Estimated reading time: 4 minutes
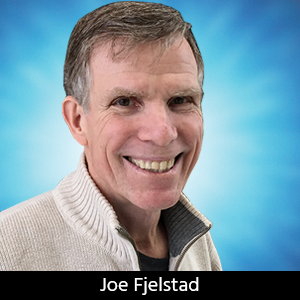
Flexible Thinking: Unlocking the Key to Rigid-flex Design Success
Despite what some seem to believe, rigid-flex circuits are not a new technology. In fact, they are more than a half-century old. At the time of the invention, my friend Thomas Sterns was working at Sanders Associates, the pioneering flex circuit manufacturer. Like many products in the first decades of printed circuit technology, they were working on a military application. The objective was to provide a reliable method for reducing the size, bulk, weight, and questionable reliability of wire harness assemblies while simultaneously reducing cost and assuring that human error might be minimized. These were all vitally important concerns for military and aerospace products.
I’m reminded of a statement from U.S. Navy Capt. Frank Akers:
“Today with the modern high-performance airplane, electronics is a must if we are to get the benefit of the tremendous performance available. We have made electronics equipment smaller, have made it lighter, and we have made it work. Printed circuits, (have been) the greatest weight and space saver of them all.”
While this sounds like a recent comment, Capt. Akers actually spoke these words in 1947, more than 75 years ago. It tells me that while the key design objectives of rigid-flex are largely unchanged, the technology—and diversity of applications—has advanced steadily. Knowing that rigid-flex circuits are an option, designers have been (with ever greater frequency) looking to rigid-flex technology to help them solve vexing interconnection problems. Most notably, and perhaps with some surprise, rigid-flex circuits have enabled a substantial percentage of the advances we have seen in smartphones and other portable electronic products. Even though most smartphones don’t have foldable screens, there are myriad interconnections required between the various features of the modern smartphone: camera, screen, speaker, microphone, GPS, gyroscope, memory storage, and yes, the telephone.
While original rigid-flex circuit designs sought to minimize the number of connectors, the number of low-profile flex connectors found in modern cellphones is impressive. Assembly appears to involve a lot of delicate handwork, which doubtless contributes to cost. Watching a few YouTube video teardowns helps me appreciate just how important it is to build in product reliability for these amazing products because rework is clearly not an inexpensive activity.
The adage, “Knowledge is king,” is imperative when it comes to rigid-flex design. The importance cannot be understated that we must fully understand the intricacies of rigid-flex manufacturing in advance of setting out to design such a product.
Many useful articles and publications on rigid-flex circuits exist online, including on manufacturers’ websites, all aiming to educate their customers and for the greater benefit. Most rigid-flex manufacturers have instructive websites and self-published books in some cases. I highly encourage you to visit the eBook library at I-Connect007, where you’ll find a wide range of topics published by subject matter experts. Tap into this resource and greatly expand your knowledge.
One of the best ways to avoid potential pitfalls is to engage with the manufacturer early in the design process. In a previous column, I wrote about the increasing importance of making the manufacturer part of the design team. There are many “design for” recommendations out there: design for environment (or excellence), design for testing, design for reliability, and as mentioned, design for manufacturing. But designing with manufacturing may be the most important design advice of all. Often, the manufacturer has “seen it all” and, if consulted early in the design process, can greatly increase your chances of first-pass design success. That “seen it all” idea reminds me of a comment from John Wooden, the Hall of Fame basketball coach from UCLA, who said, “It’s what you learn after you know it all that counts.” That was an important reminder as this technology has never stood still; it has continued to change and evolve. Because they are so close to the flow, the manufacturer will typically be a great source of guidance.
In conclusion, while often seen as an expensive interconnection technology alternative due to the higher degree of engineering required to produce it, rigid-flex circuits in the long run can be a much more cost-effective solution. Reducing the size, weight, and power (SWaP) requirements of products will always be overarching objectives in product development, and are intrinsic benefits of rigid-flex circuits. However, many buyers don’t often appreciate that it’s not just cost in, but cost out the door that must be considered when making purchase decisions.
Repackaging and condensing the words and thoughts of some historically great quality gurus of the industry, in general, I now conclude (at least to my own satisfaction) that to succeed in product design, rigid-flex, or any other product, one must first do the right things and then do those things right. Enjoy your rigid-flex design journey, and stay flexible.
This column originally appeared in the September 2023 issue of Design007 Magazine.
More Columns from Flexible Thinking
Flexible Thinking: The Key to a Successful Flex Circuit Design TransferFlexible Thinking: Flexible Circuit Technology—Looking Back and Forward
Flexible Thinking: Mind-tapping into January
Flexible Thinking: Another PCB Design Paradigm Shift in the Works
Flexible Thinking: Rules of Thumb—A Word to the Wise
Flexible Thinking: Musings on High Density Interconnections
Flexible Thinking: Integrated Passive Devices—Design Solutions With Many Benefits
Flexible Thinking: Mechatronics in a Flex World