-
- News
- Books
Featured Books
- pcb007 Magazine
Latest Issues
Current IssueInventing the Future with SEL
Two years after launching its state-of-the-art PCB facility, SEL shares lessons in vision, execution, and innovation, plus insights from industry icons and technology leaders shaping the future of PCB fabrication.
Sales: From Pitch to PO
From the first cold call to finally receiving that first purchase order, the July PCB007 Magazine breaks down some critical parts of the sales stack. To up your sales game, read on!
The Hole Truth: Via Integrity in an HDI World
From the drilled hole to registration across multiple sequential lamination cycles, to the quality of your copper plating, via reliability in an HDI world is becoming an ever-greater challenge. This month we look at “The Hole Truth,” from creating the “perfect” via to how you can assure via quality and reliability, the first time, every time.
- Articles
- Columns
- Links
- Media kit
||| MENU - pcb007 Magazine
Estimated reading time: 4 minutes
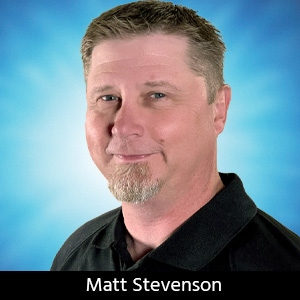
Connect the Dots: Caution—Yield Ahead
Manufacturing yield is a key measure of quality in PCB manufacturing. Measured as a percentage of good parts relative to the total produced, achieving 100% yield rates is extremely challenging for anything but the simplest PCB designs. Most PCB manufacturers produce less than a 95% yield, eating the cost of discards and re-designs. PCB manufacturers can take steps to improve yield rates. It is possible to achieve more than a 98% yield rate by addressing common manufacturing errors, improving safety and quality in tandem, and integrating a Lean approach to all processes.
Addressing Common Errors
Many errors go unnoticed in fabrication and even assembly. Looking out for these during prototyping can catch low yield culprits before production. While testing increases cost and turnaround during prototype iteration, gains in yield rate will offset this in high-volume production.
Keeping these guidelines in mind can accelerate the process:
- Always double-check that your bill of materials components fits your layout footprint. Replacing a component that doesn’t fit its location or size on a board can be costly, if not impossible. Mismatched boards are often unusable.
- Ensure that board materials can withstand the electrical and mechanical demands of your design. Inadequate material can cause failure from thermal or physical stress.
- Don’t try to cut corners when it comes to spacing and clearance. Many PCB layout errors are the result of clearance violations, e.g., inadequate board edge or drill hole clearance. Damaged components are often the result of solder bridging from solder joints being too close together. Look out for additional PCB layout errors like oxidized copper from missing a solder mask or bowing due to copper imbalance.
- Make sure that the flexibility of your boards fits their function. Properly support your flex boards with stiffeners or fixtures to meet their structural requirements and ensure durability. All that said, these practices are only one part of the puzzle.
Using Technology to Improve Accuracy
Holistically addressing manufacturing speed and accuracy is essential to processing a job at very high yields. Using statistical process control (SPC) software, manufacturers can monitor efficiency and pinpoint errors to ensure greater accuracy. Automated engineering furthers consistent precision while also increasing production. This leaves time for highly skilled manufacturers and operators to focus on high-level tasks that utilize their expertise as well as real-time quality control, all of which contributes to competitively high yield production.
Focusing on Quality and Safety
A commitment to quality at every level of organization translates to quality products and is central to successful yield increases. A quality product cannot be sustained without valuing the product’s safety from prototype to customer application. Safety supports quality, and quality ensures safety.
At the risk of sounding obvious, use of high-quality materials ensures a high-quality product and increases yield. Avoid the temptation presented by lower cost materials or design shortcuts as these can produce costly errors. In addition to defective boards, errors can cause worker injuries and reduce your labor force lowering both product quality and yield.
Keeping employees safe is also fundamental to high quality, high yield production. Employees who feel assured of their welfare can focus their attention on top-quality work. Providing employees with places to take breaks to recharge and rest and sustaining robust safety measures promotes employee well-being and investment in their work. Regular equipment maintenance also substantially factors into worker safety and ensures that processes flow smoothly. Working in a safe and low stress environment increases employee loyalty—helping to sustain a stable, expert team motivated to produce quality products.
Implementing a QMS and Adopting Lean Principles
Well-defined operating procedures provide another key component to high yield production. Establishing a quality management system (QMS) and achieving International Organization for Standardization (ISO) 9001 certification signal a high value of quality that stands out in the marketplace. While the cost of time and resources may appear daunting, investing in this process can facilitate a standard of continuous quality improvement. Guaranteeing that your organization adheres to ISO’s certification requirements, specifications, and guidelines translates to consistency and quality for both process and product.
Improved data, generated through a QMS’s consistent documentation, lays the groundwork for evidence-based decision making, providing an informed approach to achievable goals. It can help identify valuable areas for continuous and up-to-date technician training that will enhance skill and renew employee dedication to the task at hand. It also allows for accurate, regular review of processes to remove waste and maintain Lean manufacturing.
Integrating the strategies described here aligns with a Lean manufacturing (Lean) philosophy focused on eliminating any production component that does not deliver value to the customer. This approach requires comprehensive and ongoing process improvement.
Starting from the customer’s need for timely, cost-effective PCBs, a Lean approach to improvement works backward from end product to the beginning of the manufacturing process. It assesses each aspect of the process, seizing opportunities to increase efficiency and getting rid of waste along the way. It requires looking beyond the production floor to make innovative process improvements and committed leadership that sets appropriate expectations at every level. This comprehensive system provides the way forward to accomplish high yield rates that keep up with the increasing complexity of modern technology.
Don’t settle for sub-95% yields. We believe better is possible, and manufacturers who adopt these principles and processes can improve production yield rates.
This column originally appeared in the July 2022 issue of PCB007 Magazine.
More Columns from Connect the Dots
Connect the Dots: Sequential Lamination in HDI PCB ManufacturingConnect the Dots: The Future of PCB Design and Manufacturing
Connect the Dots: Proactive Controlled Impedance
Connect the Dots: Involving Manufacturers Earlier Prevents Downstream Issues
Connect the Dots: Stop Killing Your Yield—The Hidden Cost of Design Oversights
Connect the Dots: Designing for Reality—Routing, Final Fab, and QC
Connect the Dots: Designing for Reality—Surface Finish
Connect the Dots: Designing for Reality—Solder Mask and Legend