-
- News
- Books
Featured Books
- pcb007 Magazine
Latest Issues
Current IssueInventing the Future with SEL
Two years after launching its state-of-the-art PCB facility, SEL shares lessons in vision, execution, and innovation, plus insights from industry icons and technology leaders shaping the future of PCB fabrication.
Sales: From Pitch to PO
From the first cold call to finally receiving that first purchase order, the July PCB007 Magazine breaks down some critical parts of the sales stack. To up your sales game, read on!
The Hole Truth: Via Integrity in an HDI World
From the drilled hole to registration across multiple sequential lamination cycles, to the quality of your copper plating, via reliability in an HDI world is becoming an ever-greater challenge. This month we look at “The Hole Truth,” from creating the “perfect” via to how you can assure via quality and reliability, the first time, every time.
- Articles
- Columns
- Links
- Media kit
||| MENU - pcb007 Magazine
Estimated reading time: 4 minutes
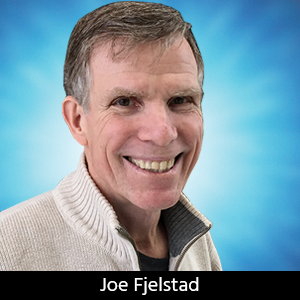
Flexible Thinking: Supporting Components on Flex Circuit Assemblies
The support of components on flexible circuit assemblies is recommended practice. This is typically accomplished by the use of stiffeners which serve to reinforce those areas where components are placed--improving interconnection reliability. Such reinforcements can be fabricated from a variety of different materials depending on the particular demands of the design. Material selection is influenced by a number of different factors related to weight, physical and thermal properties and, of course, cost. Examples of the different types of materials that have been pressed into service as stiffeners include: Resin-glass laminates, thermoplastic sheet material, stainless steel, injection molded bases, beryllium copper, anodized aluminum, quartz glass and extra layers of cover layer. However, the choices are not so limited, the package or box into which the circuit is to be placed can also be used to serve as the stiffener if desired and planned for, but rework will likely be limited.With proper planning, stiffeners can be designed to aid assembly through the designed manufacture of a flex circuit that can be handled as if it were a rigid circuit board. Such constructions can be accomplished by using any one of several methods. One common method is the "route and retain" construction approach, where stiffeners are fabricated by NC routing a reinforcement substrate so as to make is easy to detach after assembly, as illustrated in the figure below. While NC routers are pervasively used in circuit manufacturing, lasers and water jet cutters are potential alternative tools for preparing or pre-cutting stiffeners.Return to web punching (also referred to as "punch out, punch in") is also possible. This approach involves creating the stiffener using special punch tooling which punches the rigid material required for the stiffener and then immediately pushed or punched back into it original position in the panel. The method has seen much use for inexpensive rigid boards and allows mass assembly with relatively simple assembly fixture requirements.Another alternative suitable to flex circuit designs which have been laid out rectilinearly, is to use scoring or dicing tools to prepare the stiffener panel. In the scoring process, the circuit and/or the stiffener is cut partially through using special tools cut a controlled depth straight path through the rigid material alone or through both flex circuit and rigid base. After assembly the circuits can then be snapped apart along the score lines.Stiffeners which are not integral parts of the construction (e.g. fully integrated rigid and flex circuit constructions) must be bonded to the flexible circuit. The bonding adhesives normally used in the manufacture of flexible circuit laminates are commonly the adhesives of first choice for attaching a flex circuit to a stiffener. The ultimate choice of adhesive is, however, typically a function of the assembly process or circuit performance requirements. The designer should check with the flex circuit vendor for his recommendations based on requirements.In day to day practice, pressure sensitive adhesives (PSAs) are commonly used to attach stiffeners. PSAs are perhaps the most versatile and easiest to use and they exhibit very good bond strength, which, in some cases, actually improves with age. PSAs are not generally designed for extended use at high temperatures, but, for the most part, limited to enduring only short excursions at high temperatures (e.g. traditional tin-lead soldering temperatures). However, lead-free solders typically require much higher temperatures so there is need to identify and use only those materials which can perform at elevated temperatures.One singular advantage which PSAs offer over other adhesive choices is that, when applied directly to the flex circuit, they allow for the flex circuit to be bonded to virtually any surface, thus effectively making anything in the package a potential stiffener.Other than PSAs, thermosetting adhesive bonding films (i.e. cast acrylic films or flex circuit bond plies) are also common and can also be used to bond flex circuits to stiffeners, but they require the time and expense of an additional lamination step at temperature. Even so, thermosetting film adhesives of suitable formulations can offer very high bond strength of the flex to the stiffener.Other possible solutions include one- and two-part liquid epoxy type adhesives, however, they are difficult to apply uniformly and, thus, they do not enjoy wide popularity. Liquid adhesive materials do have the intrinsic ability to form a bead at the edge of the stiffener which is useful as a strain relief at the transition edge of the flex and stiffener. Thermoplastic based adhesive films can also be used for bonding flex circuits to stiffeners. Thermoplastic films have some unique advantages among adhesives as they are low stress, fully polymerized polymer resins that require no curing. They offer good adhesion to a wide variety of surfaces and materials, and the reported ability to be reworked easily, may result in these adhesive materials seeing expanded service in the future.In conclusion, stiffeners are commonly an important feature element in a flex circuit design and construction. With proper planning, the stiffener can not only support the components, but also provide additional benefits as an assembly aid.
Verdant Electronics Founder and President, Joseph (Joe) Fjelstad, is a four-decade veteran of the electronics industry and an international authority and innovator in the field of electronic interconnection and packaging technologies with more than 250 U.S. and international patents issued or pending. He is also the author of "Flexible Circuit Technology" and author, co-author or editor of several other books and more than 300 technical papers, articles and columns. To contact Joe, click here.
Follow I-Connect007 on Twitter here.
More Columns from Flexible Thinking
Flexible Thinking: The Key to a Successful Flex Circuit Design TransferFlexible Thinking: Flexible Circuit Technology—Looking Back and Forward
Flexible Thinking: Mind-tapping into January
Flexible Thinking: Another PCB Design Paradigm Shift in the Works
Flexible Thinking: Rules of Thumb—A Word to the Wise
Flexible Thinking: Musings on High Density Interconnections
Flexible Thinking: Integrated Passive Devices—Design Solutions With Many Benefits
Flexible Thinking: Mechatronics in a Flex World