-
- News
- Books
Featured Books
- pcb007 Magazine
Latest Issues
Current IssueInventing the Future with SEL
Two years after launching its state-of-the-art PCB facility, SEL shares lessons in vision, execution, and innovation, plus insights from industry icons and technology leaders shaping the future of PCB fabrication.
Sales: From Pitch to PO
From the first cold call to finally receiving that first purchase order, the July PCB007 Magazine breaks down some critical parts of the sales stack. To up your sales game, read on!
The Hole Truth: Via Integrity in an HDI World
From the drilled hole to registration across multiple sequential lamination cycles, to the quality of your copper plating, via reliability in an HDI world is becoming an ever-greater challenge. This month we look at “The Hole Truth,” from creating the “perfect” via to how you can assure via quality and reliability, the first time, every time.
- Articles
- Columns
- Links
- Media kit
||| MENU - pcb007 Magazine
Estimated reading time: 4 minutes
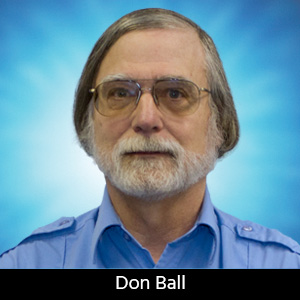
The Chemical Connection: The High Cost of Etcher Non-maintenance
We all understand that day-to-day maintenance and long-term preventive maintenance of etching equipment is a good thing. However, the pressing need to get product out the door in the face of tough production schedules can sometimes cause us to delay necessary maintenance for long periods of time. In some cases, we become fixated on short-term production and forget about long-term stability. This can end up costing a fair amount of money in terms of repairs and lost production, most of which could have been prevented by taking the time to do some simple checks on equipment operation and chemistry conditions.
For example, I received a call from a customer some years ago complaining that his cupric chloride etcher had stopped etching. The Friday before the call, the etch rate started to drop off rapidly so they had to slow the conveyor speed continually. The following Monday, the etcher was slow to heat up and when the pumps were turned on there was virtually no spray pressure even though the pump valves were wide open.
A few questions established that the color of the cupric was a bright green with an oxidation/reduction potential of over 900 mv but no chlorine odor. This was a bit of a surprise. I was expecting to hear that the color was almost black and the ORP down around the lower 500s, indicating a problem with the etchant regeneration, and accounting for the slowing etch rate. Also, with the ORP in the 900s, there should have been at least a strong chlorine smell around the etcher even if it wasn’t enough to cause the room to be evacuated.
I had a sneaking suspicion about the problem and asked if they had the capability do a free acid titration. They did and their chemist reported that the titration showed almost no free acid. This meant that the cuprous chloride byproduct from the etch reaction was not being kept in solution by the free acid and was precipitating to the bottom of the etch sump. The ORP, which is a ratio of cupric ions to cuprous ions in the etch bath, continued to increase as cuprous ions were removed from the etch solution. Thus, the regeneration unit did not add oxidizer or HCl to the system to regenerate the cuprous ions back to cupric ions. As the concentration of cupric ions decreased, so did the etch rate. Over the weekend, as the bath cooled down, any remaining cuprous chloride finished precipitating out of the etch solution to the bottom of the etcher sump, blocking the pump intakes.
Why did the free acid drop so much? The maintenance person responsible for checking the acid supply drum for the regeneration system took that Friday off and no one else was responsible for checking the drum. By the time the problem was diagnosed, and remedies taken to redissolve the cuprous chloride and bring the chemistry back into specifications, the customer lost four days of production simply because they did not have a maintenance protocol to check the free acid level at least once in the morning and once in the early afternoon.
A somewhat similar problem occurred a few months ago to a customer etching copper and steel using ferric chloride as the etchant. We got a panicked call one day saying that the heaters in the etcher had “blown up” and they needed someone there immediately to identify the problem and fix it.
The problem was evident once the ferric chloride was removed from the etcher. There was six inches of muddy brown sludge in the bottom of the sump that covered the heaters, causing them to overheat and short out in a rather spectacular fashion.
Ferric chloride is a dirty etchant when etching copper and steel alloys. The sludge consisted mostly of insoluble metallic chlorides from the alloying metals in the steel. Free acid levels are difficult to determine in ferric because the alloying metals interfere with the acid titration. Even when the free acid levels are properly maintained there are always insoluble chlorides precipitating from the etch solution to the bottom of the sump.
It is generally recommended that the etcher be drained at least once a month and the bottom of the sump hosed out. In this case, the etchant was used as long as possible, then drained and the sump filled with new etchant but without hosing out the bottom (it took too long). More than a week of production was lost simply because they did not want to spend an extra 10 minutes cleaning out the bottom of the etch sump every time they refilled the etcher with fresh etchant.
And so it goes. Every equipment supplier can probably come up with many stories of major problems and expenses caused by failure to do even minimal equipment maintenance in the name of getting more product out the door.
The time spent devising and running even a minimal daily check and maintenance protocol will quickly pay for itself by reducing downtime caused by easily preventable failures. It may be difficult to think about draining the swamp when you’re up to your butt in alligators; just remind yourself that when the swamp is drained, the alligators tend to disappear.
This column originally appeared in the December 2023 issue of PCB007 Magazine.
More Columns from The Chemical Connection
The Chemical Connection: Sales Organization from a Capital Equipment PerspectiveThe Chemical Connection: Through-glass Vias in Glass Substrates
The Chemical Connection: Reducing Defects in Circuit Board Production
The Chemical Connection: Common Misconceptions in Wet Processing
The Chemical Connection: Surface Finishes for PCBs
The Chemical Connection: Earthquakes, Astronauts, and Aquatics—A Lighter Look at the Past
The Chemical Connection: Better Fabs Attract a Better Workforce
The Chemical Connection: Can Changing Spray Nozzles Improve My Etch Quality?