-
-
News
News Highlights
- Books
Featured Books
- pcb007 Magazine
Latest Issues
Current IssueThe Hole Truth: Via Integrity in an HDI World
From the drilled hole to registration across multiple sequential lamination cycles, to the quality of your copper plating, via reliability in an HDI world is becoming an ever-greater challenge. This month we look at “The Hole Truth,” from creating the “perfect” via to how you can assure via quality and reliability, the first time, every time.
In Pursuit of Perfection: Defect Reduction
For bare PCB board fabrication, defect reduction is a critical aspect of a company's bottom line profitability. In this issue, we examine how imaging, etching, and plating processes can provide information and insight into reducing defects and increasing yields.
Voices of the Industry
We take the pulse of the PCB industry by sharing insights from leading fabricators and suppliers in this month's issue. We've gathered their thoughts on the new U.S. administration, spending, the war in Ukraine, and their most pressing needs. It’s an eye-opening and enlightening look behind the curtain.
- Articles
- Columns
- Links
- Media kit
||| MENU - pcb007 Magazine
Hitachi Chemical DuPont MicroSystems, Ltd.: Regarding the Decision to Maintain Two Japanese Granted Patents on Polyimide Precursor Resin Composition
January 15, 2020 | Business WireEstimated reading time: 1 minute
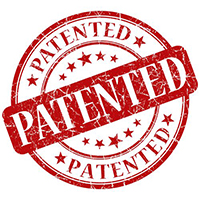
Hitachi Chemical DuPont MicroSystems, Ltd. (hereinafter “the company”) announces that the company was granted permission to maintain the Japanese patents (Patent No. 6288227 and Patent No. 6206446; hereinafter “the patent group”) on polyimide precursor resin composition essential for manufacturing high heat-resistant, bendable flexible substrates on October 11 and November 25, respectively, in 2019 after examination by the Japan Patent Office in response to an opposition to the patent group filed by a third party.
The rapid growth of the Internet of Things (IoT) is expected to further expand the demand for flexible organic EL and Micro-LED display panels with the spread of bendable devices, including next-generation smartphones, e-Paper, and digital signage.
To manufacture flexible panels, plastic substrates are placed on glass substrates, with pixel circuits and display layers formed on top, while forming thin film transistors (TFT), one part of the pixel circuits, requires high temperature processing. However, this process could not be applied to conventional plastic substrates due to their poor heat resistance. Technologies previously used to tackle this problem involved the complicated process of forming TFTs on glass substrates, followed by separating the pixel circuits from the glass substrates and reforming them on plastic substrates. Flexible panel manufacturers had struggled to overcome this challenge for many years.
The company’s technology is related to liquid polyimide precursor resin composition for forming flexible device substrates that gives plastic substrates both toughness* and heat resistance. In addition to heat resistance, this technology offers solutions to realize the conflicting properties of “excellent adhesion to glass substrates while forming pixel circuits” and “easy release from glass substrates after forming pixel circuits,” thereby allowing flexible device substrates to be formed using a simpler and more efficient process.
The company will take full advantage of the patent group to actively promote external collaboration, including out-licensing.
*Material’s high viscosity or resistance to damage caused by external force
Suggested Items
All Flex Solutions Upgrades Lamination Layup
06/22/2025 | All Flex SolutionsAll Flex Solutions has invested in Ulrich Rotte lamination layup stations in their rigid flex layup area. The Ulrich Rotte stations automate the layup process by handling the lamination plates, which are heavy, and sequencing the layup process for the operators.
SEMI FlexTech Solicits Proposals for Advancing the Future of Flexible Hybrid Electronics
06/18/2025 | SEMIFlexTech, a SEMI Technology Community, today issued a Request for Proposals (RFP) to advance flexible hybrid electronics (FHE) technologies, including the development of advanced materials and additive processing.
Roll-to-Roll Technologies for Flexible Devices Set to Grow at 11.5% CAGR
06/11/2025 | GlobeNewswireAccording to the latest study from BCC Research, the “Global Markets for Roll-to-Roll Technologies for Flexible Devices” is expected to reach $69.8 billion by the end of 2029 at a compound annual growth rate (CAGR) of 11.5% from 2024 to 2029.
Global PCB Connections: Rigid-flex and Flexible PCBs—The Backbone of Modern Electronics
05/20/2025 | Jerome Larez -- Column: Global PCB ConnectionsIn the past decade, flex and rigid-flex PCB technology has become the fastest-growing market segment. As an increasing number of PCB companies develop the capabilities to fabricate this technology, PCB designers are becoming comfortable incorporating these designs into their products.
Flexible PCB Market to Reach $61.75B by 2032, Driven by the Demand for Compact Electronics, Automotive and Medical Applications
05/16/2025 | Globe NewswireAccording to the SNS Insider, “The Flexible PCB Market was valued at USD 21.42 billion in 2023 and is expected to reach $61.75 billion by 2032, growing at a CAGR of 12.52% over the forecast period 2024-2032.”