-
- News
- Books
Featured Books
- pcb007 Magazine
Latest Issues
Current IssueIn Pursuit of Perfection: Defect Reduction
For bare PCB board fabrication, defect reduction is a critical aspect of a company's bottom line profitability. In this issue, we examine how imaging, etching, and plating processes can provide information and insight into reducing defects and increasing yields.
Voices of the Industry
We take the pulse of the PCB industry by sharing insights from leading fabricators and suppliers in this month's issue. We've gathered their thoughts on the new U.S. administration, spending, the war in Ukraine, and their most pressing needs. It’s an eye-opening and enlightening look behind the curtain.
The Essential Guide to Surface Finishes
We go back to basics this month with a recount of a little history, and look forward to addressing the many challenges that high density, high frequency, adhesion, SI, and corrosion concerns for harsh environments bring to the fore. We compare and contrast surface finishes by type and application, take a hard look at the many iterations of gold plating, and address palladium as a surface finish.
- Articles
- Columns
Search Console
- Links
- Media kit
||| MENU - pcb007 Magazine
Estimated reading time: 5 minutes
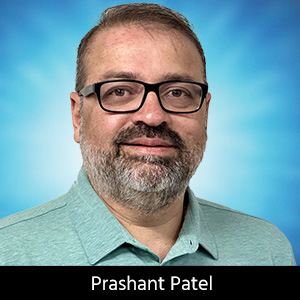
Facing the Future: Technology Trends Shaping the PCB Market
Each year the PCB market brings innovations, challenges, and opportunities that redefine the playing field. To remain competitive, North American PCB shops must adapt to these trends and leverage them to carve out an advantage. I’ll be exploring the technology trends shaping the PCB market and how can help North American manufacturers thrive in a rapidly evolving industry.
Adopting Advanced Materials
High density interconnect (HDI) and RF/microwave PCBs represent the backbone of modern electronics. HDI PCBs, with their higher circuit density, thinner traces, and microvias, cater to the shrinking form factors of today’s devices. From smartphones to Internet of Things (IoT) sensors, these materials allow for cutting-edge performance in compact designs. RF/microwave PCBs are also indispensable in applications requiring high-frequency transmission, such as radar systems, aerospace communications, and 5G infrastructure. The growing demand for these materials reflects a shift to more specialized and high-performance electronics.
North American PCB shops need to invest in the capabilities to handle these materials, be it ensuring advanced etching precision for HDI or mastering the lamination requirements of RF substrates like PTFE. Shops that specialize in advanced materials can position themselves as leaders in niche markets that demand high quality and reliability.
AI and Automation in PCB Manufacturing Processes
AI and automation are revolutionizing PCB manufacturing, creating a highly efficient process. From predictive maintenance in manufacturing equipment to automated inspection for defects, AI-driven solutions are improving yield rates while reducing costs. AI-powered design tools enable more complex PCB layouts by optimizing routing and minimizing electromagnetic interference. In manufacturing, machine learning algorithms analyze data in real-time to predict and prevent production errors, resulting in faster turnaround times and higher-quality boards.
Automation is also reducing the dependence on manual labor, especially in repetitive tasks like drilling, plating and testing. This not only improves consistency but also allows manufacturers to scale operations with minimal increases in overhead.
North American manufacturers can use AI and automation to bridge the cost gap with overseas competitors. By leveraging these technologies, they can focus on providing quicker prototyping services and exceptional quality—areas where automation excels.
IoT and Wearable Technologies in PCB Design
IoT and wearable technologies are revolutionizing PCB designs. These applications demand compact, lightweight, and efficient boards that can operate in a variety of environmental conditions. IoT devices often require multi-layered PCBs with minimal power consumption to extend battery life. Similarly, wearables such as fitness trackers and medical monitoring devices, demand flexible and biocompatible PCBs that can seamlessly integrate with the human body.
These trends are pushing the boundaries of design and material innovation. PCB manufacturers are now tasked with creating boards that not only meet performance standards but also adhere to strict size and weight limitations. Moreover, the integration of sensors and wireless communication modules into these boards requires collaboration between designers and fabricators.
North American shops can set themselves apart by providing expertise in these emerging areas. By aligning with designers early in the product development cycle, they can ensure that the manufacturing processes and materials selected meet the unique demands of IoT and wearable applications.
5G and Its Demands on PCB Capabilities
5G technology is perhaps the most significant driver of change in the PCB industry. 5G networks demand PCBs with higher signal integrity, better thermal management, and the ability to handle higher frequencies. This has led to a demand for materials with low dielectric constants and high thermal conductivity.
Manufacturers must also contend with the challenges of producing boards with precise impedance control and reduced signal loss. Multi-layered PCBs with specialized stack-ups are increasingly common in 5G applications, from base stations to consumer devices.
Addressing these demands requires investment in both equipment and expertise. However, the rewards are substantial, as the 5G market represents a high-growth sector with applications spanning telecommunications, automotive, and industrial automation. By staying at the forefront of 5G-related innovations, North American manufacturers can tap into lucrative opportunities while demonstrating their commitment to cutting-edge technology.
Emerging Flexible and Rigid-Flex PCB Technologies
Flexible and rigid-flex PCBs are becoming mainstream in the automotive, aerospace, and healthcare industries. These boards offer space savings, durability in dynamic environments, and conform to unconventional shapes.
The growing adoption of electric vehicles (EVs) and advanced medical devices has accelerated the demand for flexible and rigid-flex PCBs. For example, EVs require compact, lightweight boards to reduce vehicle weight, while medical devices benefit from flexible circuits that improve patient comfort.
North American PCB shops can leverage this trend by investing in the capabilities to produce these advanced boards, including mastering the challenges of manufacturing, such as controlling material stress during bending and ensuring reliable soldering on flexible substrates. Moreover, flexible and rigid-flex PCBs often require collaboration between designers and manufacturers to achieve optimal performance. By positioning themselves as collaborative partners, North American shops can secure a competitive edge in this growing market.
How North American Shops Can Stay Competitive With Developing Tech
Adapting to these technological trends is an opportunity for North American PCB manufacturers to distinguish themselves in the global market. Here are some strategies to remain competitive:
- Specialization: Focusing on niche markets, such as RF/Microwave or rigid-flex PCBs, can help shops command premium prices and build long-term customer relationships.
- Invest in talent: Advanced technologies require skilled engineers and technicians. By prioritizing training and hiring, manufacturers can build a workforce to manage complex projects.
- Collaborate early: Partnering with designers during the early stages of product development allows manufacturers to influence design decisions that impact manufacturability and cost.
- Leverage proximity: North American shops can capitalize on their proximity to domestic customers by offering faster turnaround times and superior customer service.
- Adopt green practices: Sustainability is a key differentiator. By adopting eco-friendly manufacturing processes and materials, shops can appeal to environmentally conscious customers.
The PCB market is growing at an unprecedented pace, driven by advancements in materials, manufacturing processes, and end-user applications. For North American manufacturers, these trends present both challenges and opportunities. By embracing advanced materials like HDI and RF/Microwave PCBs, leveraging AI and automation, and focusing on high-growth sectors like IoT, wearables, and 5G, North American shops can remain relevant and thrive in a competitive landscape.
As technology reshapes the industry, the ability to adapt, innovate, and collaborate will define tomorrow’s leaders. North American PCB manufacturers have the tools and potential to turn technological challenges into opportunities for growth and success.
Prashant Patel is the founder and president of Alpha Circuit.
More Columns from Facing the Future
Facing the Future: Investing in R&D to Stay CompetitiveFacing the Future: The Role of 5G and Beyond in Shaping PCB Demand
Facing the Future: Successfully Navigating the Uncertain Path Ahead
Facing the Future: The Evolution of the North American PCB Industry
Facing the Future: Charting the Path Forward for the American PCB Industry