New ‘Blue-Green’ Solution for Recycling World’s Batteries
April 12, 2019 | Rice UniversityEstimated reading time: 4 minutes
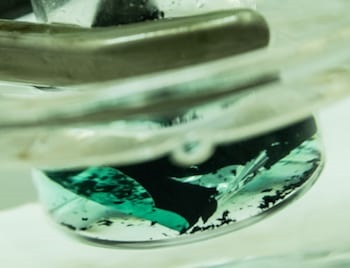
Rice University researchers literally have a solution to deal with the glut of used lithium-ion batteries left behind by the ever-increasing demand for electric vehicles, cellphones and other electronic devices.
A solution turns green as it pulls cobalt from a spent lithium-ion cathode. A Rice University laboratory is developing an environmentally friendly method to recover valuable metals from used batteries. (Photo by Jeff Fitlow/Rice University)
The Rice lab of materials scientist Pulickel Ajayan used an environmentally friendly deep eutectic solvent to extract valuable elements from the metal oxides commonly used as cathodes in lithium-ion batteries. The goal, researchers said, is to curtail the use of harsh processes to recycle batteries and keep them out of landfills.
The solvent, made of commodity products choline chloride and ethylene glycol, extracted more than 90% of cobalt from powdered compounds, and a smaller but still significant amount from used batteries.
“Rechargeable battery waste, particularly from lithium-ion batteries, will become an increasingly menacing environmental challenge in the future as the demand for these through their usage in electric vehicles and other gadgets increases dramatically,” Ajayan said.
“It’s important to recover strategic metals like cobalt that are limited in supply and are critical for the performance of these energy-storage devices,” he said. “Something to learn from our present situation with plastics is that it is the right time to have a comprehensive strategy for recycling the growing volume of battery waste.
“This has been attempted before with acids,” said Rice graduate student and lead author Kimmai Tran. “They’re effective, but they’re corrosive and not eco-friendly. As a whole, recycling lithium-ion batteries is typically expensive and a risk to workers.”Other processes also have drawbacks, she said. Pyrometallurgy involves crushing and mixing at extreme temperatures, and the harmful fumes require scrubbing. Hydrometallurgy requires caustic chemicals, while other “green” solvents that extract metal ions often require additional agents or high-temperature processes to fully capture them.
“The nice thing about this deep eutectic solvent is that it can dissolve a wide variety of metal oxides,” Tran said. “It’s literally made of a chicken feed additive and a common plastic precursor that, when mixed together at room temperature, form a clear, relatively nontoxic solution that has effective solvating properties.”
A deep eutectic solvent is a mixture of two or more compounds that freezes at temperatures much lower than each of its precursors. In that way, she said, one can literally obtain a liquid from a simple combination of solids.
“The large depression of freezing and melting points is due to the hydrogen bonds formed between the different chemicals,” Tran said. “By selecting the right precursors, inexpensive ‘green’ solvents with interesting properties can be fabricated.”
When Tran joined, the Rice group was already testing a eutectic solution as an electrolyte in next-generation high-temperature supercapacitors.
“We tried to use it in metal oxide supercapacitors, and it was dissolving them,” said Rice research scientist and co-corresponding author Babu Ganguli. “The color of the solution would change.”
Rice University research scientist Babu Ganguli and graduate student Kimmai Tran show test tubes with their eutectic solvent and varying concentrations of cobalt drawn into the solution. They are developing the solvent to extract cobalt and lithium from spent lithium-ion batteries. (Photo by Jeff Fitlow/Rice University)
The eutectic was pulling ions from the supercapacitor’s nickel.
“Our team was discussing this and we soon realized we could use what was thought to be a disadvantage for electrolyte as an advantage for dissolving and recycling spent lithium batteries,” Ganguli said.
That became Tran’s focus, as she tested deep eutectic solvents on metal oxides at different temperatures and time scales. During tests with lithium cobalt oxide powder, the clear solvent yielded a wide spectrum of blue-green colors that indicated the presence of cobalt dissolved within.
At 180 degrees Celsius (356 degrees Fahrenheit), the solvent extracted nearly 90% of lithium ions, and up to 99% of cobalt ions from the powder when certain conditions were satisfied.
The researchers built small prototype batteries and cycled them 300 times before exposing the electrodes to the same conditions. The solvent proved adept at dissolving the cobalt and lithium while separating the metal oxides from the other compounds present in the electrode.
The blue-green color of solutions reveals the presence of cobalt taken from spent lithium-ion batteries through a new process developed at Rice University. (Photo by Jeff Fitlow/Rice University)
They found that cobalt could be recovered from the eutectic solution through precipitation or even electroplating to a steel mesh, as this latter method potentially allowed for the deep eutectic solvent itself to be reused.
“We focused on cobalt,” said Rice alumnus Marco Rodrigues, now a postdoctoral researcher at Argonne National Laboratory. “From a resource standpoint, it’s the most critical part. The battery in your phone will surely have lots of it. Lithium is very valuable too, but cobalt in particular is not only environmentally scarce but also, from a social standpoint, hard to get.”He noted the Department of Energy is mounting new efforts to advance battery recycling technologies and recently announced a center for Li-ion battery recycling.
The path forward will require continued efforts.
“It’s likely we won’t be able to recycle and replace mining completely,” Tran said. “These technologies are relatively new, and there is a lot of optimization that needs to be done, such as exploring other deep eutectic solvents, but we truly believe in the potential for greener ways to do dirty chemistry. Sustainability is in the heart of the work I do and what I want to do for the rest of my career.”
Graduate student Keiko Kato is a co-author of the paper. Ajayan is the Benjamin M. and Mary Greenwood Anderson Professor in Engineering and a professor of chemistry.
The National Science Foundation supported the research through its Graduate Research Fellowship Program.
Testimonial
"Our marketing partnership with I-Connect007 is already delivering. Just a day after our press release went live, we received a direct inquiry about our updated products!"
Rachael Temple - AlltematedSuggested Items
Curtiss-Wright Selected by Rheinmetall to Provide Turret Drive Stabilization System for the KF51 Panther Main Battle Tank
08/11/2025 | BUSINESS WIRECurtiss-Wright announced it has been selected by Rheinmetall Landsysteme Germany (RLS) to provide its modular turret drive stabilization system (TDSS) technology in support of the KF51 Panther Main Battle Tank (MBT).
European Global Mobile Artillery Rocket System Launcher Proves Capability with First-Ever Firing
08/04/2025 | Lockheed MartinLockheed Martin and Rheinmetall, partners in the Global Mobile Artillery Rocket System (GMARS) program, successfully conducted the first live fire of the GMARS launcher, demonstrating its capability to launch GMLRS rockets.
Rheinmetall Expands Local Production Activities in Romania
07/28/2025 | RheinmetallRheinmetall has established a comprehensive local production network in Romania, encompassing both its own companies in the country and new partnerships with Romanian companies.
STMicroelectronics, Metalenz Sign a New License Agreement to Accelerate Metasurface Optics Adoption
07/14/2025 | STMicroelectronicsSTMicroelectronics, a global semiconductor leader serving customers across the spectrum of electronics applications and Metalenz, the pioneer of metasurface optics, announced a new license agreement.
Happy’s Tech Talk #40: Factors in PTH Reliability—Hole Voids
07/09/2025 | Happy Holden -- Column: Happy’s Tech TalkWhen we consider via reliability, the major contributing factors are typically processing deviations. These can be subtle and not always visible. One particularly insightful column was by Mike Carano, “Causes of Plating Voids, Pre-electroless Copper,” where he outlined some of the possible causes of hole defects for both plated through-hole (PTH) and blind vias.