-
-
News
News Highlights
- Books
Featured Books
- smt007 Magazine
Latest Issues
Current IssueWhat's Your Sweet Spot?
Are you in a niche that’s growing or shrinking? Is it time to reassess and refocus? We spotlight companies thriving by redefining or reinforcing their niche. What are their insights?
Moving Forward With Confidence
In this issue, we focus on sales and quoting, workforce training, new IPC leadership in the U.S. and Canada, the effects of tariffs, CFX standards, and much more—all designed to provide perspective as you move through the cloud bank of today's shifting economic market.
Intelligent Test and Inspection
Are you ready to explore the cutting-edge advancements shaping the electronics manufacturing industry? The May 2025 issue of SMT007 Magazine is packed with insights, innovations, and expert perspectives that you won’t want to miss.
- Articles
- Columns
- Links
- Media kit
||| MENU - smt007 Magazine
Chapter 1 Excerpt: The Printed Circuit Assembler’s Guide to Process Validation
December 31, 2020 | Graham Naisbitt, Gen3 SystemsEstimated reading time: 2 minutes
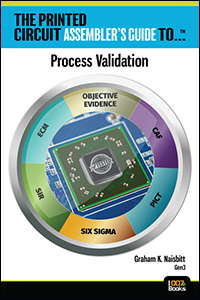
Quick and Convenient Contamination Testing
The original principle underlying the IPC’s ionic cleanliness requirement was that the mobility of surface ions, detectable from SIR measurements, would correlate to a maximum value of detectable ionic elements permissible on the circuit surface.
The industry required a test that was both fast and accurate for process control. Thus, a simplified ion chromatograph that was able to detect ionic elements without differentiation was created. Due to patent restrictions, there were—and still are—only two different instrument configurations: closed-loop and open-loop, which became referred to as static and dynamic instruments. Each instrument configuration must be capable of measuring the presence of a known amount of ionic contamination.
Based on an extrapolation of insulation resistance measurements, it was determined that there was an upper limit beyond which ionic elements would become mobile on the assembly surface, thereby potentially compromising electrochemical reliability. The number, although occasionally altered during the infancy of this test, was 1.56 µg/cm² NaCl equivalence. Despite the many technology changes employed in the period after the mid-1970s, many—if not most—felt it convenient to simply continue applying this rule as adequate evidence of the electrochemical reliability of their end-product.
The IPC has now withdrawn the requirement for 1.56 µg/cm² NaCl equivalence for a number of reasons as explained in IPC-WP-019A, which states, “For many years, military (e.g., MIL-STD-2000) and commercial (e.g., IPC-J-STD-001) manufacturing standards have required manufactured circuit card assemblies (CCAs) to meet an ionic cleanliness requirement of 1.56 microgram (µg) of sodium chloride (NaCl) equivalence per square centimetre (cm2) of extracted surface, using resistivity of solvent extract (ROSE) testing per IPC-TM-650, method 2.3.25.”
Therefore, it is the position of the IPC committees that the value of 1.56 µg NaCl equivalence per square centimetre should be considered as obsolete for the following seven reasons:
- This test methodology was originally developed in the 1970s. It was never intended to be used as a cleanliness test, nor as a test for product acceptability; it was only intended to be used as a process control method.
- The use of the ionic contamination value as a measure of product acceptance was the result of a U.S. Department of Defense desire to implement pass/fail criteria.
- This ionic contamination value, and those derived from them, were originally developed for high solids (35% solids) rosin fluxes and ozone-depleting chemical (ODC) cleaning. The flux chemistries and cleaning solutions used today are completely different from those used when the ROSE limits were established.
- Modern assemblies are simply too complex in terms of residues to have a single “one-size-fits-all” cleanliness criterion.
- There is mounting evidence that as CCA component density increases, so does the sensitivity of the circuit to ionic contamination. Modern circuit assemblies have far greater component densities than found in the 1970s. This also means that residues that had minimal impact on component technologies from the 1970s can now have a significant impact on component reliability.
- For many assemblies, ROSE testing is no longer a sufficient test regimen to adequately predict acceptable levels of ionic residues. IPC has compiled a list of technical presentations showing the inadequacy of ROSE to predict ionic residues for high-performance electronics.
- It is recognized that ionic residue testing is critical for reliable circuit function, so the ROSE test has continued in use until a more suitable alternative can be identified and implemented.
To download The Printed Circuit Assembler’s Guide to Process Validation, click here. You can also view other titles in our full library.
To view the Gen3 roundtable on the PICT standard, click here.
Suggested Items
TRI to Exhibit at SMTA Queretaro Expo 2025
07/16/2025 | TRITest Research, Inc. (TRI), the leading provider of test and inspection systems for the electronics manufacturing industry, is pleased to announce plans to exhibit at the SMTA Querétaro Expo 2025, scheduled to take place on July 24, 2025, at the Querétaro Centro de Congresos y Teatro Metropolitano.
Global PCB Connections: Let the Spec Fit the Board, Not Just the Brand
07/17/2025 | Jerome Larez -- Column: Global PCB ConnectionsIf you’ve ever seen an excellent PCB quote delayed, or worse, go cold because of a single line on the fab print, you’re not alone. Often, that line reads something like, “Use 370HR only,” or “IT-180A required.” These and other brand-name materials are proven performers, but unless your design needs that specific resin system (say, for RF performance, thermal reliability, or stringent CAF resistance), you may inadvertently be holding your job hostage.
IPC Hall of Fame Spotlight Series: Highlighting Lionel Fullwood
07/15/2025 | Dan Feinberg, I-Connect007Many IPC members who have contributed significantly to IPC and our industry have been awarded the IPC Raymond E. Pritchard Hall of Fame (HOF) Award. Though many early HOF members have passed away and are unknown to today’s IPC membership, their contributions still resonate. This special series on IPC Hall of Fame members provides a reminder of who was honored and why. As a bonus, for those who are still around, we get to find out what these talented individuals are up to today.
TRI Unveils New Platform for Diverse Board Sizes
07/14/2025 | TRITest Research, Inc. (TRI), the leading test and inspection systems provider for the electronics manufacturing industry, proudly introduces a new size configuration for SPI and AOI Models.
Seeing a Future in Mexico
07/09/2025 | Michelle Te, I-Connect007The Global Electronics Association (formerly known as IPC) has been instrumental in fostering a partnership with Guanajuato, a state north of Mexico City with 12 industrial clusters and close to 150 companies involved in electronics. This past spring, Alejandro Hernández, the undersecretary for investment promotion in Guanajuato, attended IPC APEX EXPO 2025 at the invitation of IPC Mexico Director Lorena Villanueva, where he met with several companies to discuss the opportunities available in Mexico. He is inviting electronics-related companies seeking long-term investment in a centrally located area with access to highways, railways, and ports.