-
- News
- Books
Featured Books
- pcb007 Magazine
Latest Issues
Current IssueInventing the Future with SEL
Two years after launching its state-of-the-art PCB facility, SEL shares lessons in vision, execution, and innovation, plus insights from industry icons and technology leaders shaping the future of PCB fabrication.
Sales: From Pitch to PO
From the first cold call to finally receiving that first purchase order, the July PCB007 Magazine breaks down some critical parts of the sales stack. To up your sales game, read on!
The Hole Truth: Via Integrity in an HDI World
From the drilled hole to registration across multiple sequential lamination cycles, to the quality of your copper plating, via reliability in an HDI world is becoming an ever-greater challenge. This month we look at “The Hole Truth,” from creating the “perfect” via to how you can assure via quality and reliability, the first time, every time.
- Articles
- Columns
- Links
- Media kit
||| MENU - pcb007 Magazine
Estimated reading time: 2 minutes
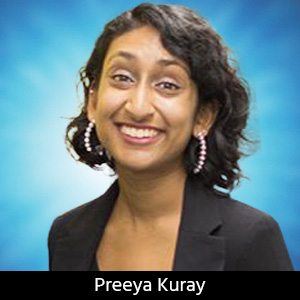
Material Insight: The Dielectric Constant of PCB Materials
In the world of PCB design, miniaturization can be achieved by using low dielectric constant (Dk) materials. Low Dk materials can allow for a reduction in thickness while maintaining a given trace width, leading to lower transmission loss and higher density circuitry:
In this equation, Z0 is the characteristic impedance, εr is the dielectric constant, w is the trace width, and h is the distance from the trace to the ground plane. When the characteristic impedance of a transmission line matches the impedance of connected devices (source and load), there is minimal reflection of the signal, and energy is efficiently transferred. Utilizing a material with the appropriate dielectric constant to achieve impedance matching is imperative to ensure signal integrity and proper circuit operation.
But from a materials science perspective, what is the dielectric constant? Why do some classes of materials inherently have lower or higher dielectric constants?
Scientifically, the dielectric constant of a material represents its ability to store electrical energy when exposed to an applied electric field. It also represents how well a material’s dipoles (i.e., internal charge distribution) align with that applied field. Just like how a magnet has a north and south pole, all materials have an internal charge distribution, contingent upon the atoms that make up that material and how they are bonded together. When an electric field is applied to a dielectric material, its internal dipoles align with the field, resulting in polarization of the material. This polarization allows the material to store electric charge by creating an electric field opposing the applied field. The higher the dielectric constant, the more the material can polarize and the more charge it can store. In contrast, materials with lower dielectric constants exhibit weaker interactions with the applied field (storing less charge), allowing for electrical signals to propagate faster throughout the material.
Another way to contextualize the dielectric constant is to imagine a highway where cars are moving. Think of the PCB as that highway but with tiny signals instead of cars. The dielectric constant can be thought of as analogous to the road surface: some roads are smooth, allowing cars to move faster, while others are bumpy, slowing them down. In a somewhat similar sense, the dielectric constant is a measure of how easily the signals on a PCB can move. A material with a low dielectric constant indicates that signals can move smoothly throughout the substrate. This next equation equates signal propagation speed to dielectric constant, where v is the propagation speed of a signal throughout the material, c represents the speed of light, and εr is the dielectric constant of the substrate material:
It is the job of the formulation scientist to create new kinds of PCB materials that will achieve the target dielectric constant of the desired application. This is achieved by combining different materials with different dielectric constants. Ceramic fillers and polymer resins are two important classes of materials used in creating PCB bondply that will contribute to the overall dielectric constant of the final product. It is imperative to consider the dielectric constant of every material used to successfully achieve the target properties of the final product.
This column originally appeared in the April 2024 issue of PCB007 Magazine.
More Columns from Material Insight
Material Insight: David Griesel: Career Success Requires Tenacity, FlexibilityMaterial Insight: Diversifying PCB Manufacturing Through Nearshoring
Material Insight: The Importance of Standards for the Chip Packaging Industry
Material Insight: A Conversation with Congressman Blake Moore
Material Insight: The Material Science of PCB Thermal Reliability
Material Insight: India’s Rise in the Global Electronics Ecosystem
Material Insight: The Revival of Domestic PCB Fabrication
Material Insight: My Journey From Atomic Lattices to Circuit Boards