-
- News
- Books
Featured Books
- smt007 Magazine
Latest Issues
Current IssueSpotlight on India
We invite you on a virtual tour of India’s thriving ecosystem, guided by the Global Electronics Association’s India office staff, who share their insights into the region’s growth and opportunities.
Supply Chain Strategies
A successful brand is built on strong customer relationships—anchored by a well-orchestrated supply chain at its core. This month, we look at how managing your supply chain directly influences customer perception.
What's Your Sweet Spot?
Are you in a niche that’s growing or shrinking? Is it time to reassess and refocus? We spotlight companies thriving by redefining or reinforcing their niche. What are their insights?
- Articles
- Columns
- Links
- Media kit
||| MENU - smt007 Magazine
Estimated reading time: 4 minutes
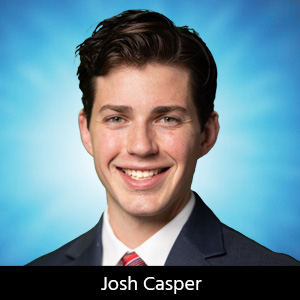
Smart Automation: What Industry 4.0 Means for Mid-sized Electronics Manufacturing
Industry 4.0 has become a go-to phrase in manufacturing circles, though it’s often used as a slogan rather than a clearly defined concept. At electronics manufacturing trade shows or conferences, marketing banners and vendor literature display the term prominently; many technical sessions also focus on it. Industry 4.0 is the push for smart factories, with a focus on autonomous machines, cloud-connected systems, and AI-powered decisions.
For global Tier 1 OEMs and large EMS providers, it’s a necessity. For mid-sized SMT manufacturers, it can sound more like marketing than reality. But, buried beneath the buzzwords are real tools that can help even small- and mid-sized operations improve quality, reduce waste, and remain competitive. Here, we explore what Industry 4.0 means for mid-sized SMT manufacturers, removing the buzz and highlighting practical steps to become smarter, more responsive manufacturers.
What Does Industry 4.0 Mean?
Industry 4.0, also known as the fourth industrial revolution, uses advanced technologies like the Internet of Things (IoT) and artificial intelligence (AI) to transform manufacturing. At its core, Industry 4.0 is about using connected systems, real-time data, and intelligent automation to make manufacturing more flexible and efficient.
There’s a misconception that Industry 4.0 means fully automating the factory, having all equipment communicate with each other, and implementing a full MES overhaul. That’s unrealistic for most mid-sized manufacturers, but the goals of better visibility, faster problem-solving, and streamlined systems are achievable.
Why Mid-sized Manufacturers Need a Different Approach
Mid-sized SMT operations face unique pressures. Many focus on high-mix, low-to-mid-volume builds. They must adjust quickly, manage frequent changeovers, and maintain traceability, often for demanding industries such as automotive, medical, and aerospace. Many do not have large full-time IT departments or unlimited CapEx budgets. Investments need to pay off quickly, be easy to implement, and scale gradually. That’s where a practical Industry 4.0 strategy can shine.
Practical Steps Toward Industry 4.0
1. Leverage existing information on the shop floor.
Extract and contextualize the data already being recorded. Most modern SMT equipment collects and stores vast amounts of important data. The problem is the ability to paint a full picture when that data is siloed within a given machine. Unifying data through connectivity solutions allows the manufacturer to see the entire line as a living entity, rather than separate systems operating independently toward a single goal. Whether it’s correlating a misprint with a defect found at AOI or understanding placement yields across multiple lines, understanding and contextualizing this data is a critical step in Industry 4.0. By taking this step, the manufacturer has the building blocks to one day implement AI-driven predictive analysis tools. Basic connectivity gives the user visibility they didn’t previously have, and it’s the first building block to everything else.
2. Use AOI and SPI data to improve yield in real time.
Inspection systems are common in most mid-sized operations. Closed-loop feedback with upstream and downstream machines is an easy win. Many modern inspection systems support some level of closed-loop feedback, where print inspection results can automatically adjust printer settings, or AOI inspection results can drive placement offsets before reflow. These feedback loops improve first-pass yield with no operator intervention and help stabilize the line without added complexity. The hardware likely exists at the manufacturer today; often, it simply takes a small investment for an SW license and configuration to begin.
3. Automate human-intensive, low-value tasks.
Not all automation requires convoluted SW integration or AI. In many facilities, the drag on efficiency is repetitive manual work, such as restocking components, placing labels, and hand-scanning barcodes. Targeting these human-intensive, low-skill tasks is one of the best ways to deploy smart automation. Tools such as intelligent storage towers, feeder verification systems, and automated laser marking help reduce errors and speed up line changes. They don’t require a full digital ecosystem to function, just planning and modular integration. The result is higher throughput, fewer errors, and happier employees.
4. Implement scalable MES or traceability systems.
For many manufacturers, leaping into a full-blown MES is like jumping into a jet’s cockpit without flying lessons. Many mid-sized operations can start with simple and scalable traceability systems that track board IDs and component placement data through the line. Choose platforms that are modular and scalable, expanding over time to include scheduling, WIP tracking, and rework. The visibility gained, even from basic tracking, improves customer reporting, root cause analysis, and compliance documentation. A phased MES approach makes traceability another tool, not a burden.
What to Watch Out For
While Industry 4.0 offers real benefits, it’s easy for a mid-size manufacturer to derail. Here are common pitfalls to avoid:
- Trying to simultaneously implement multiple improvements: Prioritize based on ROI, and phase the approach. Trying to implement too many new processes at one time can spread staff too thin, even when automation is the ultimate labor re-allocator.
- Investing in automation without process clarity: Automating a broken process simply creates poor results more quickly. Prioritizing the understanding of the process leads to successful investment evaluations and better results.
- Underestimating culture shift: Keep interfaces simple, and train staff well. Adoption matters more than capability, and success depends on training and buy-in.
- Ignoring cybersecurity: Even modest networks need protection from intrusion, malware, or IP theft.
Conclusion: Smart Doesn’t Have to Be Expensive
Industry 4.0 isn’t only for the giants. Mid-sized electronics manufacturers have as much to gain. With modular, affordable tools, there's no reason to sit on the sidelines. Identify where the pain is, use the data that already exists, and choose tools that grow with the manufacturer.
This column originally appeared in the July 2025 issue of SMT007 Magazine.
More Columns from Smart Automation
Smart Automation: Pick-and-place Machines—What Matters in 2025Smart Automation: The Power of Data Integration in Electronics Manufacturing
Smart Automation: AI—Revolutionizing Inspection in Electronics Manufacturing
Smart Automation: The Growing Role of Additive Manufacturing