-
- News
- Books
Featured Books
- pcb007 Magazine
Latest Issues
Current IssueInventing the Future with SEL
Two years after launching its state-of-the-art PCB facility, SEL shares lessons in vision, execution, and innovation, plus insights from industry icons and technology leaders shaping the future of PCB fabrication.
Sales: From Pitch to PO
From the first cold call to finally receiving that first purchase order, the July PCB007 Magazine breaks down some critical parts of the sales stack. To up your sales game, read on!
The Hole Truth: Via Integrity in an HDI World
From the drilled hole to registration across multiple sequential lamination cycles, to the quality of your copper plating, via reliability in an HDI world is becoming an ever-greater challenge. This month we look at “The Hole Truth,” from creating the “perfect” via to how you can assure via quality and reliability, the first time, every time.
- Articles
- Columns
- Links
- Media kit
||| MENU - pcb007 Magazine
Estimated reading time: 5 minutes
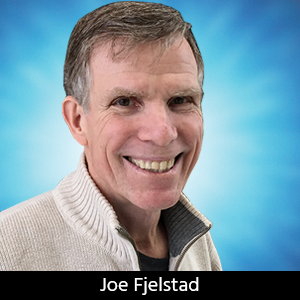
Flexible Thinking: How to Get From Here to There
"One day Alice came to a fork in the road and saw a Cheshire cat in a tree. 'Which road do I take?' she asked. 'Where do you want to go?' was his response. 'I don't know,' Alice answered. 'Then,' said the cat, 'it doesn't matter."
—Lewis Carroll, author of Alice’s Adventures in Wonderland
Lewis Carroll is said to have written Alice’s Adventures in Wonderland originally for the entertainment of the seven-year-old daughter of a family friend named Alice Liddell. While it has since delighted countless children (and adults, I am certain) with the imaginative and fanciful world it presents since it was first published, the book is also full of playfully thoughtful dialogue that often seems to have meaning deeper than the humorous exchanges belie.
The quoted excerpt includes one such exchange, and it is an instructive life lesson for all who read and take it in fully. To begin the process, you must first know where you are going. This is true for any project or life pursuit, I believe, and I often try to bring it to mind as I start any new project. With respect to developing products that might benefit from flexible circuit technology, this is no less true.
From Concept to Product
In my book Flexible Circuit Technology, 4th Edition, I mapped out a number of steps for getting from concept to product using flexible circuits in “Chapter 6: Implementing Flexible Circuit Technology.” The pathway was not paved in stone because the evolution of flexible circuit technology is ongoing, and new materials, processes, and processing equipment continue to come online, opening the doors to new opportunities and prospective ways of getting the job done. However, the basics of the process remain the same. So, here in brief are some of the process touchstones that I think are important.
First, there is the product concept. What specific design should be used for elements of the product that make flexible circuits attractive? This question needs to be asked to make sure that flexible circuit technology is truly required for the product. Because the thinness of the circuit is frequently an objective, flexible circuits are usually tapped to provide the sought-after benefit. However, sometimes—even often—a thin reinforced laminate circuit will suffice, and typically, at a lower cost. Thus, do a quick reality check; there is no need to make a product more expensive than necessary.
Second, flexible circuits have the obvious ability to interconnect electronic elements (e.g., modules, displays, connectors, etc.) that are distal from one another, commonly in three-dimensional space. Moreover, these electronic elements may be required to move relative to each other when in use (e.g., disk drives, read-write heads, printer cables, etc.) or during maintenance or upgrading of a system to facilitate access to the elements of interest. Understanding the mechanical requirements associated with this movement will influence design choices, including the type of materials used and the type and weight of metal foil (most frequently rolled annealed copper).
In addition, there are many seemingly insignificant details (e.g., copper foil grain direction) that need to be addressed to ensure that the product will perform to expectations for the duration of its anticipated lifetime. The type and thickness of the cover-layer used in the circuit also plays into this equation as well as the objective of keeping the copper foil at the center of the construction, especially in areas designed for bending or flexing. The first topic is somewhat macro, and the second is a bit more micro and nuanced, but both topics are germane to this subject.
Designing Flex Right the First Time
Circling back to the bigger, yet often overlooked, items associated with the process of getting a flex circuit designed right the first time, there is a need to consider the operating environment for the end product. For example, consider the temperature excursion range and humidity expectations over its life and use as well as the processes that will be used in its fabrication. These factors will impact and likely limit the choices of materials used. Solder remains a commonly used method for assembly. And with higher temperature lead-free solders in use today, it is necessary to choose a material that will stand up to requirements.
Another matter to consider relative to field use is the mechanical stresses and strains that may be encountered by the product. Designers use flex with great frequency in dynamic applications, such as those mentioned earlier (e.g., disc drives read/write heads, printer cables, etc.), and they pay special attention to the circuit features that pass through the dynamic bend areas of the design.
However, products that are deemed to be non-dynamic applications can and sometimes do fail due to copper fatigue failure as a result of shock and vibration endured in a field application. These are not the visible flexural cycles that can be seen with the unaided eye, but microscopic flexural cycles that are characteristic of vibration. While in the former case, the cycles tend to be high amplitude and moderately low frequency, in the latter case, the frequency tends to be high and the amplitude low. I have seen such failures and heard of others over the years.
Conclusion
The intent of this column was to make you aware of some of the issues that need to be considered as you navigate the waters that stretch between product conception and manufacture using flexible circuit technology. Flexible circuits are a very attractive interconnection technology, but you must be attentive to the many factors that can spell the difference between success and failure.
In closing, I invite you to download a free copy of Flexible Circuit Technology, 4th Edition to fill in more of the detail needed to make the journey. The book can be found and downloaded at flexiblecircuittechnology.com.
Joe Fjelstad is founder and CEO of Verdant Electronics and an international authority and innovator in the field of electronic interconnection and packaging technologies with more than 150 patents issued or pending.
This column was originally published in the April 2019 issue of Flex007 Magazine.
More Columns from Flexible Thinking
Flexible Thinking: The Key to a Successful Flex Circuit Design TransferFlexible Thinking: Flexible Circuit Technology—Looking Back and Forward
Flexible Thinking: Mind-tapping into January
Flexible Thinking: Another PCB Design Paradigm Shift in the Works
Flexible Thinking: Rules of Thumb—A Word to the Wise
Flexible Thinking: Musings on High Density Interconnections
Flexible Thinking: Integrated Passive Devices—Design Solutions With Many Benefits
Flexible Thinking: Mechatronics in a Flex World