-
- News
- Books
Featured Books
- pcb007 Magazine
Latest Issues
Current IssueSales: From Pitch to PO
From the first cold call to finally receiving that first purchase order, the July PCB007 Magazine breaks down some critical parts of the sales stack. To up your sales game, read on!
The Hole Truth: Via Integrity in an HDI World
From the drilled hole to registration across multiple sequential lamination cycles, to the quality of your copper plating, via reliability in an HDI world is becoming an ever-greater challenge. This month we look at “The Hole Truth,” from creating the “perfect” via to how you can assure via quality and reliability, the first time, every time.
In Pursuit of Perfection: Defect Reduction
For bare PCB board fabrication, defect reduction is a critical aspect of a company's bottom line profitability. In this issue, we examine how imaging, etching, and plating processes can provide information and insight into reducing defects and increasing yields.
- Articles
- Columns
- Links
- Media kit
||| MENU - pcb007 Magazine
The Growing Need for UHDI
November 30, 2022 | I-Connect007 Editorial TeamEstimated reading time: 3 minutes
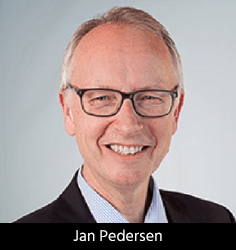
Jan Pedersen of NCAB Group is deeply involved in IPC standards development surrounding ultra HDI and keeps his finger on the pulse of the industry surrounding this type of fabrication. With Asia still dominating this area, Jan sees the need for U.S. and European PCB fabricators to make the investment if they want to stay competitive.
Nolan Johnson: Jan, you’re very involved in UHDI design and manufacturing. What’s your perspective on these topics within the industry now, and where UHDI is going?
Jan Pedersen: There are seven to 10 factories globally that can produce what we call ultra HDI. The definition for UHDI is 50-micron and below track and gap. You can use subtractive methods down to, let’s say, 35 or 40 microns, and then when you creep down below that level you need mSAP or xSAP technologies.
That has been around for many years. It’s not really a new technology. It was introduced into the packaging or the component industry in the 1970s and ‘80s, but it was brought up again when Apple and others started to do smartphones. There are those factories that are involved in this, but they are factored for one customer, so it’s very hard for a smaller customer to get into UHDI, and most companies are smaller than Apple.
If you are a bit smaller, you don’t get access. It’s simple as that. I’ve tried it myself, tried to place an order with a big European PCB group that claims they have the capability. But when you have your Gerbers and your data and you want to produce boards there, they say, “Oh, sorry. This is basically for one customer,” and they don’t accept us putting their competitors, which could be anybody, into the same factory.
Johnson: Given that, what is driving the development of UHDI?
Pedersen: For us, it’s coming from telecom and 5G, and you assume we’ll see 6G. But quite a few of our customers come from these industries. We see that need growing in the automotive and medical industries, and I’m discussing it almost globally. I’m looking to see if there is any availability of production capabilities in the U.S. today. We don’t find it. There’s one factory in Europe that has limited capacity, and then the rest are in Asia and producing for the big names.
Johnson: Where does HDI stop and UHDI begin?
Pedersen: Let’s use the ultra HDI definition of 50 microns down. It’s subtractive down to approximately 40 microns.
Where we are today approximately on BGA pitch below 350 microns, we talk about pads of 140, and then you are basically into mSAP or substrate-like PCB technologies, whatever that is. There are quite a few technologies out there now that can be used. But we see that we are going from a subtractive into an mSAP level; this depends on where you are coming from and how far you are coming with the investments in your factory, because some of the factories that are producing mSAP have invested in imaging, AOI—everything needed for that resolution now.
When you have a subtractive in that factor, they can go quite far down here. But if you don’t have all the other investments and just go for mSAP, that doesn’t help you.
I’m saying this as background because you have this producibility level C in IPC-2226, where you have 50-micron track and gap. Everything below that is ultra HDI—substrate-like PCBs can be produced by either subtractive or SAP-related technologies. If you go below that again, down to 15 to 20 microns, you need an embedded trace substrate or similar technologies. Then of course you come to high-end IC substrates which are in single microns.
In the U.S. today for substrate-like PCB, it’s below 50 microns, not touching 20 microns, but maybe 35 or 40. When I had my Gerbers and asked for quotations, they said they couldn’t do it. They do have mSAP equipment, if you can call it that, or a process in-house, but have not yet invested in the imaging and AOI that is able to detect down to 20 microns. I think they stop somewhere around 35 today.
To read this entire conversation, which appeared in the November 2022 issue of PCB007 Magazine, click here.
Testimonial
"In a year when every marketing dollar mattered, I chose to keep I-Connect007 in our 2025 plan. Their commitment to high-quality, insightful content aligns with Koh Young’s values and helps readers navigate a changing industry. "
Brent Fischthal - Koh YoungSuggested Items
Creating Connections in Mexico
07/30/2025 | Michelle Te, Community MagazineA concerted effort by the Global Electronics Association—Mexico team over the past year has created inroads for the Global Electronics Association (formerly IPC) with leading electronics companies, government offices, and academic institutions in Mexico. “Our goal is to bring more awareness to what the Global Electronics Association is and what it offers,” says Lorena Villanueva, senior director. “We also aim to increase our membership. Of 3,200 members of the Global Electronics Association, only 180 are in Mexico.”
Powering Progress: Summer 2025 Community Magazine Now Available
07/22/2025 | Community MagazineIn the new Summer 2025 edition of Community Magazine, members of the Global Electronics Association demonstrate what progress really looks like—through innovation on the factory floor, influence on public policy, and investment in the next generation of engineers.
TRI to Exhibit at SMTA Queretaro Expo 2025
07/16/2025 | TRITest Research, Inc. (TRI), the leading provider of test and inspection systems for the electronics manufacturing industry, is pleased to announce plans to exhibit at the SMTA Querétaro Expo 2025, scheduled to take place on July 24, 2025, at the Querétaro Centro de Congresos y Teatro Metropolitano.
Global PCB Connections: Let the Spec Fit the Board, Not Just the Brand
07/17/2025 | Jerome Larez -- Column: Global PCB ConnectionsIf you’ve ever seen an excellent PCB quote delayed, or worse, go cold because of a single line on the fab print, you’re not alone. Often, that line reads something like, “Use 370HR only,” or “IT-180A required.” These and other brand-name materials are proven performers, but unless your design needs that specific resin system (say, for RF performance, thermal reliability, or stringent CAF resistance), you may inadvertently be holding your job hostage.
IPC Hall of Fame Spotlight Series: Highlighting Lionel Fullwood
07/15/2025 | Dan Feinberg, I-Connect007Many IPC members who have contributed significantly to IPC and our industry have been awarded the IPC Raymond E. Pritchard Hall of Fame (HOF) Award. Though many early HOF members have passed away and are unknown to today’s IPC membership, their contributions still resonate. This special series on IPC Hall of Fame members provides a reminder of who was honored and why. As a bonus, for those who are still around, we get to find out what these talented individuals are up to today.