-
- News
- Books
Featured Books
- pcb007 Magazine
Latest Issues
Current IssueInventing the Future with SEL
Two years after launching its state-of-the-art PCB facility, SEL shares lessons in vision, execution, and innovation, plus insights from industry icons and technology leaders shaping the future of PCB fabrication.
Sales: From Pitch to PO
From the first cold call to finally receiving that first purchase order, the July PCB007 Magazine breaks down some critical parts of the sales stack. To up your sales game, read on!
The Hole Truth: Via Integrity in an HDI World
From the drilled hole to registration across multiple sequential lamination cycles, to the quality of your copper plating, via reliability in an HDI world is becoming an ever-greater challenge. This month we look at “The Hole Truth,” from creating the “perfect” via to how you can assure via quality and reliability, the first time, every time.
- Articles
- Columns
- Links
- Media kit
||| MENU - pcb007 Magazine
Estimated reading time: 3 minutes
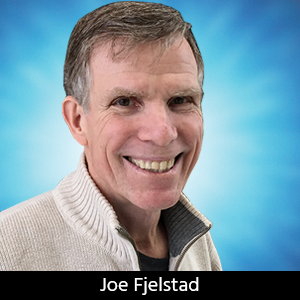
Flexible Thinking: Integrated Passive Devices—Design Solutions With Many Benefits
Many good ideas have often escaped broader appreciation in the electronics industry. Some have come in and out of favor over time, including the integrated passive device (IPD).
The first IPDs appeared in the late 1980s and early ’90s, driven by a desire to miniaturize electronics while decreasing cost and increasing performance. Those drivers remain key today. Just like an IC package, engineers integrate resistors, capacitors, inductors, etc., into a packaged device, and then mount and interconnect them to a printed circuit board. This can significantly reduce the number of discrete components that might otherwise be required for an assembly design, and using an IPD can simplify PCB assembly processes and lower assembly and final product costs.
This IC-like manufacturing process would involve depositing thin layers of resistive, dielectric, and conductive materials onto a suitable substrate (often silicon, glass, or ceramic) using physical vapor deposition (PVD) or chemical vapor deposition (CVD). However, it is also possible to assemble an IPD discrete device using a traditional SMT process and solder to mount the resistors, capacitors, and inductors to a small PCB or ceramic circuit that has terminations at designated locations (Figure 1).
Other benefits of IPDs include:
- Miniaturization: To shrink the size of products, designers have occasionally used IPDs to save space on printed circuit boards to replace myriad discrete passive devices.
- Performance improvement: Integration of passives into packages can reduce the parasitic effects that often occur in some designs and can lead to better electrical assembly performance.
- Enhanced reliability: The integrated passive component can be manufactured and assembled using fewer solder joints and interconnections, resulting in more reliable electronic designs. (This is something that has not gone unnoticed by me and is now considered an opportunity for exploration using the Occam Process for their manufacture.)
With the benefits just accounted for, it should not be too surprising that integrated passive devices have found some reasonably broad acceptance. For example, when one attempts to establish where IPDs have found greatest acceptance, it’s almost everywhere. Today, IPDs are widely used in various applications, including RF modules, wireless communication devices, medical devices, automotive electronics, and consumer electronics. One highlightable benefit of IPDs is their ability to enhance performance while saving space, making them suitable for high-frequency and high-performance application. However, in broad brushstrokes, the following are a few more specific places where they have provided benefits.
In consumer electronics, such as smartphones, tablets, and wearables, the adoption of IPDs has reportedly been quite high due to the stringent space and performance requirements as discussed earlier. One estimate has it that perhaps 70% of modern consumer electronic designs in recent years have incorporated some form of IPD.
As new cars continue to consume evermore electronics, the automotive industry has demonstrated significant interest in the adoption of IPDs, particularly in advanced driver-assistance systems, infotainment systems, and power management modules to name just a few. Estimates of adoption rates in automotive are similar to that of consumer electronics. In telecommunications equipment, especially for RF and high-frequency applications (think 5G), IPDs are widely used to enhance performance and reliability. With a solid foothold, it is likely they will continue their march into coming generations of products. The same holds true for medical and industrial products, and the list goes on.
When it comes to suppliers, a long list includes familiar names such as Vishay, AVX, Murata, Texas Instruments, Johanson Technology, OnChip Devices, and STMicroelectronics. They offer a wide range of passive electronic components, including resistors, capacitors, inductors, and integrated passive components, with off-the-shelf and custom solutions to meet specific design needs.
Integrated passive devices offer designers an opportunity to significantly reduce their designs' complexity while improving performance and reliability. I encourage you to learn more about them.
Joe Fjelstad is founder and CEO of Verdant Electronics and an international authority and innovator in the field of electronic interconnection and packaging technologies with more than 185 patents issued or pending. To read past columns or contact Fjelstad, click here. Download your free copy of Fjelstad’s book Flexible Circuit Technology, 4th Edition, and watch his in-depth workshop series “Flexible Circuit Technology.”
This column originally appeared in the August 2024 issue of Design007 Magazine.
More Columns from Flexible Thinking
Flexible Thinking: The Key to a Successful Flex Circuit Design TransferFlexible Thinking: Flexible Circuit Technology—Looking Back and Forward
Flexible Thinking: Mind-tapping into January
Flexible Thinking: Another PCB Design Paradigm Shift in the Works
Flexible Thinking: Rules of Thumb—A Word to the Wise
Flexible Thinking: Musings on High Density Interconnections
Flexible Thinking: Mechatronics in a Flex World
Flexible Thinking: PCB Designers Still Wanted