-
- News
- Books
Featured Books
- smt007 Magazine
Latest Issues
Current IssueSupply Chain Strategies
A successful brand is built on strong customer relationships—anchored by a well-orchestrated supply chain at its core. This month, we look at how managing your supply chain directly influences customer perception.
What's Your Sweet Spot?
Are you in a niche that’s growing or shrinking? Is it time to reassess and refocus? We spotlight companies thriving by redefining or reinforcing their niche. What are their insights?
Moving Forward With Confidence
In this issue, we focus on sales and quoting, workforce training, new IPC leadership in the U.S. and Canada, the effects of tariffs, CFX standards, and much more—all designed to provide perspective as you move through the cloud bank of today's shifting economic market.
- Articles
- Columns
- Links
- Media kit
||| MENU - smt007 Magazine
Solder Preforms 101: Ask the Expert
November 13, 2017 | Patty Goldman, I-Connect007Estimated reading time: 6 minutes
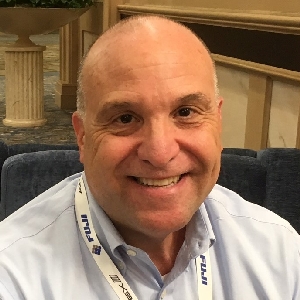
One reason (of many) the SMTA International show is such a wonderful learning experience for me is because it is assembly-focused and I’m a PCB bare board person. When I sat down with Jerry Sidone, from Alpha Assembly Solutions, I learned a great deal about solder preforms, something I barely knew existed before.
Patty Goldman: Jerry, tell me a little bit on your background with Alpha.
Jerry Sidone: I'm a product manager for the engineered materials, which encompasses the solder preform business for Alpha. I'm here to talk about a new solder preform product that we're introducing here at SMTAI; we presented a technical paper on it at the conference. It is a new void reduction solution and it’s a very compelling product that addresses voiding under bottom termination components.
Goldman: I'm a printed circuit board person, and I’m not familiar with solder preforms. What is the purpose of a solder preform?
Sidone: Solder preforms have been used for many years and they are produced in many different shapes and sizes and available in most any solder alloy. One of the most appealing characteristics of solder preforms are they are 100% alloy. Hence, the solder volume is controlled very precisely and consistently wherever they are utilized. Preforms are primarily used to add solder volume wherever solder paste volume is not sufficient.
By far the most popular type of preform in the market today are our standard tape and reel preforms. They're small rectangular preforms, sized to standard chip capacitor packages (i.e., 0201, 0402, 0603, etc.) and packaged in tape and reel format. The advantage of tape and reel preforms is the ease of implementation in any surface mount assembly process. They can be selectively placed anywhere on the board to increase solder volume. They are commonly used to provide 100% hole-fill and to increase solder volume on a surface mount pad.
Goldman: Or if you have a recessed area or something like that? What about flux?
Sidone: Preforms are 100% solder alloy, so they must rely on the flux from the solder paste to generate the activity necessary to solder.
Goldman: Are they always used in conjunction with paste?
Sidone: Not always.
Goldman: But if you were placing them you would have to put them on the paste, wouldn't you? Otherwise they’re not going to stick, right?
Sidone: That's right. In these types of applications, preforms must be placed in the paste. The rule of thumb is to place the preform with a minimum 25% in contact with the solder paste. This will allow them to flow and liquefy within the solder paste to form a reliable solder joint.
Goldman: That's the neat thing about solder, the surface tension pulls things together.
Sidone: At Alpha, we also manufacture fluxed preforms. It allows the preform to stand alone without the need for solder paste or flux paste. Fluxed preforms are offered with a core flux, similar to cored wire or flux coated with a dry rosin flux. The type of fluxed preform used is application dependent. The product that we are introducing today uses a special flux-coated preform to address problematic voiding.
One of the biggest reliability issues in assembly today is voiding under bottom termination components, or BTCs, as they are known in the industry. BTCs are surface mount power management devices that come in leaded and leadless packages. They are identified by the large metalized pad located on the bottom side of the device. The pad is used to both electrically ground and as a thermal heatsink for the device. Excessive voids in the thermal pad’s solder joint causes inefficiencies in heat transfer and can reduce the life of the component.
Goldman: Then your goal is to minimize it, of course.
Sidone: Yes, and this new void reduction solution does just that. A number of documented methods can reduce voids under BTCs. The most common and effective means is printing grid patterns using solder paste. The channels formed in the solder paste provide an escape path for the gases during reflow. The problem our customers have experienced with this sort of solution is the inconsistency in the resultant voids. In the past, inconsistencies have not been an issue when voiding to 25–50% was allowable, but with some of our customers pushing void targets to less than 15% or 10%, inconsistencies in voiding are not acceptable.
Goldman: Is that random, or are there certain variables?
Sidone: Many factors contribute to voiding, including SMT equipment types, solder pastes, component types, reflow profiles and others. Alpha’s solution attempts to minimize the impact from as many factors as possible. We have spent the last couple of years developing our new low void technology, engaging with key customers and component suppliers to identify the primary causes of voiding. The output and result of that work is an effective micro-flux coated preform system that consistently reduces voiding under BTCs. We call it AccuFlux BTC-578 Preform System. It features a special micro-flux coated preform and includes a comprehensive review of the customer’s process. We consider such things as reflow parameters, stencil design, solder paste selection and more to offer the most consistent and effective total void reduction solution.
Goldman: Sounds interesting. What makes your new low-void solution so unique?
Sidone: Our approach is to engage with the customer to identify the appropriate void solution in their application and offer the lowest total cost of ownership. Whether it is one of our low void pastes, preform solutions or a tweak to the customer’s process parameters, we will provide the appropriate solution based on the customer’s requirements.
Goldman: You can advise them.
Sidone: Yes. We can advise them and recommend the best void solution to match their existing process.
Goldman: Now, because they've got many components on their board, suppose there's some that need one type and some that need another. For one component you should do this, and for another one you do that. Do you advise them for every type of component?
Sidone: Typically, there are not more than one or two different types of components so sensitive to voiding on a board. We will recommend the overall best void reduction solution.
Goldman: And you have the data to back it up, which builds confidence for your customers.
Sidone: That's right. That was the key. For instance, we collected over 9,000 data points in our “BTC-578” DOE, not to mention all the preliminary studies that took place prior to selecting the variables for the DOE. A significant amount of data that gives high confidence in our void reduction solution. In fact, we have seen voiding consistently less than 10% or 15% using this new technology in standard reflow atmospheres.
Page 1 of 2
Testimonial
"In a year when every marketing dollar mattered, I chose to keep I-Connect007 in our 2025 plan. Their commitment to high-quality, insightful content aligns with Koh Young’s values and helps readers navigate a changing industry. "
Brent Fischthal - Koh YoungSuggested Items
Indium Promotes Huang to Senior Manager, Marketing Communications
08/28/2025 | Indium CorporationWith its commitment to innovation and growth through employee development, Indium Corporation announces the promotion of Jingya Huang to Senior Manager, Marketing Communications, to continue to lead the company’s branding and promotional efforts.
Rehm Academy Expands Its Training Program
08/28/2025 | Rehm Thermal SystemsThe demands on modern industrial companies and employees continue to rise, and therefore, the topic of further education is becoming increasingly important today.
MacDermid Alpha Awarded for Innovation: Driving Process Optimization and Efficiency with Major Indian EMS Provider
08/28/2025 | MacDermid Alpha Electronics SolutionsMacDermid Alpha Electronics Solutions, a leading global supplier of integrated materials for the electronics industry, is recognized by one of India’s top EMS providers, Syrma SGS, with an award for innovation that advanced process optimization, enhanced operational efficiency, and yield gains.
Integrated Solutions for Board-level Reliability: A Smarter Path Forward
08/27/2025 | Alan Gardner, MacDermid Alpha Electronics SolutionsIn today’s electronics manufacturing landscape, reliability is no longer just a benchmark but a business imperative. As industries such as automotive, aerospace, and high-performance computing (HPC) push the boundaries of innovation, the demand for dependable board-level performance under extreme conditions has never been greater.
ZESTRON Expands Capabilities with Addition of the EPS by i-Tech AG 75 Pallet Cleaning System
08/26/2025 | ZESTRONZESTRON, the global leader in high-precision cleaning solutions and services, is excited to announce the addition of a new capability in its Technical Center in Manassas, VA: