-
- News
- Books
Featured Books
- pcb007 Magazine
Latest Issues
Current IssueThe Hole Truth: Via Integrity in an HDI World
From the drilled hole to registration across multiple sequential lamination cycles, to the quality of your copper plating, via reliability in an HDI world is becoming an ever-greater challenge. This month we look at “The Hole Truth,” from creating the “perfect” via to how you can assure via quality and reliability, the first time, every time.
In Pursuit of Perfection: Defect Reduction
For bare PCB board fabrication, defect reduction is a critical aspect of a company's bottom line profitability. In this issue, we examine how imaging, etching, and plating processes can provide information and insight into reducing defects and increasing yields.
Voices of the Industry
We take the pulse of the PCB industry by sharing insights from leading fabricators and suppliers in this month's issue. We've gathered their thoughts on the new U.S. administration, spending, the war in Ukraine, and their most pressing needs. It’s an eye-opening and enlightening look behind the curtain.
- Articles
- Columns
- Links
- Media kit
||| MENU - pcb007 Magazine
ECWC15 Virtual Conference Keynote: 5G PCB Technology and Material Challenges
December 7, 2020 | Pete Starkey, I-Connect007Estimated reading time: 7 minutes
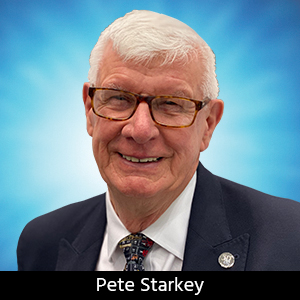
The second day of the Electronic Circuits World Convention began with a keynote from Dr. Shiuh-Kao Chiang, managing partner of Prismark, describing the PCB technology and material challenges presented by the introduction of the fifth-generation cellular wireless communication network—the roll-out of which was continuing in spite of the coronavirus pandemic.
The electronics industry was in the midst of a period of radical change, the main stimulus being a fundamental upgrade in infrastructure equipment, with printed circuits driven by high-speed, high-frequency demands to enable much faster wireless communication. Once the data-centre investment cycle and 5G build-out had been completed, momentum was likely to shift back to smart and portable consumer products. Dr. Chiang forecast that for the next few years, the industry would continue to grow at a compound rate of over 5%.
From a product perspective, while other sectors were suffering a decline in value, packaging substrates were showing relatively strong growth due to demand for components used in computer-related areas: central processor units, graphics processor units, artificial intelligence, and advanced packaging for large devices. For the next few years, continuing growth was forecast in packaging substrates, high-density interconnect, flexible circuits, and multilayer boards.
Multilayer boards would continue to play a very important role in 5G infrastructure, servers, and networking systems, but their material characteristics and fabrication techniques required improvement in order to satisfy the high-speed demand. Developments in HDI and flex would be driven by portable systems and substrate developments by flip-chip BGA and 5G terminal devices, particularly the antenna-in-package (AIP) module used in the 5G smartphone. Dr. Chiang considered the industry to be in the middle of the infrastructure transformation, and that 5G was the key element of that change.
The most important feature of the infrastructure upgrade was that the signal was travelling at a much higher speed and at a much higher frequency. “High speed in the board, high frequency in the air.” This applied to almost all the devices and presented challenges to the PCB industry: to develop newer technology, newer materials, and newer processing methods to avoid signal loss and ensure that data could be transmitted at a higher rate without suffering distortion or interference.
Major features differentiating 5G from its 3G and 4G predecessors were high frequency and multiple-in-multiple-out (MIMO), necessitating multiple antennae capable of changing and strengthening the signal in certain directions. The design of the circuit board in the base station required multiple antenna elements and the ability to receive, process, and transmit signals at high frequency. And the terminal device—for example, a mobile phone—is similarly required to receive and transmit signals at high frequency, making the PCB more complex (and of substantially higher value) than its 4G equivalent. Additionally, high-value flexible circuits and feed-lines would be required, fabricated from materials capable of carrying high-frequency signal without distortion or loss. Advanced low-loss rigid and flexible materials presented challenges to laminate suppliers.
But the 5G system involved much more than high-frequency communication between the terminal device and the base station: the networking system passed the signal to the data centre, server, data processing, data storage, or data re-direct to other users. The overall system was bringing major changes to the architecture of the base station. In the past, the antenna, the power amplifier, and the transceiver were typically separate functional units, with the antenna at the top of the tower and the other units in the base station. Alternatively, everything but the base-band unit could be incorporated in the tower box, together with the antenna.
Dr. Chiang made it clear that the material challenge of a 5G system depended on the frequency range it was operating in and which functional unit of which circuit board was being considered. 5G could effectively be seen as two different systems: less than 6 GHz was classed as “mid-to-low frequency,” and millimetre-wave as “high-frequency.” In the mid-to-low frequency class, the architecture was actually similar to that of the 4G base station, the main difference being that more antenna units were required, but the frequency band was actually similar to 4G, and the industry had plenty of experience in designing, manufacturing, and assembling PCBs for this frequency range. The main trend involved the integration of a transceiver, power amplifier, and antenna together as an active antenna.
In contrast, 5G operating at frequencies of up to 70 GHz required new materials—typically high-frequency material for the antenna and high-speed material for the base-band unit. Many different low-loss materials had been introduced over the past 2–3 years, some PTFE-based, some modified PTFE-like material, with low Dk and low Df characteristics, which were processable and suitable for the integration of the antenna function, the power amplifier function the transmit-receiver function into one active antenna unit. Fine-pitch circuitry and HDI were typical design features, with high layer count and high component density.
An active antenna unit for a 5G base station had multiple antenna elements, individually small in size because they were handling shorter wavelengths, and all mounted on a main board to reduce cable losses. Transceiver components were placed on the reverse of the main board, together with other active and passive components to complete the active antenna function. This type of integration was becoming common, not only in 5G base stations but also linked to other communication equipment and processors, storage, and servers because of the rapid escalation of data generated by consumers.
As wireless communication transferred to the 5G standard, wired communication for computing and processing equipment was also moving to a new standard to enable higher data rates and volumes. Advances in data transfer standard from PCIe 3.0 to PCIe 4.0 to PCIe 5.0 demanded laminate to be upgraded from mid-loss to low-loss to very-low-loss, and the industry was presently in the middle of this transition process. Similarly, with the networking system, changing standards necessitated a move from very-low-loss to ultra-low loss laminates with lower Dk and lower Df. Typically, materials were grouped into two categories: high-speed, which is usually used for server, base station, and base-band units—and RF—high-frequency, low-loss material, which is usually used for the antenna function. The two groups were merging together for ultra-low-loss, with dielectric properties approaching those of an RF material.
In general, material properties continued to improve and satisfy the need for higher-frequency and higher-speed applications. And in developments beyond ultra-low-loss, materials with even lower Dk and Df values were becoming commercially available. Not only were base station considerations creating material challenges, but 5G terminal devices also had specific requirements.
Dr. Chiang’s team had examined the workings of the newly-released iPhone 12 with the 5G millimetre-wave feature. For frequencies under 6 GHz, the antenna structure was typically similar to that used in 4G. But separate antennae were needed for high-frequency 5G signals, and the iPhone 12 had three separate antennae: passive units facing to the front and back and an antenna-in-package module facing to the side with different structures for different frequencies. The passive antennae were connected to active components elsewhere on the main board. The antenna-in-package module incorporated transceiver and passive components to form a complete antenna function. A cross-section of this module showed a very sophisticated 16-layer any-layer circuit board in low-loss material, with its component side facing inward and the antenna part facing out.
Two of the antennae were connected to the main board through feed-lines, flexible circuits made of very-low-loss material, similar to the PTFE-like antenna circuit board used in the 5G base station—an example of a new material specially developed for 5G applications. Liquid crystal polymer has become popular as a low-loss flexible circuit material.
Although low Dk and low Df values could be achieved by modifying resin formulations and additives, low Dk glass fabric could further improve dielectric properties, although the cost was high and supply was limited. Signal integrity could be improved and transmission losses through skin effect reduced by the use of low-profile copper foil, and Dr. Chiang showed a comparison of different foil grades from general purpose to the ultra-smooth H-VLP2 material compatible with millimetre-wave frequencies. Reverse-treated foil was also available.
Dr. Chiang’s keynote presentation was a detailed and comprehensive overview of the changing electronics industry and the challenges being overcome by material suppliers and PCB fabricators in meeting the technological demands of 5G as it continues its evolution.
This was an informative, stimulating, and enjoyable introduction to the second day of the ECWC15 Virtual Conference. My grateful thanks to the Hong Kong Printed Circuit Association for hosting and managing a superb event.
Suggested Items
Trump Copper Tariffs Spark Concern
07/10/2025 | I-Connect007 Editorial TeamPresident Donald Trump stated on July 8 that he plans to impose a 50% tariff on copper imports, sparking concern in a global industry whose output is critical to electric vehicles, military hardware, semiconductors, and a wide range of consumer goods. According to Yahoo Finance, copper futures climbed over 2% following tariff confirmation.
Happy’s Tech Talk #40: Factors in PTH Reliability—Hole Voids
07/09/2025 | Happy Holden -- Column: Happy’s Tech TalkWhen we consider via reliability, the major contributing factors are typically processing deviations. These can be subtle and not always visible. One particularly insightful column was by Mike Carano, “Causes of Plating Voids, Pre-electroless Copper,” where he outlined some of the possible causes of hole defects for both plated through-hole (PTH) and blind vias.
Trouble in Your Tank: Can You Drill the Perfect Hole?
07/07/2025 | Michael Carano -- Column: Trouble in Your TankIn the movie “Friday Night Lights,” the head football coach (played by Billy Bob Thornton) addresses his high school football team on a hot day in August in West Texas. He asks his players one question: “Can you be perfect?” That is an interesting question, in football and the printed circuit board fabrication world, where being perfect is somewhat elusive. When it comes to mechanical drilling and via formation, can you drill the perfect hole time after time?
The Evolution of Picosecond Laser Drilling
06/19/2025 | Marcy LaRont, PCB007 MagazineIs it hard to imagine a single laser pulse reduced not only from nanoseconds to picoseconds in its pulse duration, but even to femtoseconds? Well, buckle up because it seems we are there. In this interview, Dr. Stefan Rung, technical director of laser machines at Schmoll Maschinen GmbH, traces the technology trajectory of the laser drill from the CO2 laser to cutting-edge picosecond and hybrid laser drilling systems, highlighting the benefits and limitations of each method, and demonstrating how laser innovations are shaping the future of PCB fabrication.
Day 2: More Cutting-edge Insights at the EIPC Summer Conference
06/18/2025 | Pete Starkey, I-Connect007The European Institute for the PCB Community (EIPC) summer conference took place this year in Edinburgh, Scotland, June 3-4. This is the third of three articles on the conference. The other two cover Day 1’s sessions and the opening keynote speech. Below is a recap of the second day’s sessions.