-
- News
- Books
Featured Books
- pcb007 Magazine
Latest Issues
Current IssueThe Hole Truth: Via Integrity in an HDI World
From the drilled hole to registration across multiple sequential lamination cycles, to the quality of your copper plating, via reliability in an HDI world is becoming an ever-greater challenge. This month we look at “The Hole Truth,” from creating the “perfect” via to how you can assure via quality and reliability, the first time, every time.
In Pursuit of Perfection: Defect Reduction
For bare PCB board fabrication, defect reduction is a critical aspect of a company's bottom line profitability. In this issue, we examine how imaging, etching, and plating processes can provide information and insight into reducing defects and increasing yields.
Voices of the Industry
We take the pulse of the PCB industry by sharing insights from leading fabricators and suppliers in this month's issue. We've gathered their thoughts on the new U.S. administration, spending, the war in Ukraine, and their most pressing needs. It’s an eye-opening and enlightening look behind the curtain.
- Articles
- Columns
Search Console
- Links
- Media kit
||| MENU - pcb007 Magazine
Soldering to Aluminum With Mina
October 21, 2021 | Nolan Johnson, I-Connect007Estimated reading time: 3 minutes
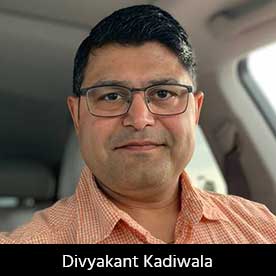
At DesignCon, I caught up with Divyakant Kadiwala of Averatek Corporation. He spent a few minutes explaining a special process developed by Averatek that allows technologists to solder to aluminum.
Nolan Johnson: Divyakant, how about a quick introduction?
Divyakant Kadiwala: I’m the VP of manufacturing at Averatek. My role is to oversee the manufacturing as well as product development and commercialization of Mina, which is a low-temperature soldering surface treatment for aluminum.
Johnson: Mina is a treatment compound that you have developed for some special cases. Walk us through what Mina is all about.
Kadiwala: Soldering to aluminum is difficult. Right now, the only way you can do that is to do an etch of the aluminum oxide using the zincate process, followed by an all-noble metal finish to keep the oxide away. Then you can solder like you would normally do. Mina is a process that takes away all those wet chemistry steps. All you need to do is print the Mina on the pad that needs to be soldered, do a low-temperature cure, which should leave the deposit of Mina on the pads, it’s non-conductive. And then after that, it’s a matter of doing simple SMT operations where you would put the solder paste on the pad, move to pick-and-place to put the components on top, and then reflow. That’s it.
Johnson: That’s pretty straight forward for an otherwise very challenging substrate.
Kadiwala: Yes, it’s especially challenging for aluminum PET substrates because they are low cost and doing these wet chemistry processes would be too expensive. Now PET cannot tolerate high temperatures. But we can still apply the Mina process by using a low temperature solder paste—usually tin bismuth silver alloy—we can go through traditional reflow operations and have a solid PC board.
Johnson: What are some of the typical applications where this technique becomes useful?
Kadiwala: The most common use of aluminum PET substrate is on RFID tags, but these days smart tags are becoming common. Smart tags essentially use the same substrate, but they have a lot more components on them. The method of choice for RFID tags now is to use silver epoxies, but when your tag has lots of components, lots of real estate, that silver epoxy cost adds up, making the overall tag very expensive. Plus, when you make a tag this big, you want to be able to use it for a long time. Silver epoxies are known for cracking, so reliability and longevity of the product is low. So, if you can have a solder solution to the same PC board or smart tag, it’s a better solution. And that’s where Mina is becoming a very important model.
Johnson: If I’m an OEM and I’m looking to manufacture these sorts of applications, how do I access the Mina process? And is this limited to PET?
Kadiwala: In terms of applications for OEMs, aluminum PET is not the only material. It’s just a common substrate for us because the industry is using aluminum. As for OEMs, we are working with some tier one and tier two suppliers in the automotive industry. They are not just interested in using aluminum PET, they’re also interested in using heat sinks, aluminum heat pipes, aluminum cables, and so attaching to those cables becomes critical. Having a solid way to connect to those different aluminum applications is important and we have the solution.
Johnson: Why is aluminum PET so prevalent?
Kadiwala: Aluminum PET is basically a very cheap substrate I want to stress that Mina doesn’t dictate the use of aluminum PET. For Mina, you can solder to aluminum, be it aluminum on PET, aluminum on FR-4, aluminum on anything else, or just plain aluminum for heat sink. Mina enables soldering to aluminum and the applications are endless. It is for heat sinks, automotive, electric car battery connections, automotive electric car battery control boards, and aluminum cables. We have applications using high-speed data cables which have to be grounded, and that’s where Mina comes in.
There’s an application for LEDs, you can solder LEDs to aluminum. Which means they operate cooler, and the life of the LED improves. The main thing is cost. Copper is three times as expensive; you can reduce a lot of your costs if you can change to aluminum, and soldering to aluminum is important.
Johnson: Thanks for the overview. I really appreciate this, and it’s quite interesting.
Kadiwala: You’re very welcome.