experience and leadership to her new role.
Critical Manufacturing to Show You Might Need a New MES for Making Industry 4.0 A Reality at IPC APEX EXPO 2025
03/10/2025 | Critical ManufacturingCritical Manufacturing, a leader in advanced Manufacturing Execution Systems (MES) and a subsidiary of ASMPT, will show visitors to IPC APEX EXPO 2025 that the company’s MES - complete with extensive features specific to the electronics industry - can serve as a true Industry 4.0 platform. Any electronics manufacturer looking to turn its vision of digital transformation from concept into reality should prioritize visiting Critical Manufacturing at ASMPT SMT Booth 1813.