-
- News
- Books
Featured Books
- pcb007 Magazine
Latest Issues
Current IssueThe Growing Industry
In this issue of PCB007 Magazine, we talk with leading economic experts, advocacy specialists in Washington, D.C., and PCB company leadership to get a well-rounded picture of what’s happening in the industry today. Don’t miss it.
The Sustainability Issue
Sustainability is one of the most widely used terms in business today, especially for electronics and manufacturing but what does it mean to you? We explore the environmental, business, and economic impacts.
The Fabricator’s Guide to IPC APEX EXPO
This issue previews many of the important events taking place at this year's show and highlights some changes and opportunities. So, buckle up. We are counting down to IPC APEX EXPO 2024.
- Articles
- Columns
Search Console
- Links
- Events
||| MENU - pcb007 Magazine
Estimated reading time: 3 minutes
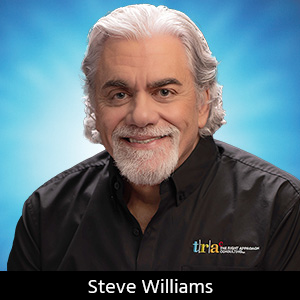
The Right Approach: The Founding Fathers of Quality–Juran and Crosby
This column continues the series of installments, each highlighting one of the seven founding fathers of quality (as selected by the author). It is important to understand and acknowledge their revolutionary contributions that still form the foundation of modern quality practices.
Joseph M. Juran (1904–2008)
Dr. Juran's concepts can be used to establish a traditional quality system based around his famous quality trilogy of quality planning, quality control, and quality improvement (Figure 1). Dr. Juran was invited to Japan in 1952 by the Union of Japanese Scientists and Engineers to teach his principles of quality management as the country tried to rebuild its economy. Unfortunately, it wasn’t until the late ‘80s that Dr. Juran finally got the attention of American management when he declared, “In the U.S.A., about one-third of what we do consists of redoing work previously done.”
Juran’s Quality Trilogy
Quality Planning
Juran defined this first stage as providing operators with the tools to produce goods and services that can meet customers' needs. Juran’s vision was perhaps the precursor to today’s “voice of the customer” concept, as he believed an organization must determine who its customers are and what they need before any thought of process or product can be considered. Once this has been determined, the next step is to develop processes that will deliver products or services that meet these needs. Juran’s premise was that if quality planning is poor, then chronic waste will occur in any process.
Quality Control
The second stage of the trilogy has nothing to do with influencing quality; it is merely the assessment (inspection) function that compares actual performance to a standard. This is the point where many companies allocate considerable resources in the hope of quality improvement. This premise is flawed because quality cannot be “inspected in”; it must be “built in.” While quality control is not a value-add proposition, what it does do is identify chronic waste opportunities for the final stage of the trilogy.
Quality Improvement
This final stage of Juran’s quality trilogy holds that the chronic waste identified by quality control should be considered an opportunity for quality improvement. Quality improvement is the systematic approach to the reduction or elimination of waste in a process. This can take many forms but should seek to continually establish a higher level of performance than previously achieved.
Philip B. Crosby (1926–2001)
Philip Crosby has been called “The fun uncle of the quality revolution” and had a talent for explaining a sometimes dry subject matter into terms that were simple and understandable to the average Joe. He coined the rally cry, “Do it right the first time,” and was the first to introduce a “zero defects” mentality to manufacturing, which is not unlike today’s Lean/Six Sigma movement. Like many of his colleagues, Crosby placed the responsibility with management for creating a culture of defect elimination without pointing blame at the operators.
Another key attribute of this methodology was Crosby’s definition of quality as conformance to a specification, not some ambiguous measure of goodness. As Crosby once famously stated, "Quality is conformance to requirements; non-quality is nonconformance." I would agree with this viewpoint but argue against the common misperception that there can be “good quality” or “bad quality”; there can only be quality. Crosby established the four absolutes of quality management as a foundation for his 14 steps to quality improvement (Figure 2).
Crosby's 14 Steps to Quality Improvement
- Management commitment
- Develop a quality improvement team
- Quality measurement
- Cost of quality evaluation
- Quality awareness
- Corrective action
- Zero defects planning
- Employee education
- Zero defects day
- Goal setting
- Error-cause removal
- Recognition
- Quality councils
- Do it over again
Conclusion
Juran’s focus on quality planning as a primary tool for improvement and the proclamation that quality cannot be “inspected in” has stood the test of time. While I disagree with Uncle Phil’s premise that “quality is free,” his groundbreaking work to drive organizations to the goal of zero defects has resulted in tremendous quality improvement in U.S.-made products. Much can still be learned from these two founding fathers.
This column originally appeared in the January 2020 issue of PCB007 Magazine.
More Columns from The Right Approach
The Right Approach: I Hear the Train A Comin'The Right Approach: Culture Change is Key to a QMS
The Right Approach: Leadership 101—Be a Heretic, Not a Sheep
The Right Approach: Leadership 101—The Law of Legacy
The Right Approach: Leadership 101: The Law of Explosive Growth
The Right Approach: Leadership 101—The Law of Timing
The Right Approach: The Law of Sacrifice
The Right Approach: The Law of Priorities