-
- News
- Books
Featured Books
- smt007 Magazine
Latest Issues
Current IssueWhat's Your Sweet Spot?
Are you in a niche that’s growing or shrinking? Is it time to reassess and refocus? We spotlight companies thriving by redefining or reinforcing their niche. What are their insights?
Moving Forward With Confidence
In this issue, we focus on sales and quoting, workforce training, new IPC leadership in the U.S. and Canada, the effects of tariffs, CFX standards, and much more—all designed to provide perspective as you move through the cloud bank of today's shifting economic market.
Intelligent Test and Inspection
Are you ready to explore the cutting-edge advancements shaping the electronics manufacturing industry? The May 2025 issue of SMT007 Magazine is packed with insights, innovations, and expert perspectives that you won’t want to miss.
- Articles
- Columns
- Links
- Media kit
||| MENU - smt007 Magazine
Exploring High Density With Axiom
May 6, 2022 | I-Connect007 Editorial TeamEstimated reading time: 3 minutes
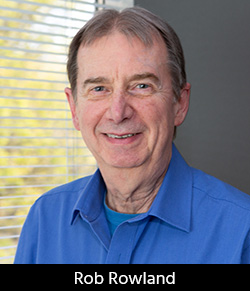
Nolan Johnson and Barry Matties talk with Axiom’s Rob Rowland and Kevin Bennett about the current high-density challenges facing EMS manufacturing. In this interview, Bennett and Rowland zero in on component packaging and feeder technology as critical areas in need of improvement.
Nolan Johnson: Rob, please introduce us to Axiom.
Rob Rowland: Axiom has been an EMS provider for about 30 years. We primarily focus on military, aerospace, space products, and any other high-reliability application type of customers, building the more complex, high-density type of boards. Kevin has been doing placement for over 20 years, both as a machine programmer and a process engineer. We probably handle a wider diversity of unique components than many companies doing board build. Our board sizes range from what you would call a memory module size, up to boards in the 18-by-20-inch size range, so we handle a large variety of different sizes.
Johnson: Is it fair to assume that it’s a mostly high-mix, low-volume setup?
Rowland: Yes. Our expertise is the higher mix, lower volume, with a typical run in the 30- to 50-board range. We have a couple of runs where we’re building in the hundreds, and occasionally into the thousands, but it’s usually jobs fewer than 100 boards. One interesting aspect when talking about placement machines is that most companies in the U.S. are dealing with higher mix, lower volume.
It’s fair to say there’s a big distinction between what you need to do for different production mixes. As I talk with my peers in the industry, one of our biggest challenges for the higher mix, lower volume placement is component packaging.
Packaging—Tape, Reels, and Tubes... Oh My!
Barry Matties: When we talk about packaging, do you mean part of the components?
Rowland: In this case, we’re specifically talking about tape and reel vs. matrix tray vs. tubes. The ideal scenario if you’re running high volumes is to buy full-size reels. When you’re in the high-mix business, you’re typically dealing with much shorter strips of tape, and not all the machines on the market are well-designed to deal with that. It’s a major challenge for domestic companies, and one that the placement industry has not stepped up to address as much as I would like. We had to develop a process that enables us to deal with shorter strips of tape; it’s typically one of our bigger headaches from a board build standpoint.
Johnson: Is that sort of packaging challenge worse when you’re dealing with very small components or is it consistent across the board?
Kevin Bennett: It’s worse when you’re dealing with smaller components, because there are different methods for loading them onto the placement machine. The components are presented in the pockets of the carrier tape with cover tape over the top of each pocket to keep them from falling out. When you have a short strip of tape, there needs to be enough carrier tape length for the feeder to advance correctly. In that case you must prep the strip with an extra length of cover tape, so the mechanism that peels the cover tape back will expose the component for the nozzle to pick from.
If you’re placing short strips of tape on a matrix tray platform, the entire length of cover tape needs to be peeled back before attempting to pick. If the short strip contains small components, a slight bump could cause all the components to come out of the carrier tape with potential loss due to attrition.
To read this entire conversation, which appeared in the May 2022 issue of SMT007 Magazine, click here.
Suggested Items
FTG Announces Q2 2025 Financial Results
07/09/2025 | Globe NewswireFiran Technology Group Corporation announced financial results for the second quarter 2025. Revenue: Recorded at $48.7 million, a 25.6% increase over Q2 2024.
Moog Announces Acquisition of COTSWORKS
07/07/2025 | BUSINESS WIREMoog Inc., a worldwide designer, manufacturer and systems integrator of high-performance precision motion and fluid controls and control systems, announced the acquisition of COTSWORKS Inc., an aerospace and defense fiber optics transceiver component manufacturer, for a purchase price of $63 million.
S&K Aerospace Awarded Major Contract Under DLA Maritime Acquisition Advancement Program
07/02/2025 | BUSINESS WIRES&K Aerospace, LLC has been awarded a significant contract under the Defense Logistics Agency’s (DLA) Maritime Acquisition Advancement Program, managed by the U.S. Naval Supply Command - Weapon Systems Support (NAVSUP WSS) in Mechanicsburg, PA.
Green Circuits to Exhibit Full-Service Electronics Manufacturing Solutions at 2025 SMD Symposium
07/02/2025 | Green CircuitsGreen Circuits, a full-service Electronics Manufacturing Services (EMS) partner to leading OEMs, is pleased to announce its participation in the 2025 SMD Symposium, taking place August 5-7 at the Von Braun Center in Huntsville, Alabama.
I-Connect007 Editor’s Choice: Five Must-Reads for the Week
06/27/2025 | Nolan Johnson, I-Connect007While news outside our industry keeps our attention occupied, the big news inside the industry is the rechristening of IPC as the Global Electronics Association. My must-reads begins with Marcy LaRont’s exclusive and informative interview with Dr. John Mitchell, president and CEO of the Global Electronics Association. For designers, have we finally reached the point in time where autorouters will fulfill their potential?