-
- News
- Books
Featured Books
- smt007 Magazine
Latest Issues
Current IssueWhat's Your Sweet Spot?
Are you in a niche that’s growing or shrinking? Is it time to reassess and refocus? We spotlight companies thriving by redefining or reinforcing their niche. What are their insights?
Moving Forward With Confidence
In this issue, we focus on sales and quoting, workforce training, new IPC leadership in the U.S. and Canada, the effects of tariffs, CFX standards, and much more—all designed to provide perspective as you move through the cloud bank of today's shifting economic market.
Intelligent Test and Inspection
Are you ready to explore the cutting-edge advancements shaping the electronics manufacturing industry? The May 2025 issue of SMT007 Magazine is packed with insights, innovations, and expert perspectives that you won’t want to miss.
- Articles
- Columns
- Links
- Media kit
||| MENU - smt007 Magazine
Excerpt: The Printed Circuit Assembler’s Guide to... SMT Inspection: Today, Tomorrow, and Beyond, Chapter 1
April 8, 2021 | Brent Fischthal, Koh Young AmericaEstimated reading time: 3 minutes
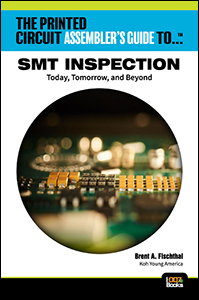
Chapter 1: It All Starts With Vision
Today, optical inspection systems are the preferred solution for in-line quality control in the SMT industry. Systems such as solder paste inspection (SPI) or automated optical inspection (AOI) systems for pre- and post-reflow are almost standard in every production facility.
In the early days of optical inspection, SPI and AOI systems were based on 2D inspection technology. These 2D systems were looking at different grey levels for solder paste, solder joint, and component detection. Most decisions were made by a “good/bad” comparison to reference images, or “golden boards.” But for the solder paste inspection, the most important process indicator for good solder joint quality was missing—namely, paste volume. Consequently, 2D technology for SPI became redundant when 3D measurement solutions were introduced. Years later, the same situation began to occur for AOI.
While many 2D AOI systems still remain in use, the effort needed to keep this technology at a low level of escape and false-call rates is tremendously high. This is because the concept of comparing reference images is still the main technique applied in 2D systems. To help, some equipment manufacturers have added additional cameras and projectors to create quasi 3D or 2.5D technology, but it is still based on the same antiquated, inadequate concept of comparison or color assessment.
Now, after the introduction of 3D AOI, a transition to true 3D measurement is taking place. The benefits are clear: rock-solid threshold and inspection tolerances provide a low escape and false-call rate with minimum debugging effort.
We see the world in 3D, and it is with that data that we are able to see what is good and what is not, what is fit for purpose and what should be inspected out. The same is true of inspection equipment. Only exceptional 3D vision can provide the image data and measurements needed to make the right decision about the fitness of a PCB to continue along the line while providing the data needed to make holistic process improvements.
With increasing board complexity, more components, more joints, higher density, and new package technologies such as 01005 (0402M) and even 008004 (0201M) microchips, 2D AOI technology using grey-scale image analysis or angled camera views of color images are no longer a viable option. Most decisions made are based on “good/bad” comparison of reference images or color assessment, which can easily be affected by variables such as lighting consistency, component surface finish, board condition, and component proximity.
The benefits of 3D inspection are clear:
- Total faith in inspection tolerances
- Reduced effort to debug inspection programs
- Measurement data that provides meaningful insights about the process and helps identify and eliminate the root causes of defects
3D SPI, together with 3D AOI, enables manufacturers to accurately control and monitor the solder printing, the component placement, and the solder reflow processes.
The requirements of 3D AOI to go from inspection to measurement, and ultimately to process control and optimization, is measurement data that is reliable, repeatable, and relatable.
Full 3D Inspection
Some AOI solutions offer a limited level of 3D coverage for components and solder joints. Full 3D coverage is needed to identify boards with defects and help manufacturers monitor their performance. These 3D AOI systems not only inspect common defects, such as missing or wrong components, but accurately identify coplanarity and lead-bridging issues, which are prevalent in small packages and BGAs.
Figure 1.1: Full 3D inspection coverage examples.
Some 3D AOI solutions use multi-frequency shadow moiré technology to measure the Z-axis profilometry of the entire board. By measuring components and solder joints, and then offering critical height information to the inspection algorithms, manufacturers can identify errors such as pad overhang and insufficient solder. Unlike 3D AOI systems using a brightness threshold, the moiré technology uses the height threshold to extract critical body and the lead tip information. This data allows the AOI to provide reliable body and joint measurements with CAD dimensions, since it can locate the body properly in the very first stage of the inspection process.
To download this free eBook, published by I-Connect007, click here.
To view the entire I-Connect007 eBook library, click here.
Suggested Items
Driving Innovation: Direct Imaging vs. Conventional Exposure
07/01/2025 | Simon Khesin -- Column: Driving InnovationMy first camera used Kodak film. I even experimented with developing photos in the bathroom, though I usually dropped the film off at a Kodak center and received the prints two weeks later, only to discover that some images were out of focus or poorly framed. Today, every smartphone contains a high-quality camera capable of producing stunning images instantly.
Hands-On Demos Now Available for Apollo Seiko’s EF and AF Selective Soldering Lines
06/30/2025 | Apollo SeikoApollo Seiko, a leading innovator in soldering technology, is excited to spotlight its expanded lineup of EF and AF Series Selective Soldering Systems, now available for live demonstrations in its newly dedicated demo room.
Indium Corporation Expert to Present on Automotive and Industrial Solder Bonding Solutions at Global Electronics Association Workshop
06/26/2025 | IndiumIndium Corporation Principal Engineer, Advanced Materials, Andy Mackie, Ph.D., MSc, will deliver a technical presentation on innovative solder bonding solutions for automotive and industrial applications at the Global Electronics A
Fresh PCB Concepts: Assembly Challenges with Micro Components and Standard Solder Mask Practices
06/26/2025 | Team NCAB -- Column: Fresh PCB ConceptsMicro components have redefined what is possible in PCB design. With package sizes like 01005 and 0201 becoming more common in high-density layouts, designers are now expected to pack more performance into smaller spaces than ever before. While these advancements support miniaturization and functionality, they introduce new assembly challenges, particularly with traditional solder mask and legend application processes.
Knocking Down the Bone Pile: Tin Whisker Mitigation in Aerospace Applications, Part 3
06/25/2025 | Nash Bell -- Column: Knocking Down the Bone PileTin whiskers are slender, hair-like metallic growths that can develop on the surface of tin-plated electronic components. Typically measuring a few micrometers in diameter and growing several millimeters in length, they form through an electrochemical process influenced by environmental factors such as temperature variations, mechanical or compressive stress, and the aging of solder alloys.