-
- News
- Books
Featured Books
- smt007 Magazine
Latest Issues
Current IssueMoving Forward With Confidence
In this issue, we focus on sales and quoting, workforce training, new IPC leadership in the U.S. and Canada, the effects of tariffs, CFX standards, and much more—all designed to provide perspective as you move through the cloud bank of today's shifting economic market.
Intelligent Test and Inspection
Are you ready to explore the cutting-edge advancements shaping the electronics manufacturing industry? The May 2025 issue of SMT007 Magazine is packed with insights, innovations, and expert perspectives that you won’t want to miss.
Do You Have X-ray Vision?
Has X-ray’s time finally come in electronics manufacturing? Join us in this issue of SMT007 Magazine, where we answer this question and others to bring more efficiency to your bottom line.
- Articles
- Columns
Search Console
- Links
- Media kit
||| MENU - smt007 Magazine
Filling Critical Traceability Gaps With AI
June 28, 2023 | CybordEstimated reading time: 3 minutes
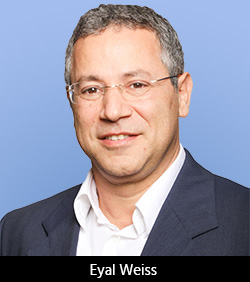
Traceability means being able to track the origin of any given electrical component throughout the supply chain. For OEMs, this is no longer optional or “nice to have.” Yet industrial traceability capacities are sorely lacking throughout industries.
Today, the most widespread standard for traceability is “batch traceability,” which aside from tracking the production lot, serial number, and exact board placement for components, fails to analyze the individual components themselves, thus jeopardizing the quality of the goods they compose.
Faulty components are unavoidable. For components that make it into circulation and harbor some kind of defect, the result can easily cascade into sweeping recalls that waste time, money, and resources.
Instead, electronics manufacturers need to be able to facilitate recalls much more surgically. But that can only be achieved through exploratory traceability: new processes that employ precise, detailed, and exacting visual identification of every electronic component placed on a PCBA.
Original equipment manufacturers have an opportunity to improve traceability with AI tools and big data, closing the information gaps that plague tech products across the supply chain.
Where Lies the Fault?
Because eight out of 10 failures are attributed to faulty components rather than faulty workmanship, most manufacturers view traceability as essential. After all, it allows them to operate in markets that demand a detailed trail for every part on every board. Consider military defense systems, automotive software, and medical technologies, where consequences of a malfunction can be dire.
Unfortunately, supply chain disruptions, especially in the wake of the pandemic, muddied the waters. Average manufacturing lead times increased from three and a half months to nearly a year, forcing OEMs to circumvent their standard suppliers and source components from alternative suppliers, often with improper storage standards and subpar materials, as well as mixed lots and ambiguous traceability information.
Although the negative impacts of supply chain slowdowns on electronic components have diminished, assuming there are zero defects across thousands upon thousands of components would be wrong-minded. Given that defective and counterfeit components remain, manufacturers should raise their traceability standards to boost quality, output efficiency, and financial clarity, all of which help strengthen the bottom line. Leveraging AI to do this offers the path of least resistance.
The Root of the Problem
Many industry leaders appreciate AI’s capacity to improve various phases of the manufacturing process, but often miss its potential impact on the traceability capabilities of individual components.
Presently, there are several levels of traceability across various industries. In the first level, monitoring relevant equipment parts in the manufacturing value chain is conducted inconsistently. The next two levels involve the use of serial numbers to match PCBs to their associated batch. The fourth and highest level monitors the actual placement of the components onto PCBs. However, this maximum level of traceability incorrectly assumes that all components within a reel are exactly the same, and therein lies the root of the problem.
Level Up
Though Level 4 reflects the highest industry standard, many companies have yet to upgrade traceability beyond the first and second tiers; this leads to troublesome gaps in their visibility. Moreover, current lab testing processes are woefully ineffective in identifying compromised material, as they rely solely on sampling a smattering of components out of thousands.
OEMs should strive to extend their traceability standards beyond Level 4 to attain complete exploratory traceability. AI-powered visual technology can enable this heightened level of traceability, offering a far more efficient and cost-effective solution than lab testing batches of components. Regardless of where components are sourced, visual recognition powered by AI can rapidly analyze every component on every board for authenticity and component integrity without concern for human error. When implemented, manufacturers can pinpoint any problematic component and conduct rapid surgical recalls on an individual basis with minimal disruption to the manufacturing process.
Just as doctors administer blood tests to assess a patient’s health, OEMs need to take the same approach to each and every electronic component. Luckily, AI can transform this otherwise Sisyphean task into one that is far more efficient and manageable.
No Extra Hardware Necessary
The manufacturing industry needs to embrace AI tools if they truly wish to pioneer air-tight 4A traceability toward a more intelligent, efficient, and cost-effective future. All it takes is a SaaS integration with their existing SMT hardware to gain true visibility into what is going on in their products.
Dr. Eyal Weiss is CTO and founder of Cybord.
This article originally appears in the June 2023 issue of SMT007 Magazine.
Suggested Items
Intervala Hosts Employee Car and Motorcycle Show, Benefit Nonprofits
08/27/2024 | IntervalaIntervala hosted an employee car and motorcycle show, aptly named the Vala-Cruise and it was a roaring success! Employees had the chance to show off their prized wheels, and it was incredible to see the variety and passion on display.
KIC Honored with IPC Recognition for 25 Years of Membership and Contributions to Electronics Manufacturing Industry
06/24/2024 | KICKIC, a renowned pioneer in thermal process and temperature measurement solutions for electronics manufacturing, is proud to announce that it has been recognized by IPC for 25 years of membership and significant contributions to electronics manufacturing.
Boeing Starliner Spacecraft Completes Successful Crewed Docking with International Space Station
06/07/2024 | BoeingNASA astronauts Barry "Butch" Wilmore and Sunita "Suni" Williams successfully docked Boeing's Starliner spacecraft to the International Space Station (ISS), about 26 hours after launching from Cape Canaveral Space Force Station.
KIC’s Miles Moreau to Present Profiling Basics and Best Practices at SMTA Wisconsin Chapter PCBA Profile Workshop
01/25/2024 | KICKIC, a renowned pioneer in thermal process and temperature measurement solutions for electronics manufacturing, announces that Miles Moreau, General Manager, will be a featured speaker at the SMTA Wisconsin Chapter In-Person PCBA Profile Workshop.
The Drive Toward UHDI and Substrates
09/20/2023 | I-Connect007 Editorial TeamPanasonic’s Darren Hitchcock spoke with the I-Connect007 Editorial Team on the complexities of moving toward ultra HDI manufacturing. As we learn in this conversation, the number of shifting constraints relative to traditional PCB fabrication is quite large and can sometimes conflict with each other.