-
-
News
News Highlights
- Books
Featured Books
- pcb007 Magazine
Latest Issues
Current IssueSales: From Pitch to PO
From the first cold call to finally receiving that first purchase order, the July PCB007 Magazine breaks down some critical parts of the sales stack. To up your sales game, read on!
The Hole Truth: Via Integrity in an HDI World
From the drilled hole to registration across multiple sequential lamination cycles, to the quality of your copper plating, via reliability in an HDI world is becoming an ever-greater challenge. This month we look at “The Hole Truth,” from creating the “perfect” via to how you can assure via quality and reliability, the first time, every time.
In Pursuit of Perfection: Defect Reduction
For bare PCB board fabrication, defect reduction is a critical aspect of a company's bottom line profitability. In this issue, we examine how imaging, etching, and plating processes can provide information and insight into reducing defects and increasing yields.
- Articles
- Columns
- Links
- Media kit
||| MENU - pcb007 Magazine
PCBs Are Moisture-Sensitive Devices
September 7, 2018 | Richard Heimsch, SUPER DRYEstimated reading time: 3 minutes
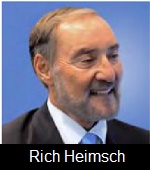
Guidelines for the proper storage, handling and moisture protection of electronic components can be found in the standards IPC/JEDEC J-STD-033C. Though these date back to 1999, there were no published standards for storage and moisture protection for printed boards until 2010, and their proper handling is still often overlooked. But with the correct storage control and the use of suitable drying methods, considerable manufacturing advantages can be gained: PCBs will remain solderable for much longer and damage during reflow due to moisture can be eliminated.
Historically, the printed board industry relied on military specifications and guidelines to define the packaging methods used to preserve the quality and reliability of PCBs during shipment and storage. Over time, of course, many of these documents became obsolete, were found to be incomplete, didn’t address leadfree assembly, or did not provide guidance for newer laminates or final finishes. Additionally, the proliferation of alternative final finishes has produced concerns and requirements for printed board packaging and handling to preserve the finish and assure good solderability.
For instance, IPC-1601A (2016 revision) Printed Board Handling and Storage Guidelines, states: “Baking is not recommended for OSP coatings, as it deteriorates the OSP finish. If baking is deemed necessary, the use of the lowest possible temperature and dwell time is suggested as a starting point.”
Organic solderability preservative (OSP) coatings are among the leading surface finish options in lead-free soldering because they provide an attractive combination of solderability, ease of processing and low cost. Compared to alternatives, however, they tend to be the most prone to oxidation. The cause for this lies in the pure copper surface protected only by the OSP coating layer. Under normal climatic conditions in a manufacturing process, after only a few minutes there will be a separation of a water film at the surface (3-5 atom layers). This then starts a diffusion process which leads to a vapor pressure balance through the OSP coat. Baking also accelerates solid diffusion between metals and increases intermetallic growth. This can lead to a “weak knee” or other solderability issues if the intermetallic layer reaches the surface and oxidizes. Effects upon other finishes (immersion tin, immersion silver, ENIG) are further detailed in the guidelines.
IPC-1601A (2016 revision) also states: “If process controls are ineffective, and printed boards have absorbed excessive moisture, baking is the most practical remedy.” It goes on to state, “However, baking not only increases cost and cycle time, it can also degrade solderability of the printed board which requires extra handling and increases the likelihood of handling damage or contamination. In general, both the printed board fabricator and the user should strive to avoid baking by practicing effective handling, packaging, storage, and process controls…”
In addition to moisture management at key steps in the fabrication process, IPC-1601A also makes clear that boards should be protectively packaged to limit their exposure to ambient humidity during processing and storage. And, importantly, packaged only after determining that their moisture content is below the maximum acceptable moisture content (MAMC) level, which is typically between 0.1% and 0.5% moisture weight to resin weight. Just as with components, 125°C baking temperatures degrade the solderability of PCBs. IPC-1601A warns that as little as 4-6 hours at that temperature can render HASL finished boards unsolderable. Over the decades that passed since the J-STD-033 standard was created, new technologies were developed and proven to safely reset component floor life using low temperatures and ultra-low humidity without requiring extensive time. These 4060°C and <1% methods were first adopted in Europe, and their recognition and use has now spread to North America.
To read the full version of this article which originally appeared in the August 2018 issue of PCB007 Magazine, click here.
Testimonial
"Our marketing partnership with I-Connect007 is already delivering. Just a day after our press release went live, we received a direct inquiry about our updated products!"
Rachael Temple - AlltematedSuggested Items
Statement from the Global Electronics Association on the July 2025 Tariff on Copper Foil and Electronics-Grade Copper Inputs
07/31/2025 | Global Electronics AssociationWe are disappointed by today’s decision to impose a 50% tariff on imported copper foil and other essential materials critical to electronics manufacturing in the United States.
Considering the Future of Impending Copper Tariffs
07/30/2025 | I-Connect007 Editorial TeamThe Global Electronics Association is alerting industry members that a potential 50% tariff on copper could hit U.S. electronics manufacturers where it hurts.
Connect the Dots: Sequential Lamination in HDI PCB Manufacturing
07/31/2025 | Matt Stevenson -- Column: Connect the DotsAs HDI technology becomes mainstream in high-speed and miniaturized electronics, understanding the PCB manufacturing process can help PCB design engineers create successful, cost-effective designs using advanced technologies. Designs that incorporate blind and buried vias, boards with space constraints, sensitive signal integrity requirements, or internal heat dissipation concerns are often candidates for HDI technology and usually require sequential lamination to satisfy the requirements.
OKI Launches Rigid-Flex PCBs with Embedded Copper Coins Featuring Improved Heat Dissipation for Space Equipment Applications
07/29/2025 | BUSINESS WIREOKI Circuit Technology, the OKI Group’s printed circuit board (PCB) business company, has developed rigid-flex PCBs with embedded copper coins that offer improved heat dissipation for use in rockets and satellite-mounted equipment operating in vacuum environments.
Designers Notebook: Basic PCB Planning Criteria—Establishing Design Constraints
07/22/2025 | Vern Solberg -- Column: Designer's NotebookPrinted circuit board development flows more smoothly when all critical issues are predefined and understood from the start. As a basic planning strategy, the designer must first consider the product performance criteria, then determine the specific industry standards or specifications that the product must meet. Planning also includes a review of all significant issues that may affect the product’s manufacture, performance, reliability, overall quality, and safety.