-
- News
- Books
Featured Books
- pcb007 Magazine
Latest Issues
Current IssueInventing the Future with SEL
Two years after launching its state-of-the-art PCB facility, SEL shares lessons in vision, execution, and innovation, plus insights from industry icons and technology leaders shaping the future of PCB fabrication.
Sales: From Pitch to PO
From the first cold call to finally receiving that first purchase order, the July PCB007 Magazine breaks down some critical parts of the sales stack. To up your sales game, read on!
The Hole Truth: Via Integrity in an HDI World
From the drilled hole to registration across multiple sequential lamination cycles, to the quality of your copper plating, via reliability in an HDI world is becoming an ever-greater challenge. This month we look at “The Hole Truth,” from creating the “perfect” via to how you can assure via quality and reliability, the first time, every time.
- Articles
- Columns
- Links
- Media kit
||| MENU - pcb007 Magazine
Flex Time: Why is Rigid-Flex So Expensive?
July 11, 2018 | Bob Burns, PRINTED CIRCUITSEstimated reading time: 1 minute
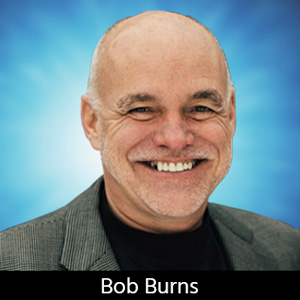
One question that I hear fairly often, particularly after an initial quotation, is “Why is rigid-flex so expensive?” In this article, I’ll share with you the cost drivers in rigid-flex relative to standard rigid boards and flex circuits with stiffeners. A typical rigid-flex PWB will cost about seven times the cost of the same design on a hard board, and two to three times an equivalent flex circuit with stiffeners. A good way to estimate the cost of rigid-flex board in low-level production quantities is 35 to 40 cents per square inch, per layer. So, if you have an eightlayer board that measures 4” x 6”, your costing would look like this:
8 layers x 4” x 6” x $0.40/sq.in. = $ 76.80 each
Again, this applies only to low level production quantities. This is a helpful calculation for getting a quick, rough idea of what your part might cost as a rigid-flex. Rigid-flex PWBs cost quite a bit more, primarily because of the higher cost of the raw materials we use to build them, relative to standard rigid boards or even flex boards. The number one cost driver is the no-flow prepreg. Rigid-flex manufacturers have to use no-flow, or sometimes low-flow prepreg, so that the resin does not flow out onto the flexible areas of the board. No-flow prepregs are designed to offer just enough flow to fill the circuits in the hardboard areas, but not enough to flow out onto the flexible areas of the boards.
No-flow and low-flow prepregs run from $1.50 to $3 per square foot. Conventional rigid board high-flow prepregs run around $.25 per square foot, so there is a large differential in price just for the prepreg. A couple of other things contribute to the cost as well. No-flow prepreg is only available in 1080 and 106 glass cloth styles, which typically press out at .0025” and .002” respectively, so they are thin. Rigid-flex manufacturers don’t have 2113, 2116, 7628 glass styles available to manufacture your board. It is wise to use two plies of prepreg between layers within your construction. The no-flow resin resists flowing, so to assure adequate fill, we use two plies of prepreg between each layer.
To read the full version of this article which appeared in the April 2018 issue of Flex007 Magazine, click here.
Testimonial
"We’re proud to call I-Connect007 a trusted partner. Their innovative approach and industry insight made our podcast collaboration a success by connecting us with the right audience and delivering real results."
Julia McCaffrey - NCAB GroupSuggested Items
I-Connect007 Editor’s Choice: Five Must-Reads for the Week
08/15/2025 | Marcy LaRont, I-Connect007In our industry, my top reads include Prashant Patel’s overview and argument for reshoring, which I found to be a great general overview and breakdown. In further support of the onshoring/reshoring message, I’m highlighting Nolan Johnson’s interview on the survey and report by the Reshoring Initiative. Check out my interview with USPAE’s Jim Will on the state of the flat panel display (FPD) industry and the risks associated with it for U.S. defense and critical infrastructure products.
Global Electronics Industry Remains Under Pressure from Rising Costs
08/04/2025 | Global Electronics AssociationThe global electronics manufacturing supply chain remains under pressure from rising costs, with 61% of firms reporting higher material costs and 54% noting increased labor expenses. according to the Global Electronics Association’s Sentiment of the Global Electronics Manufacturing Supply Chain Report.
Statement from the Global Electronics Association on the July 2025 Tariff on Copper Foil and Electronics-Grade Copper Inputs
07/31/2025 | Global Electronics AssociationWe are disappointed by today’s decision to impose a 50% tariff on imported copper foil and other essential materials critical to electronics manufacturing in the United States.
Direct Metallization: A Sustainable Shift in PCB Fabrication
07/31/2025 | Jim Watkowski, Harry Yang, and Mark Edwards, MacDermid Alpha Electronics SolutionsThe global electronics industry is undergoing a significant transformation, driven by the need for more resilient supply chains and environmentally sustainable manufacturing practices. Printed circuit boards (PCBs), the backbone of interconnection for electronic devices, are at the center of this shift. Traditionally, PCB fabrication has relied heavily on electroless copper, a process that, while effective, is resource-intensive and environmentally hazardous. In response, many manufacturers are turning to direct metallization technologies as a cleaner, more efficient alternative.
Considering the Future of Impending Copper Tariffs
07/30/2025 | I-Connect007 Editorial TeamThe Global Electronics Association is alerting industry members that a potential 50% tariff on copper could hit U.S. electronics manufacturers where it hurts.