Estimated reading time: 5 minutes
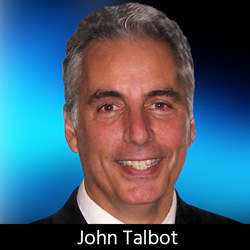
Consider This: Reaching the Limit on Stiffeners
Flexible printed circuit boards, by their very nature, are designed to be flexible. This presents problems in securely and reliably attaching the ends of the flex circuits to a solid, stiff, main PCB or other electronic devices. A combination of hard, as well as semi-flexible stiffeners, is used for this purpose. Hard stiffeners are FR-4, aluminum, and heat conductive aluminum-backed metals. A hard stiffener has a limit as to how close the flex circuit bends to the stiffener without stressing the joint or causing the flex circuit to crease (Figure 1).
Thick flex cover-coat material is used as a semi-stiffener where the flex circuit needs to retain some flexibility close to the attachment point. The slightly less flexible stiffener allows for attachment of the flex to the FR-4 PCB, while providing an area of reduced flexibility, allowing for a more reliable connection without creasing the flex near the attachment point (Figure 2).
Double layers of thicker, cover coat stiffeners create a slightly bendable flex attachment point such as a printer head to a fixed PCB. The cover coat material allows for some stress transition from highly bendable to rigid, reducing the chance of a crease crack in the copper, similar to a short, tapered cord protector on a power tool. Flex circuitry can rip or create openings in the copper traces if the bend radius is too small or the number of flexing cycles is too large. A transition area from hard mount, no-flex stiffener to fully flexible will extend the life of a flex circuit. The viscoelasticity of many 3M adhesives and tapes improves resistance to vibration fatigue by imparting flexibility to a joint or bonded area.
Many modern flex ZIP FFC connectors use a self-adhesive tape wrap or a solid mount with screws, which then slip into a connector soldered to the rigid PCB.
Typically, flex stiffeners are added after the panel is laser routed or die cut, using 3M double-sided tape, epoxy glue or a lamination process using a glue sheet prepreg. The FR-4 stiffeners will be routed out of the desired thickness of FR-4. The adhesive glue sheet is applied to the flex and the two parts aligned, using etch marks or silkscreen marks, and pressed together. The double-sided acrylic adhesive tape will securely attach the two parts together. This method also allows for the stiffeners to overhang the flex area and provide mounting holes or points, as in Figure 1.
In addition to pressure sensitive tape, the parts can be thermally bonded with heat and pressure in a lamination press as a large panel. The typical method is to thermally bond the stiffener to the circuit with the same flexible adhesive that is used to attach the cover lays. Using high heat and pressure, then gluing the parts together, this method will result in a very strong, permanent stiffener bonding. However, using lamination as a method to glue stiffeners is limited to larger panels with a large number of stiffeners, which do not extend past the flex circuit. The flex final circuit and stiffener will have to be routed or laser cut out of the main panel.
Bonding with pressure sensitive, adhesive tape is the most used attachment method available. The attachment is done with PSA (pressure sensitive adhesive) material such as 3M/Tesa Tape, 3M 467MP or 3M 9077. There are over a hundred different types of PSA available from 3M alone. The specific PSA will depend on whether the flexible PCB will be subjected to a high temperature reflow cycle. The type of adhesive used will also depend upon the configuration and/or location of the stiffeners. If a stiffener extends past the flex circuit side, in most cases, it will require a PSA attachment with a locational stiffener outline added to the copper etching data or silkscreen to allow for accurate placement. The flex and stiffener can both be accurately drilled with alignment holes, fitted over a small jig with alignment pins and pressed together with PSA very accurately. Simply press the adhesive side down onto the flex and then peel off the poly-coated kraft paper lining, aligning the stiffener into the pins and applying pressure to secure together.
The PSA creates a very thin, aesthetic bond line caused by glue squish-out between the flex and the stiffener. The stiffeners can be laminated by hand or in an automation setup. The adhesive sheets are easy to die-cut, and CNC rout, as well as laser-cut. The PSA is a simple, easy-to-use, long life, industry leading solution for attaching stiffeners. 3M 467MP is the visually clearest of the 3M transfer tapes, and offers a neat, precise application with no mess or waste when applied to flat surfaces. It has excellent shear strength, as well as high temperature and chemical resistance, making it an ideal choice for stiffener attachment. The PSA tape features 3M high-performance, acrylic adhesive 200MP, an adhesive thickness of 2.0 mils (0.05 mm) and a poly-coated kraft paper liner of 4.2-mil (0.11 mm) thickness.
The 3M 9077 double-sided, pressure sensitive, adhesive tape is a high-temperature adhesive and release liner system that is easy to use. This is the recommended tape to be used for reflow soldering, as it survives short-term exposure to 500°F/260°C for lead-free solder reflow. The 9077 tape maintains high adhesive strength in high temperatures, and is excellent for heat intensive processing, as well as in high temperature attachments to heat sinks. It is ideal for flexible printed circuit attachments to clean metal surfaces with excellent holding power and low outgassing. 3M9077 PST features a 2-mil 3M ultra-high-temperature acrylic adhesive 100HT, a 3.6 mil (.05 mm) clear, heat-resistant, non-woven liner adds stability for die-cutting and converting. The long-term temperature rating is 300°F (150°C) and it is suitable for automotive under-hood applications.
Aluminum is also used as a stiffener with an insulator cover coat strip. This allows for hard mounting to a flat surface other than a PCB. In some applications, thermally conductive material, aluminum, or copper heat conductive laminate can be used to manage heat while providing a hard mounting point for the flex circuit.
This column originally appeared in the March 2021 issue of Design007 Magazine.
More Columns from Consider This
Consider This: Designing Via-in-Pad for Higher Density Flexible CircuitsConsider This: Termination of Flex Circuits
Consider This: PCB Technologies We Need Now and Later
Consider This: Advancements in Printed Circuit Manufacturing Equipment
Consider This: Heavy-Copper Flex Circuits See Large Growth
Consider This: Buried Capacitance Power Planes
Consider This: Let’s Talk About the Basics of Flex
Acrylic vs. Epoxy Adhesives for Flexible Circuits