-
-
News
News Highlights
- Books
Featured Books
- smt007 Magazine
Latest Issues
Current IssueSupply Chain Strategies
A successful brand is built on strong customer relationships—anchored by a well-orchestrated supply chain at its core. This month, we look at how managing your supply chain directly influences customer perception.
What's Your Sweet Spot?
Are you in a niche that’s growing or shrinking? Is it time to reassess and refocus? We spotlight companies thriving by redefining or reinforcing their niche. What are their insights?
Moving Forward With Confidence
In this issue, we focus on sales and quoting, workforce training, new IPC leadership in the U.S. and Canada, the effects of tariffs, CFX standards, and much more—all designed to provide perspective as you move through the cloud bank of today's shifting economic market.
- Articles
- Columns
- Links
- Media kit
||| MENU - smt007 Magazine
Automated Conformal Coating of CCAs Using Polyurethane
August 30, 2019 | Marissa Pati and Ana “Lety” Campuzano-Contreras, BAE SystemsEstimated reading time: 3 minutes
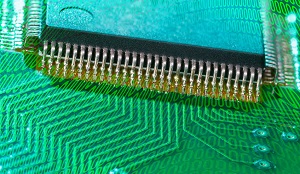
Abstract
The development of an automated circuit card assembly (CCA) conformal coating process using a low-outgassing polyurethane material was essential for meeting the increase in customer demand from 3,000 to 60,000 units per year. Low-outgassing polyurethane conformal coating is used for protection against humidity and tin whisker mitigation.
When increasing production throughput requirements, it is necessary to eliminate variation and increase production capacity by automating processes. Manual processes in manufacturing can lead to defects, increased variability, and additional manufacturing time.
To begin the process improvement of automating spraying a low-outgassing polyurethane conformal coating, several machine and material parameters were considered during the evaluation. A selective conformal coating machine was chosen and the following parameters were determined to be critical to the process: thinner-to-material ratio, atomizing air pressure, material syringe pressure, nozzle distance from the substrate, nozzle speed, material flow rate, number of coats, and curing requirements.
These parameters were verified by performing an adhesion by tape test per ASTM D3359-17 (Standard Test Methods for Rating Adhesion by Tape Test) in addition to verifying conformal coat thickness and defects per J-STD-001 (Joint Industry Standard Requirements for Soldered Electrical and Electronic Assemblies) requirements. Implementing a selective polyurethane conformal coating spraying process has increased capacity capabilities and eliminated variations induced from the manual process.
Background
In the manufacturing of Class 3 circuit card assemblies, conformal coating can be critical to the lifespan of the circuit card. For circuit cards to withstand environmental factors in the field they must be properly protected, which typically requires the use of conformal coating. Polyurethane conformal coating is commonly used throughout the industry, but typically, it is used in lower volume production. Tin whisker mitigation is one of the most common reasons to use a low-outgassing polyurethane material.
Adapting to increases in production can be difficult. An increase in customer demand from 3,000 to 60,000 units per year can create many challenges in a manufacturing environment. Currently, a low-outgassing polyurethane material is applied to the circuit card assemblies via manually spraying using an atomizing handheld air gun. With any manual process, there is significant variation in the outcome due to many variables involved; therefore, the process is difficult to control. This variation may be acceptable in low volume production, but for mass production, this method is unsustainable and unreliable. Automating the process is the best way to achieve zero defects, eliminate variation, and accommodate the strict production schedule.
To develop an automated-spraying process for this polyurethane material, there were many factors that had to be taken into consideration and many variables that required process controls (Figure 1). There are J-STD-001 requirements that must be met; polyurethane conformal coating must be 0.03–0.13mm (0.001–0.005 in.) [1]. No defects per IPCA-610 (Acceptability of Electronic Assemblies) are acceptable. There is also the need to meet the customer and drawing requirements. Additionally, strict material requirements, such as pot life and cure time, needed to be considered. All of these factors played a major role in automating the manual hand-spray process, and it was necessary to understand all of the material requirements and restrictions, customer requirements, and IPC requirements before beginning the evaluation of equipment and development of the process.
The entire conformal coating process was evaluated during this experiment, which includes more than just the spraying of polyurethane material onto the circuit cards. The first step of the process is the preparation of circuit card assemblies, which includes cleaning, baking, and masking any areas that are required to be free of conformal coating per the customer drawing requirements. The coating process also includes preparation of the material used for spraying; this may be a mixture of two or more parts that must be weighed and mixed properly. The next step is the spraying and curing of the material onto the circuit cards and coupons for thickness measurements. The final steps of the conformal coating process are the removal of the masking materials and touchup of the coating. Preparation of the substrates, correct mixture of the material, proper curing, and accurate thickness measurements are important variables that could affect the output of the conformal coat spraying process. Therefore, it was necessary to ensure proper controls had been established for all of these aspects of the conformal coating process.
To read the full article, which appeared in the August 2019 issue of SMT007 Magazine, click here.
Testimonial
"In a year when every marketing dollar mattered, I chose to keep I-Connect007 in our 2025 plan. Their commitment to high-quality, insightful content aligns with Koh Young’s values and helps readers navigate a changing industry. "
Brent Fischthal - Koh YoungSuggested Items
A.R.T. Ltd. Nominated in Four Categories at 2025 Instrumentation and Electronics Industry Awards
08/11/2025 | A.R.T. Ltd.Advanced Rework Technology Ltd. (A.R.T. Ltd.), a leading provider of electronics training and consultancy, has been shortlisted in four categories at the 2025 Instrumentation and Electronics Industry Awards, including Industry Personality, Academic Support, Rising Star, and Best Customer Service.
EMC Taiwan Receives IPC-4101 Qualified Products Listing Certification
08/08/2025 | Global Electronics AssociationIPC’s Validation Services Program has awarded an IPC-4101 Qualified Products Listing (QPL) to Elite Materials Co. (EMC), an electronics base material manufacturing company headquartered in Taoyuan City, Taiwan.
Global Excellence in PCB Design: The Global Electronics Association Expands to Italy
08/07/2025 | Global Electronics AssociationIn today's rapidly evolving electronics industry, printed circuit boards (PCBs) serve as the critical backbone influencing the success, reliability, and time-to-market of countless products. Recognizing this essential role, the Global Electronics Association (formerly IPC), a worldwide leader in electronics standards, certification, and education, is now expanding its internationally acclaimed PCB design training to Italy.
Dana on Data: Best Practices in Interpreting Drawing Notes—‘Use Latest Revision’
08/07/2025 | Dana Korf -- Column: Dana on DataThe global nature of electronics manufacturing requires clear, consistent, and precise communication, particularly in technical documentation. An area where miscommunication often arises is in interpreting drawing notes—small lines of text with the potential to dramatically impact product quality, manufacturing efficiency, and customer satisfaction.
Creating Connections in Mexico
07/30/2025 | Michelle Te, Community MagazineA concerted effort by the Global Electronics Association—Mexico team over the past year has created inroads for the Global Electronics Association (formerly IPC) with leading electronics companies, government offices, and academic institutions in Mexico. “Our goal is to bring more awareness to what the Global Electronics Association is and what it offers,” says Lorena Villanueva, senior director. “We also aim to increase our membership. Of 3,200 members of the Global Electronics Association, only 180 are in Mexico.”