-
- News
- Books
Featured Books
- smt007 Magazine
Latest Issues
Current IssueWhat's Your Sweet Spot?
Are you in a niche that’s growing or shrinking? Is it time to reassess and refocus? We spotlight companies thriving by redefining or reinforcing their niche. What are their insights?
Moving Forward With Confidence
In this issue, we focus on sales and quoting, workforce training, new IPC leadership in the U.S. and Canada, the effects of tariffs, CFX standards, and much more—all designed to provide perspective as you move through the cloud bank of today's shifting economic market.
Intelligent Test and Inspection
Are you ready to explore the cutting-edge advancements shaping the electronics manufacturing industry? The May 2025 issue of SMT007 Magazine is packed with insights, innovations, and expert perspectives that you won’t want to miss.
- Articles
- Columns
- Links
- Media kit
||| MENU - smt007 Magazine
SMTA Europe’s Electronics in Harsh Environments Conference and Exhibition: A Taste of Things to Come
April 14, 2020 | Pete Starkey, I-Connect007Estimated reading time: 7 minutes
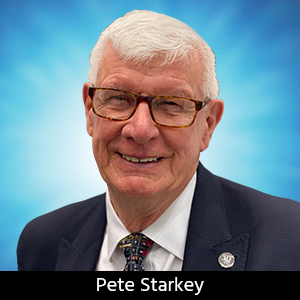
SMTA Europe’s Electronics in Harsh Environments Conference and Exhibition has become a must-attend annual event; unfortunately, it also became another casualty of the COVID-19 lockdown. Scheduled to take place in Amsterdam, the Netherlands, from April 21–23, 2020, it has now been postponed until December 1–3.
The conference will tackle the challenges and best practices for building reliable electronic devices that will perform to design standards when used in harsh environments. Specific topics will include building reliable high-density assemblies, power electronics, electric hybrids, product assembly challenges, cleaning, coating, process control, and monitoring and tracking production hardware. Challenging areas—such as high-temperature soldering, solder material advances, and new standards—will be presented. In addition, the event will provide a tremendous networking opportunity and tabletop exhibition, offering a chance to chat with leading suppliers to this industry sector.
To give a taste of what to expect in December, and to underscore some programme highlights and to emphasise the benefits of attending the conference, SMTA Europe Chairman Keith Bryant joined Technical Committee member and online training specialist Bob Willis to present a preview webinar while observing proper social distancing. A full-house of design, process, and quality engineers tuned in from Europe, North America, and further afield on the afternoon of April 7 to find out more about the demands on electronics in harsh environments.
Why Amsterdam? Bryant explained that being a central hub for many global airlines, with a mainline rail station under the international airport and major road links from all of Europe, it was an easily accessible location and the welcoming city had many creative and imaginative attractions as well as hundreds of excellent restaurants and bars. The conference has established an impressive history of building year-on-year success, and Bryant’s video reflection on the 2019 event registered some very positive feedback.
Dr. Rakesh Kumar—VP of technology for Specialty Coating Systems, returning conference delegate, and tabletop exhibitor—enjoyed the learning experience together with the opportunity to meet industry experts and appreciate the perspectives of presenters on future electronics and testing requirements. As well as gathering positive customer leads, he absorbed a great deal of valuable information with which to guide his development and marketing teams.
Conference Chair Mike Bixenman remarked on the strength of technical content and the objective mix of academia and industry expertise, which was also echoed by keynote speaker Dave Hillman, who observed the balanced collision of academia and industry—“The place to be to get good technical information—everything we thought it would be and more!”
Beth Turner from Electrolube, exhibitor and first-time conference attendee in 2019, commented that the conference was a great learning and networking opportunity with excellent presentations and everyone keen to share knowledge. In particular, she learned more about current challenges in automotive electronics and where her company’s products could help to provide solutions. “Highlights? The whole event! The tabletop has definitely been commercially worthwhile and a great opportunity to meet people.”
Next, Bryant answered the question, “What’s considered a harsh environment?” He listed extreme high or low operating temperatures, corrosive chemicals—such as saltwater—automotive and aerospace fuels, and noxious gases found in automotive, aerospace, and petrochemical applications. However, this doesn’t just include equipment that would go under the hood of a motor car or down an oil well, it’s but increasingly in consumer applications, such as dishwashers and washing machines. “Harsh environments are nearly everywhere!”
Exploring the agenda for the 2020 event, Bryant recommended attending the professional development course on advanced materials analysis, which would introduce an interesting approach to reliability testing and provide fast and accurate results. The conference programme would then consist of five sessions of technical presentations from a host of distinguished speakers on the themes: electrochemical reliability of PCBs in the automotive industry, electrochemical reliability of leadless and bottom-terminated components, electronics reliability, climatic reliability of electronics, solder material advancement for harsh environments, and a concluding session from iNEMI.
Having made his comprehensive introduction, Bryant handed the screen to Bob Willis to talk in more detail about some of the featured presentations. Willis began with a discussion of low-temperature soldering—an anomalous topic in a harsh environment conference but significant in the more mundane areas of hand soldering, rework, and repair, especially when damage to the solder joints on adjacent components was to be avoided. Much of the published knowledge was based on development work by Hewlett-Packard, and both Alpha and Indium had some time promoted the use of low-temperature soldering.
More recently, IBM/Lenovo shared their experience on the manufacturing of boards for some of their laptop products. Some adjustment of paste volume and reflow profile was required, not only a reduced peak temperature but particularly to ensure adequate cooling to avoid the possibility of displaced components. Early problems with voiding on reworked BGA packages had been overcome by increasing the time at reflow temperature. Willis showed temperature-time graphs of comparative reflow profiles and an example of successful QFN rework and repair achieved by preheating to 100°C and then reflowing with a peak board temperature of 160°C using infrared, top-side heating.
The next topic previewed by Willis was the use of condensation testing for evaluating combinations of PCB assembly processes and protection materials, with reference to work at the National Physical Laboratory on the in-process measurement of conformal coating coverage. He explained that electronic circuits could suffer from condensation effects in service where there was a rapid change in temperature and/or humidity either for the circuit assembly itself or in the ambient conditions. The classic case was for an aircraft landing from high altitude. Because the conditions generally lasted only for a few minutes, condensation was a transient effect and difficult to control and repeat. NPL had developed a test apparatus in which sample temperature could be varied independently from the environment, and hence the condensation level could be controlled and its effects measured.
As electronic circuits continued to move to increased packaging densities and operated at higher voltages and in harsher environments, electrochemical reliability was becoming more critical. A significant topic for discussion at the conference would be the main causes of electrochemical failures, and how insulation resistance techniques could be used to monitor conductive anodic filament (CAF) failures at higher test voltages. This would have particular relevance to aerospace and automotive applications. Willis explained that test design and results of CAF failures under different biases up to 1000 volts DC would be presented, together with a discussion of the conclusions on the effect of bias voltage on CAF formation, with the prospect of a new collaborative research project being announced.
Surface insulation resistance (SIR) testing has become increasingly significant in the industry. Willis referred to the IPC-9201A Surface Insulation Resistance Handbook, the IPC-9203 Users Guide to IPC-9202, and the IPC-B-52 Standard Test Vehicle, to which he had proposed the addition of test patterns to represent QFN (quad-flat no-leads) packages. He showed examples of the modified test vehicle, and discussed assessment methods, stressing the importance of examining the actual samples as well as the data. At the conference, the results of SIR testing, in combination with NPL condensation testing, would be discussed in detail and correlated with ion chromatography studies.
Willis handed the screen back to Bryant, who previewed his own presentation on failure mechanisms in insulated-gate bipolar transistors IGBTs) in applications “from wind farms to rice cookers.” Failure in an off-shore wind turbine could have extremely expensive consequences, and his illustration of a burned-out IGBT module showed catastrophic damage. Bryant also explained the structure of a module, with its many materials and interfaces, and demonstrated the effect of solder voids obstructing heat transfer and resulting in unstable behaviour at the die because of localised overheating. Faults could be detected using X-ray techniques and scanning acoustic microscopy, and the objective was to eliminate them by improved manufacturing standards.
Bryant’s closing remarks: “A few more things to convince you. Obviously, it’s a good networking event with plenty of free time to mix with the speakers and exhibitors. It’s also a chance to chat with the other attendees and a good opportunity to build up your network of contacts. There will be people there from SMTA who will be pleased to tell you about other events that are happening, and other ways of getting involved and how you can see a lot of added value from SMTA or SMTA Europe membership. These events always bring value to you and to your company, so I thoroughly recommend that you come along and join us!”
For more information, click here.
Testimonial
"Advertising in PCB007 Magazine has been a great way to showcase our bare board testers to the right audience. The I-Connect007 team makes the process smooth and professional. We’re proud to be featured in such a trusted publication."
Klaus Koziol - atgSuggested Items
Weller Tools Supports Future Talent with Exclusive Donation to SMTA Michigan Student Soldering Competition
07/23/2025 | Weller ToolsWeller Tools, the industry leader in hand soldering solutions, is proud to announce its support of the upcoming SMTA Michigan Expo & Tech Forum by donating a limited-edition 80th Anniversary Black Soldering Set to the event’s student soldering competition.
Koh Young Appoints Tom Hattori as President of Koh Young Japan
07/21/2025 | Koh YoungKoh Young Technology, the global leader in True 3D measurement-based inspection solutions, announced the appointment of Tom Hattori as President of Koh Young Japan (JKY).
Silicon Mountain Contract Services Enhances SMT Capabilities with New HELLER Reflow Oven
07/17/2025 | Silicon Mountain Contract ServicesSilicon Mountain Contract Services, a leading provider of custom electronics manufacturing solutions, is proud to announce a significant upgrade to its SMT production capability with the addition of a HELLER 2043 MK5 10‑zone reflow oven to its Nampa facility.
Knocking Down the Bone Pile: Addressing End-of-life Component Solderability Issues, Part 4
07/16/2025 | Nash Bell -- Column: Knocking Down the Bone PileIn 1983, the Department of Defense identified that over 40% of military electronic system failures in the field were electrical, with approximately 50% attributed to poor solder connections. Investigations revealed that plated finishes, typically nickel or tin, were porous and non-intermetallic.
SHENMAO Strengthens Semiconductor Capabilities with Acquisition of PMTC
07/10/2025 | SHENMAOSHENMAO America, Inc. has announced the acquisition of Profound Material Technology Co., Ltd. (PMTC), a premier Taiwan-based manufacturer of high-performance solder balls for semiconductor packaging.