-
- News
- Books
Featured Books
- smt007 Magazine
Latest Issues
Current IssueTechnical Resources
Key industry organizations–all with knowledge sharing as a part of their mission–share their technical repositories in this issue of SMT007 Magazine. Where can you find information critical to your work? Odds are, right here.
The Path Ahead
What are you paying the most attention to as we enter 2025? Find out what we learned when we asked that question. Join us as we explore five main themes in the new year.
Soldering Technologies
Soldering is the heartbeat of assembly, and new developments are taking place to match the rest of the innovation in electronics. There are tried-and-true technologies for soldering. But new challenges in packaging, materials, and sustainability may be putting this key step in flux.
- Articles
- Columns
Search Console
- Links
- Media kit
||| MENU - smt007 Magazine
How Do I Get Smart With IPC CFX? (Part 2)
July 31, 2019 | Michael Ford, Aegis Software Corp.Estimated reading time: 10 minutes
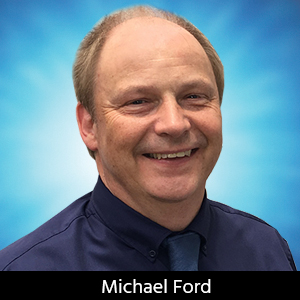
In Part 1, Michael Ford described automation in the SMT assembly industry and where CFX fits in. In Part 2, Ford looks at the CFX adoption, the values and challenges of digitalization with CFX, and the scope of CFX utilization.
CFX Adoption
Historically, as well as the lack of defined data content, legacy communication standards within assembly manufacturing failed to become widely adopted due to related costs and difficulties to implement. In the case of CFX, a free, open-source software development kit (SDK) is available to anyone who would like to fast-track support of CFX into their machines or IT solutions. The CFX SDK is available through the GitHub source-code sharing site and comes with full documentation covering messages and data structures. This can be freely incorporated into commercial applications, including machines, bespoke processes—such as functional test equipment—as well as various manufacturing solutions.
Though it is expected that there will be a wide range of adoption of CFX by mainstream equipment vendors, there will be cases where older machines will remain unsupported without native CFX support. In these cases, CFX capability can be provided through the use of a simple, inexpensive add-on box, which could contain a Raspberry Pi computer with any required inputs and outputs to gather and deliver data between the machine and the CFX environment, for example. Customization of the software within the add-on box is likely depending on the machine to which it is being applied.
Values and Challenges of Digitalization With CFX
The challenges of factory digitalization, in line with expectations of smart factory or Industry 4.0, are almost completely removed with the adoption of CFX. In terms of the manufacturing business, requirements for data needed for critical decision-making support needed for fully flexible factory operations are fully met through the specific information definition and timing of CFX messages. Innovation towards smart factory solutions can finally begin on a practical basis.
CFX is sustainable since it affords the same opportunity for machine vendors to create their own added-value solutions and values through the use of CFX data derived from other machines and processes. The ability for machine vendors to generate product enhancement and create additional revenue streams adds to their benefit from CFX of the elimination of costs to create and support bespoke interfaces for customers. IT teams and solution providers also benefit significantly, as the cost of data acquisition becomes a mere fraction of what it once was. In addition, the data has better quality, detail, and consistency, and is capable of supporting further smart solutions and Industry 4.0 innovation.
Scope of CFX Utilization
There are as many potential values from the use of CFX data as there are ideas for smart functions in assembly factories. The scope of CFX has been defined to include support for all known and existing software functions as well as those expected in the future. There are three layers of information exchange within the typical assembly factory. CFX is designed to support all three, including the connection of each layer.
Figure 4: Examples of CFX message transfer.
Each of the three layers shown in Figure 4 provides information through CFX as well as utilizing data from other layers and processes. CFX creates the “big data” environment in assembly manufacturing. The following four examples are each based on a different flow of CFX messages.
1. CFX Machine-to-Machine, Closed-loop Application
The principle of a “closed-loop” is that the analysis of the output of a process is used to modify the input and operational parameters used throughout the process. There are several ways of applying closed-loops on an SMT manufacturing line with many examples having been developed. Unfortunately, these legacy examples rely on bespoke machine connections that have been set up with extensive work and testing and only work with specific combinations of machines with specific software versions. With CFX, as long as each machine supports CFX, the connection of advanced closed-loops is as simple as “plug and play.”
The closed-loop application may be provided by any one of the machine vendors in the line, a third-party software, or even a combination. Figure 5 shows an example of a more complex closed-loop line.
Figure 5: CFX machine-to-machine, closed-loop example application.
The sequence of steps performed is as follows:
- Each uniquely identified PCB flows in from the left
- The screen-printing operation is performed
- The paste inspection operation is performed
- Data from the paste inspection (1) is analyzed to find deviations between the specified printing position as determined by the engineering data and the actual measured position
- Following analysis, a correction parameter (2) is sent to the screen printer to compensate for the printing deviation such that the next PCBs should not have any deviation
- In addition, a compensation factor parameter (2) is sent to the SMT placement machine such that placements on the specific production unit analyzed will not be affected by the printing deviation that already occurred; this compensation factor is also fed to the optical inspection machine so that the compensation applied by SMT is not reported as an error
- The optical inspection machine, bearing in mind the placement compensation, will also measure any deviation in the placements (3) and feed the data back to the SMT placement machine
- The SMT placement machine can analyze the data from the automated inspection machine to determine any root causes—for example, whether deviations are simple offsets, skews, related to a nozzle, head or feeder, etc.—such that corrective action can be suggested back to the SMT placement machine operator
The effect of such closed-loop operations, looking at historical examples, have resulted in an order of magnitude improvement in first-pass yield together with associated reduction of losses in productivity and quality.
Page 1 of 2
Suggested Items
Altus Group Strengthens Industry Connections at Southern Manufacturing & Electronics 2025
02/11/2025 | Altus GroupAltus Group, a leading distributor of capital equipment in the UK and Ireland, has concluded another successful year at Southern Manufacturing and Electronics 2025, where the team strengthened relationships with existing customers and engaged with new industry contacts.
The Government Circuit: Four Things to Know About IPC Advocacy in 2025
02/11/2025 | Chris Mitchell -- Column: The Government CircuitAs the calendar turns to mid-February, IPC’s government relations and advocacy work is in full swing around the world. Here are four things to know, big picture, about how we’re approaching the current, very complicated situation.
Lisa Anderson, Supply Chain Expert: The Manufacturing Resurgence is Here – Are You Ready?
02/10/2025 | LMA Consulting Group, Inc.Manufacturing in the U.S. is gaining momentum, and businesses that aren’t prepared will struggle to keep up. According to Lisa Anderson, MBA, CSCP, CLTD, President of LMA Consulting Group, Inc., the resurgence will be fast and powerful, with companies that are ready to scale reaping the greatest benefits.
Husqvarna, Flex Announce Strategic Partnership
02/07/2025 | FlexHusqvarna and Flex announced a strategic manufacturing partnership, which will enable Husqvarna to further enhance flexibility, efficiency, and time to market through Flex's strategic supply chain management solutions and expand Flex's Lifestyle portfolio into outdoor and power equipment.
AIM Solder Acquires the Assets of Canfield Technologies
02/07/2025 | AIM SolderAIM Solder, a leading global manufacturer of solder assembly materials, is pleased to announce the acquisition of the assets of Canfield Technologies, a renowned producer of high-quality solders and fluxes since 1844.